Metal Manufacturing Industry
Unplanned downtime and rising carbon emissions are major challenges in modern metal manufacturing. Nanoprecise delivers IoT-drive and AI-powered predictive maintenance solutions (PdM) tailored for the harsh, high-impact environments of metal production.
Trusted by industry leaders like Tata Steel, our platform helps reduce unplanned outages, optimize asset performance, and support your path to net-zero goals.
Explore our case studies and brochure to see how we’re transforming metal manufacturing!
Trusted by STeel and Metal manufacturing Leaders
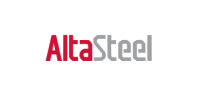
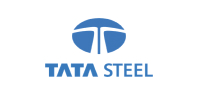
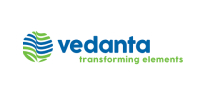
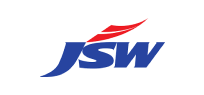
Metal Manufacturing Industry Challenges
Harsh Operating Conditions
Metal manufacturing, characterized by elevated temperatures, dust, and abrasive materials, poses harsh operating conditions that contribute to accelerated wear and tear on equipment. This challenging environment makes monitoring equipment a complex task.
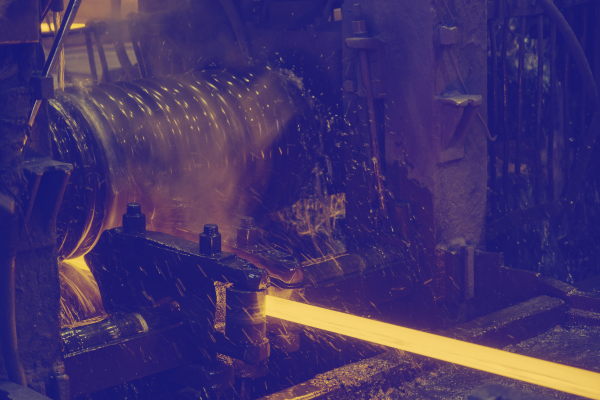
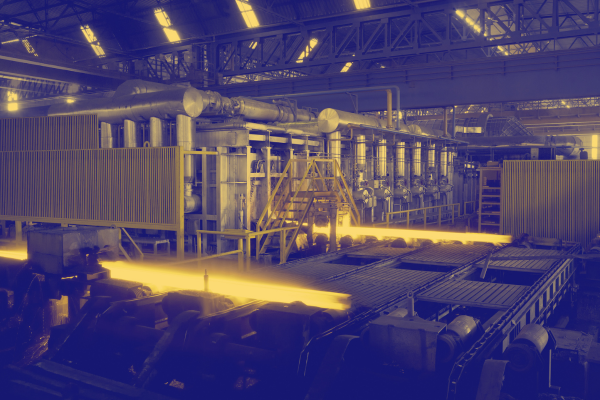
Monitoring Variable Speed Assets
Metal manufacturing encompasses a diverse range of machinery with varying RPMs. Because of this, Condition Monitoring solutions must be versatile enough to cover assets with both high and low RPM, ensuring that the entire spectrum of equipment is adequately monitored and maintained.
High Carbon Emissions in Metal Manufacturing
The metal industry faces the unique challenge of having the highest carbon emissions per dollar of value produced. Addressing this issue requires strategic measures, and energy-centric predictive maintenance emerges as a key player in minimizing downtime-related emissions and promoting sustainable practices.
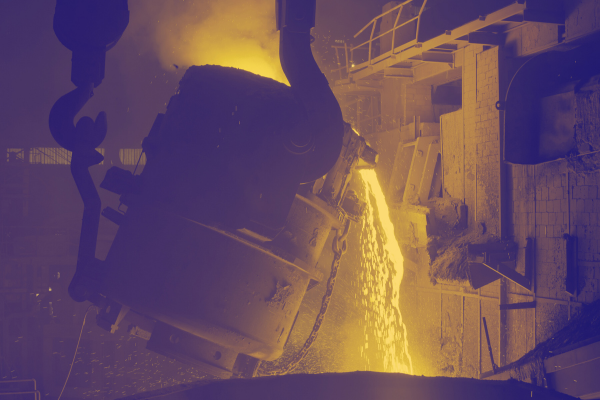
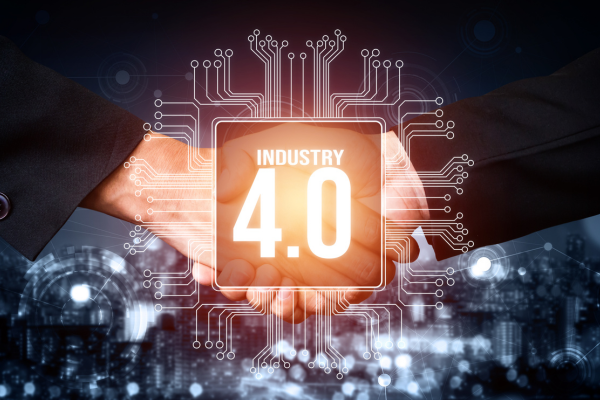
Let us show you how!
Explore the transformative potential of predictive maintenance. At Nanoprecise, we specialize in tailoring predictive maintenance to your unique needs. Reach out today, and together, let’s pave the way for a more efficient, profitable and sustainable future.