Chemicals
Within the intricate realm of the chemical industry, operational challenges persist, necessitating a strategic approach to ensure efficiency and reliability. Predictive maintenance emerges as a transformative solution, addressing key issues manufacturers face. Complex processes and the potential for equipment failures often lead to unplanned downtime, disrupting production cycles. Predictive maintenance, however, offers a proactive strategy, by leveraging advanced analytics and real-time data, allowing chemical manufacturers to foresee potential equipment issues, minimizing unplanned downtime, and enhancing overall operational efficiency. This predictive approach optimizes equipment reliability and contributes to meeting safety standards and environmental regulations. Join us in exploring the strategic advantages of predictive maintenance, as we delve into how it elevates efficiency, safety, and sustainability in the complex landscape of the chemical industry.
Industry Challenges
Inherently Dangerous Applications
Chemical manufacturing involves applications with inherent dangers, posing risks to both equipment and personnel.
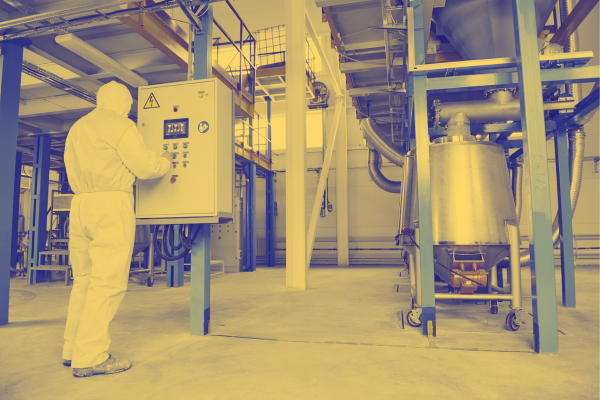
High Temperature & Pressure Conditions
High-temperature and high-pressure environments in chemical manufacturing can challenge the operational capabilities of traditional condition monitoring techniques.
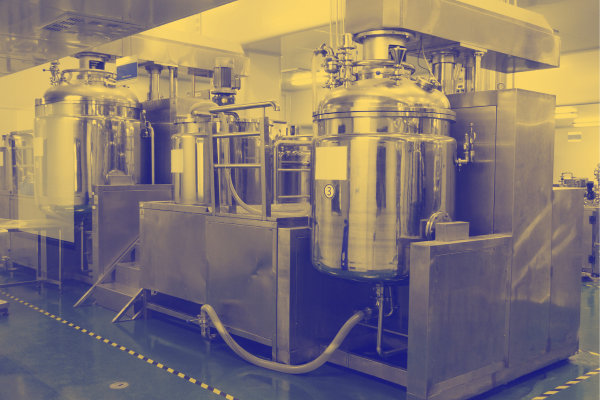
Large Range of Equipment Sets with Highly Varying Speed
Diverse equipment sets with significantly varying speeds demand nuanced monitoring solutions.
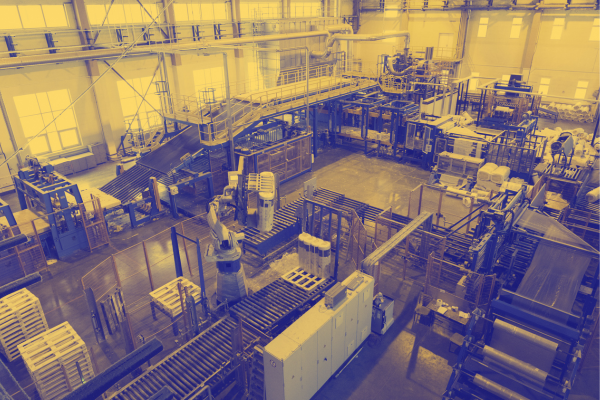
Applications
Colling Tower Fans
Compressors
High-Pressure Pumps
Agitators
Centrifuge
Compactors
Trusted By Your Peers
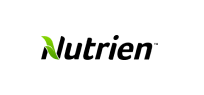
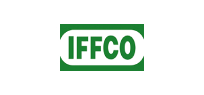
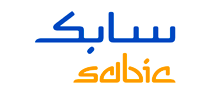
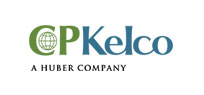
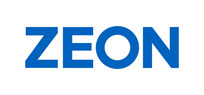
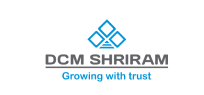
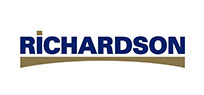
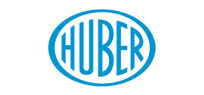
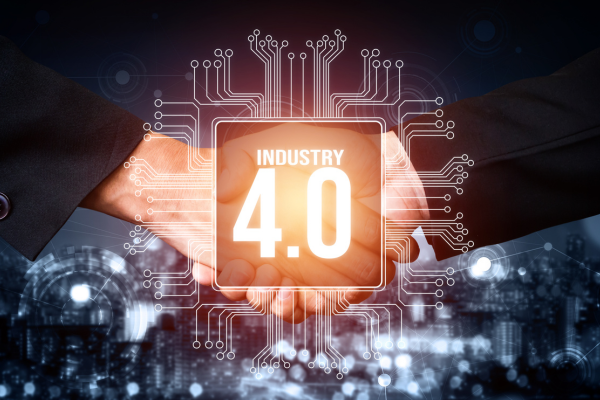
Let us show you how!
Discover the path to operational excellence in the chemical sector with Nanoprecise Sci Corp. Uncover the transformative power of predictive maintenance solutions tailored to the distinct challenges of chemical manufacturing. Our specialized offerings seamlessly align with the complexities of your operations, providing a host of benefits, from ensuring equipment reliability to optimizing processes and achieving comprehensive operational efficiencies. Connect with us today to experience a personalized demonstration, allowing us to showcase how our solutions are poised to redefine excellence in your chemical endeavors.