Vibration Analysis in
Gearboxes
What is a Vibration Analysis in Gearboxes?
A gearbox is a mechanical device that helps control the speed and power of a motor before transferring it to a machine. It can also change the direction of movement and adjust how the power is delivered. Different gears inside the gearbox work together to perform these tasks.
Gearboxes with in large industrial assets are durable and compact but require regular care, like proper lubrication and alignment, to function effectively and last longer.
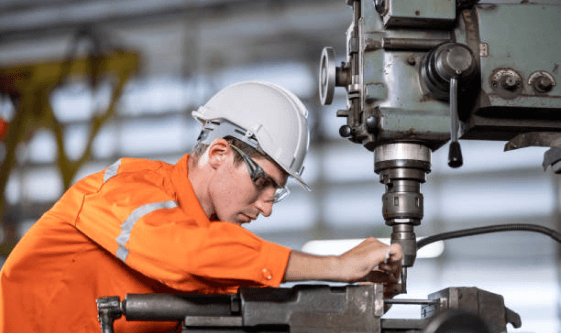
Ensure Smooth Gearbox Performance with Vibration Analysis in Gearboxes
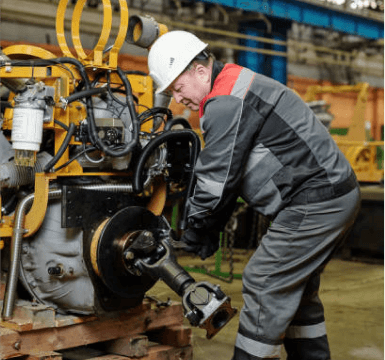
Most machinery runs without a hitch at first. However, wear and tear can take a toll on the asset over time.
Conducing vibration analysis on gearboxes helps identify these early signs of wear, preventing unexpected failures, expensive downtime, and keeping equipment running smoothly.
Nanoprecise Sci Corp’s Vibration Analysis in Gearboxes solution provides a reliable way to monitor equipment. The 6-in-1 sensors and smart AI-based systems provide real-time insights, helping rotating assets stay efficient and reliable, even in extreme conditions.
What does Vibration Analysis in Gearboxes do?
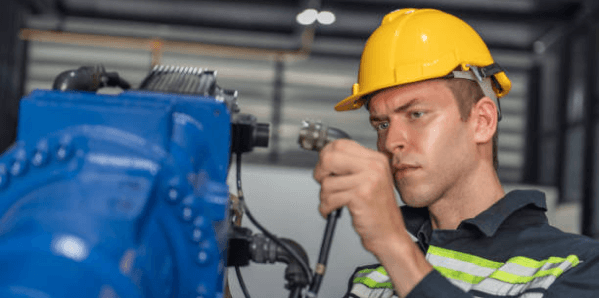
Gearboxes ensure efficient power transmission within complex systems. Any gearbox failure, imbalance, or flaw can result in significant downtime, operational disruptions, and costly repairs. Vibration monitoring uses sensors to watch changes in different machines and equipment. When vibration levels increase, it often signals potential issues, such as emerging malfunctions, process limitations, or impending failures
Potential issues detected using Vibration Analysis in Gearboxes
- Imbalances and misalignments
- Excessive wear and tear
- Overloading conditions
- Impending bearing failures
- Installation issues
- Manufacturing Defects
Even a minor crack in a gear can disrupt speed when the damaged teeth enter the load zone, causing impacts and operational inefficiencies. Additionally, insufficient lubrication of gear teeth can lead to increased friction, further exacerbating wear. Vibration analysis detects friction—and impact-related anomalies through predictive maintenance solutions.
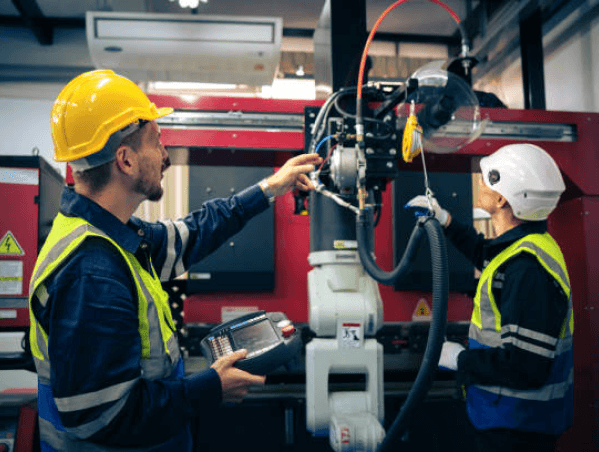
How Nanoprecise Sci Corp Helps Protect Gearboxes with Advanced Vibration Analysis in Gearboxes
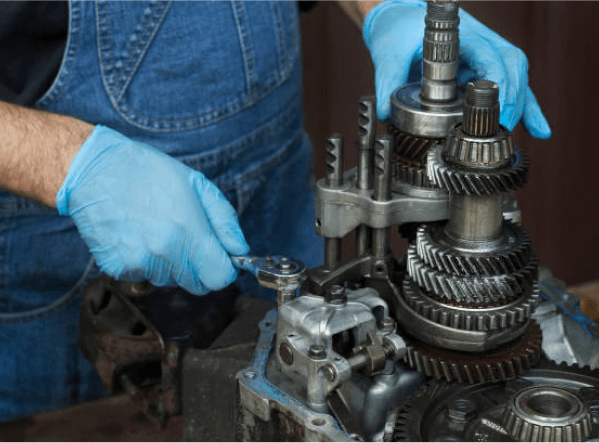
Nanoprecise combines cutting-edge Machine-Doctor™ wireless sensors and the RotationLF™ AI-based platform to deliver an end-to-end predictive maintenance solution.
