Predictive maintenance (PdM) is a proactive approach to maintenance that uses machine data, AI and ongoing condition monitoring of equipment to identify irregularities and predict when equipment failure is likely to occur so maintenance can be scheduled and performed before a breakdown happens.
Since Predictive maintenance is used to predict when equipment failure is likely to occur, reliability engineers and their teams can plan around this, and schedule maintenance to fix these issues, preventing unplanned downtime and unexpected costs.
Definition of Predictive Maintenance
Predictive maintenance (PdM) is a technique that involves continuously monitoring the condition of a machine and analyzing parameters to gain insights into machine health and performance, predicting when it could fail and prevent downtime.
Common conditions monitored in PdM are vibration and temperature. However Nanoprece goes a step further with their Energy Centric Predictive Maintenance (ECPdM) Solution that measures:
- VIbration
- Temperature
- Acoustic Emission
- Magnetic Flux
- Humidity
- True RPM
Condition Monitoring vs Predictive Maintenance
Although used in tandem, condition monitoring and predictive maintenance are not the same. Condition monitoring is a part of Predictive Maintenance.
Condition Monitoring
The process of continuously or periodically measuring the condition of equipment. It focuses on data collection through asset and equipment monitoring. This data collection can be part of a larger predictive maintenance tool. However, it will not always predict when a failure will occur.
Predictive Maintenance
Predictive maintenance can use the data and insights from condition monitoring (and sometimes AI) to predict when a machine could fail.
RotationLF si a PdM tool that helps you to automate that analysis of your machine health data.
Learn more about RotationL for condition monitoring in PdM →
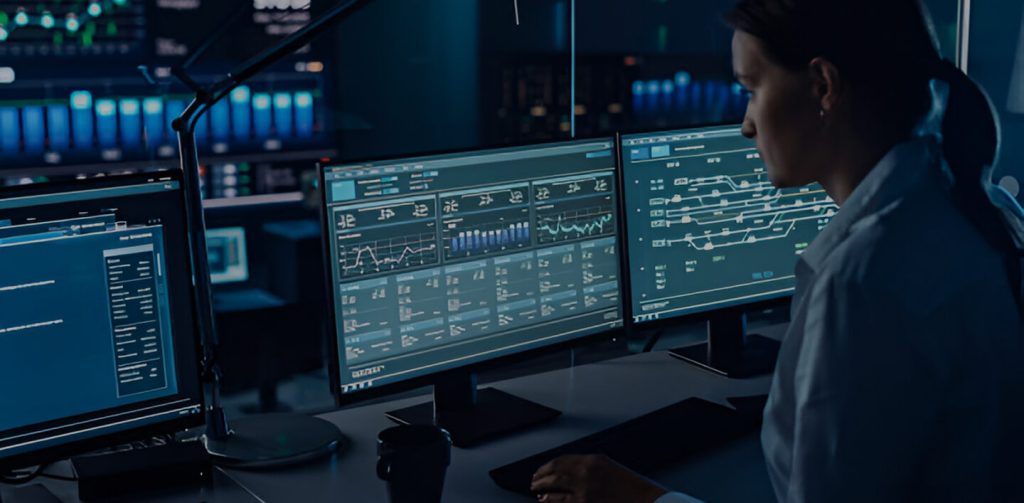
Predictive Maintenance vs Preventive Maintenance
A common misconception is that predictive maintenance and preventative maintenance are the same, as both are proactive maintenance approaches to prevent equipment failure.
However, the two of them differ in their approach and timing of maintenance.
Predictive Maintenance
Maintenance based on the actual condition of the equipment, using real time data and monitoring technologies like a predictive maintenance software.
- Condition based.
- Based on recommendations and signals from predictive maintenance tools like vibration sensors and software.
- Minimizes downtime.
- Custom to individual equipment.
Example: Using vibration analysis to detect wear in a motor bearing and scheduling maintenance when signs of failure are detected.
Preventive Maintenance
Scheduled maintenance performed at regular intervals to keep machines running. It does not take into account condition of the machine.
- Time based (e.x. Every 6 months, or every 1,000 hours of operation).
- Based on historical data and manufacturer recommendations.
- Aims to reduce likelihood of failure (but is not guaranteed)
- Not customized to machinery.
Example: changing oil every 3,000 hours, even if everything looks clean.
Feature | Preventive Maintenance | Predictive Maintenance |
Basis | Time/usage schedule | Real-time equipment condition |
Tools used | Maintenance calendar | Sensors, analytics, AI |
Cost | Lower upfront, higher long-term | Higher upfront, lower long-term |
Downtime | Still possible | Reduced due to accurate predictions |
Efficiency | May result in over-maintenance | Maintenance only when needed |
Case Study: How a $1B Dairy Producer was Able to Prevent Downtime with PdM
How Predictive Maintenance Works
To enable PdM, condition monitoring sensors are installed on machines to continuously track performance and health data. These sensors collect real-time data that is sent to the cloud and analyzed by AI algorithms to detect early signs of faults and predict potential failures through pattern recognition.
With Nanoprecises AI Based Predictive Maintenance Solution, when an anomaly is detected, teams receive a notification about the potential fault, that includes how much time you have until failure and the incurred cost of inaction.
By alerting teams at the earliest signs of failure, the system provides ample time to plan and schedule repairs, reducing downtime, costs and increasing operational efficiency.
Download the Feature Sheet on our PdM Solution.
Advantages of Predictive Maintenance
1. Reduced Unplanned Downtime
- PdM helps detect issues before equipment fails.
- This minimizes unexpected breakdowns and production halts.
2. Lower Maintenance Costs
- Maintenance is performed only when necessary, reducing labor, spare parts, and service costs.
- Avoids the waste of unnecessary routine checks (common in preventive maintenance).
3. Extended Equipment Lifespan
- Early detection of wear or imbalances prevents severe damage.
- Assets last longer because they’re maintained in optimal condition.
4. Improved Safety
- Identifying and fixing faults early reduces the risk of dangerous equipment failures.
- Especially valuable in high-risk industries like oil & gas, manufacturing, and mining.
5. Higher Operational Efficiency & ROI
- PdM improves asset reliability, enabling better planning and production uptime.
- Combined with AI and analytics, it also enables smarter resource allocation and long-term savings.
Predictive Maintenance ROI Calculator:
Reduce downtime, lower costs, and improve efficiency – our calculator takes into account . Try our Predictive Maintenance ROI Calculator now!
The Future of Predictive Maintenance Technology
The future of predictive maintenance is evolving toward energy-centric predictive maintenance and AI-driven strategies. Energy-centric PdM uses real-time energy consumption data to detect inefficiencies and early signs of equipment failure, enabling both maintenance and energy optimization. This approach not only improves asset reliability but also supports sustainability goals by reducing unnecessary power usage.
Meanwhile, AI-based predictive maintenance leverages machine learning to analyze vast datasets, identify hidden patterns, and predict failures with high accuracy. As sensors and industrial IoT become more widespread, combining energy insights with AI models will enable truly intelligent, self-learning systems that maximize uptime, reduce costs, and enhance operational efficiency.