Preventive Maintenance Services
Preventive Maintenance
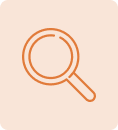
Preventive maintenance is the process of monitoring the machines & equipment sets to make sure everything is working in the optimum condition. This includes checking your machines for strange noises, lubricating the right areas, and changing all your filters among other actions
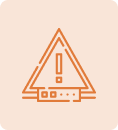
Failure to do these things, results in the risk of a total shutdown of the manufacturing facility, thereby causing delayed production outputs and a broken relationship with your customers & partners.
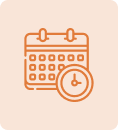
A good maintenance schedule is one of the most important weapons in your arsenal. It involves more than just monitoring and fine tuning. It also involves creating exhaustive and detailed documentation on your machines’ health to make sure all heavy-duty assets are running at optimum performance levels.
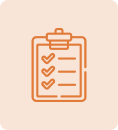
Good records help operators predict future problems and estimate how long things can run before they need to shut down. This is a surprisingly big challenge since each piece of machinery has different needs and has different ways in which they can fail. There are an infinite number of ways to fail and only a handful of ways to succeed after all.
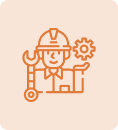
It takes a competent and experienced technician to spot the lesser-known signs of an incoming catastrophe, and not every facility is gifted with that. Examining your production operations and machines is complex, and takes a lot of time.
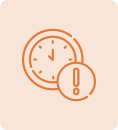
It can be difficult to make the call to schedule a maintenance spot. It slows down production in the short-term, and that makes operators anxious about meeting goals. But in the long-term, this is absolutely critical to ensure that the business faces minimal downtime, maximum outputs, and maintains the smoothest operations possible.
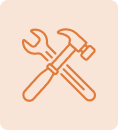
At Nanoprecise, we understand the pressures you face. We make use of unique, IIoT hardware and patented algorithms to determine the health & performance of your machines. We use artificial intelligence to implement automated predictive maintenance solutions that create a baseline performance metric for each equipment, predict impending faults and offer recommendations for remedial action, that suits the specific needs of each particular equipment.
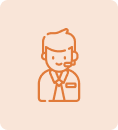
We understand that maintenance is a challenge. This is why we provide you with the expertise you need to succeed, through our CAT Level 2/3/4 analysts & Reliability experts who offer assistance to identify the issues in machines and plan corrective steps right away.
The Benefits of Preventative Maintenance
The best of Preventative Maintenance strategies helps engineers create a framework which ensure that the most critical components don’t fail unexpectedly. Equipment and components are well inspected and replaced before failure, making sure the most critical assets don’t turn into liabilities when you least expect it.
Machines can stop with little or no warning. They don’t necessarily complain out loud and would rather just silently suffer until the maintenance team take notice. This will eventually lead to technicians rushing from problem to problem, putting fires out. Preventative Maintenance helps to avoid this catastrophe by offering various benefits.
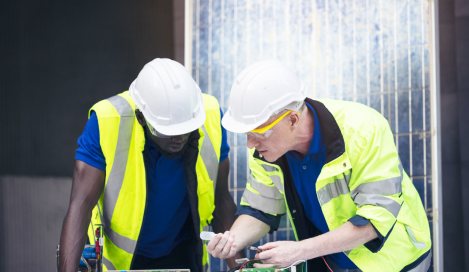
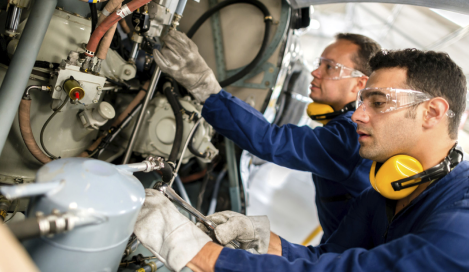
Benefits of a Preventative Maintenance Regime:
- Reduced unplanned downtime
- Improved operational efficiency
- Increased asset uptime
- Optimized resource utilization
- Saves time & money
A preventative maintenance plan also improves equipment effectiveness while reducing the mean time between failures so that production always meets its deadlines and overtimes are minimized.
Many facilities often have predictive maintenance solutions in place, to monitor the health & performance of machines in real-time. This helps the maintenance & reliability professionals to gain a complete picture of the overall manufacturing operations. It not only predicts failures & improves efficiency but also increases the overall safety of the workers by providing a complete visibility of the manufacturing unit.
When engineers & technicians can focus on doing their jobs instead of putting out fires and treating malfunctions, they end up with better morale in the workplace. This is a crucial component for having a successful workplace that can innovate and produce results.
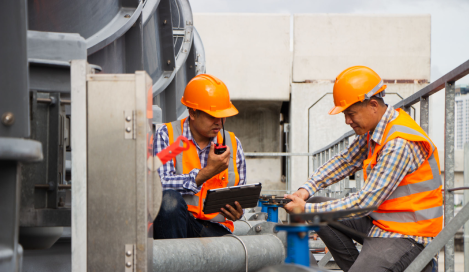
Predictive Maintenance Solutions
Predictive maintenance solutions can help implement the right framework by providing customised solutions that fit he needs of each piece of equipment. Technicians & Engineers then have an easier time executing their duties by automating many of the steps in preventative maintenance. This helps to create the best working conditions and maximizes the lifespan of your equipment too. Automated condition monitoring of the industrial assets with the right predictive maintenance solution keeps them running effectively and safely. The right software can help businesses prevent unexpected failures and the resulting unplanned downtime, organize tasks and maintain appropriate records at the same time.
Don’t hesitate when it comes to contacting a vendor. Following the manufacturer’s guidelines to maintain your equipment isn’t enough in the long run. Operators need advanced systems that can help them be proactive by diagnosing faults in advance, so that they aren’t forced into desperate measures once failure is imminent.
Request a Call Back
Frequently Asked Questions
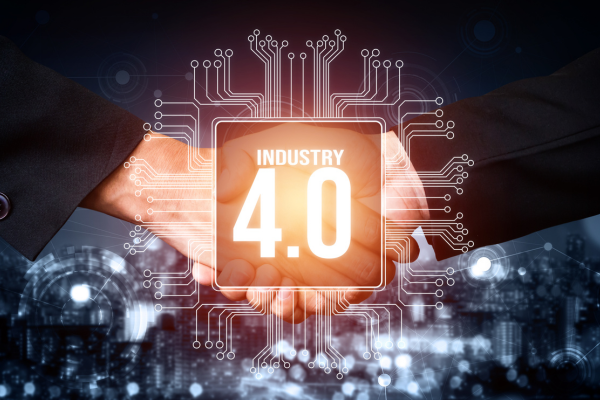
Let us show you how!
Explore the transformative potential of predictive maintenance. At Nanoprecise, we specialize in tailoring predictive maintenance to your unique needs. Reach out today, and together, let’s pave the way for a more efficient, profitable and sustainable future.