Machine-Doctor™ Wireless Sensors:
6 in 1 wireless sensor measure six key parameters – Acoustic, Acceleration, Magnetic Flux, RPM, Temperature, and Vibration. These sensors collect and transmit data to our secure analytics platform, ensuring continuous monitoring.
AI-Powered RotationLF™ Platform:
Once data is received, RotationLF™ uses advanced algorithms to analyse vibration patterns and detect real-time abnormalities. This platform provides automated insights, allowing teams to respond quickly and prevent critical failures.
Real-Life Case Study of Vibration Analysis in Gearboxes from Nanoprecise
A renowned commercial fishing vessel, operating under some of the harshest maritime conditions depends on its gearboxes and engines to perform safely and efficiently, whether battling deadly seas or navigating calmer waters during off-season.
Challenge:
Major gearbox maintenance is nearly impossible at sea, with repairs typically reserved for dockside operations in remote locations. With limited access to trained personnel and materials, predictive maintenance is vital to avoid catastrophic failures.
Solution:
Nanoprecise’s Machine-Doctor™ sensors and RotationLF™ analytics were installed on the vessel’s gearbox and critical components. When data analysis indicated a rising vibration in the gearbox’s Z-axis, the system automatically alerted the crew to take corrective action. By reducing RPM and inspecting the coupling upon return to the dock, the vessel prevented further damage and avoided a potential breakdown.
Outcome:
Nanoprecise’s Vibration Analysis in Gearboxes solution allowed the crew to respond proactively through timely diagnostics, enhancing the vessel’s reliability and avoiding costly, dangerous failures at sea.
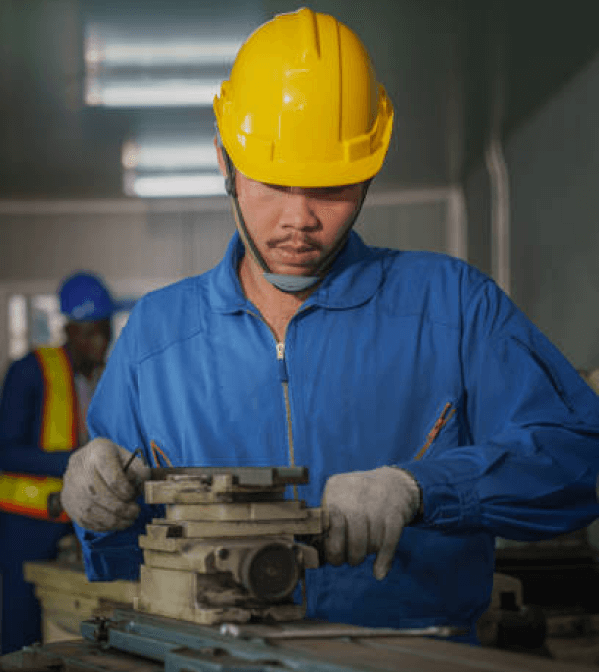
Request a Call Back
Frequently Asked Questions
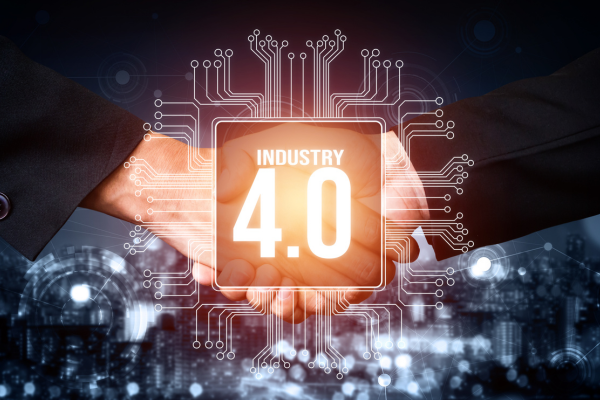
Let us show you how!
Explore the transformative potential of predictive maintenance. At Nanoprecise, we specialize in tailoring predictive maintenance to your unique needs. Reach out today, and together, let’s pave the way for a more efficient, profitable and sustainable future.