Wireless Vibration Sensors
Learn more about Nanoprecise’s wireless vibration sensors for optimal condition monitoring!
Wireless Vibration Sensors & Condition Monitoring
More and more industries are adopting IoT technology such as wireless sensors and other connected devices to monitor the condition of the machines and optimize operations.
IoT is playing an increasingly important role with devices such as wireless vibration sensors being used to revolutionize the traditional practices. Companies are using these sensors to monitor production processes, detect potential issues, and streamline operations.
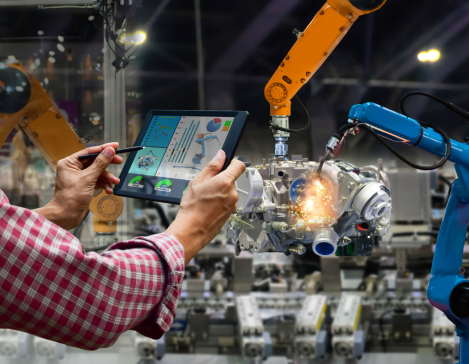
Features of Wireless Vibration Sensors:

The first and most important thing to know about wireless vibration sensors is the fact that they do not require any wires for installation and transmission. They can be easily mounted on surfaces and can start capturing data within minutes of installation.

Wireless vibration sensors are very reliable in all environments. This means that no matter what time of day or night, you will always have access to the same level of accurate data. You can use your wireless vibration sensor on floors, walls, ceiling or even machinery inside your factory as well as outside it.

They are the one of the best solutions for monitoring the health & performance of machines and equipment sets placed at remote and hard-to-reach places.

These devices are able to operate in any climate as are designed to meet the IP66/IP67 specification for protection from liquid and dust.

Wireless vibration sensors allow to automate your different vibration measuring processes and can send out alerts to maintenance & reliability teams instantly whenever there is a variation in the vibration parameter. This allows for a better process of identifying problems and providing companies with peace of mind.

The last thing that one should know about wireless vibration sensors is the fact that they are extremely easy to use. In fact, there are very few knowledge requirements involved when it comes to employing these devices since they require pretty much no set-up process at all.

Getting better service is also an important feature that companies consider when they are trying to find the right equipment for their needs. Wireless vibration sensor providers are not only able to provide improved services, but their services can also be customized to fit your business requirements.
Wireless Vibration Sensor System
The wireless vibration sensor system is made up of a number of different units that are connected to each other as well as to the machinery.
These sensors have the ability to pick up on the vibration up to a higher level than those found in the incumbent systems, gateways and an analytics platform.
They then send texts or emails notifications, letting the maintenance staff know when something is not right. A wide array of monitoring software comes with the system, allowing all users to easily access information related to their overall operational efficiency.
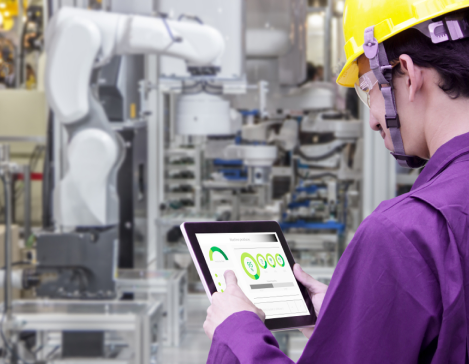
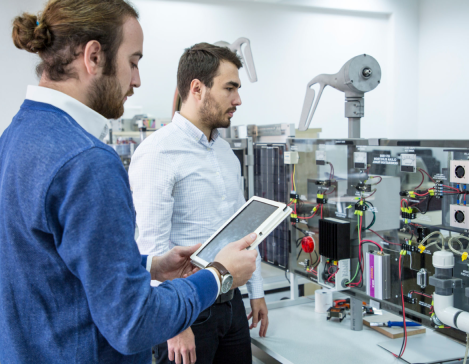
It is important that you make use of the wireless vibration sensor to its full potential so that you can avoid any mishaps in the manufacturing plant.
Maintenance & reliability professionals use wireless vibration sensors to keep a constant check on their equipment sets. They can also install additional sensors in order to ensure they are more effective in their monitoring efforts.
This helps engineers & technicians keep up with what’s going on, even when some personnel are unavailable. It will also help maintain the efficiency of your entire machine and make it easier to achieve more targets for your company’s bottom line.
Significance of Wireless Vibration Sensors
Since the wireless vibration sensor can be set up anywhere, anytime, it transforms the entire condition monitoring process of your machines. This makes it easier for maintenance personnel to gain a better understanding of their machine’s performance as a whole and what they need to do in order to keep them in top notch condition. Maintenance teams no longer need to constantly check on their machines manually, or spend hours putting together reports for the field staff to take action. Using the wireless vibration sensor system helps to make sure that reliability technicians and managers never miss any important issue.
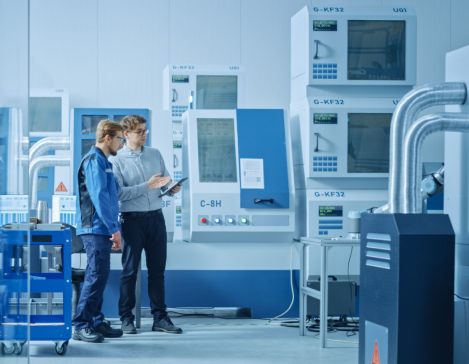
Conclusion
With wireless vibration sensors, you can get a better understanding of your machines and what they’re doing at all times. This will help you effectively maintain the equipment sets and guarantee that they are working on their maximum capacity.
The wireless vibration sensor is just the right product for anyone who wants to keep a closer eye on their equipment sets. From its advanced features to its simple installation process, this device is truly one of the best investments you can ever make for your company.
Nanoprecise Sci Corp offers a wide range of wireless sensors that not only monitor vibration but also monitors the acoustic emissions, RPM, Magnetic Flux, Temperature & Humidity, all of which can be used to monitor the performance of industrial assets in a variety of different sectors. These units are able to deliver accurate and reliable data, thanks to their durability and advanced features that make it easier for them to function. If you want to keep your plants running on maximum efficiency, then these sensors are just the right choice for you.
Request a Call Back
Frequently Asked Questions
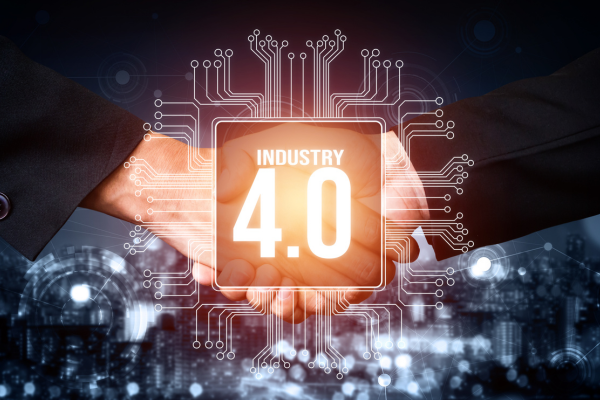
Let us show you how!
Explore the transformative potential of predictive maintenance. At Nanoprecise, we specialize in tailoring predictive maintenance to your unique needs. Reach out today, and together, let’s pave the way for a more efficient, profitable and sustainable future.