Vibration Monitoring Services
As the important components of rotating machinery start to wear, tolerances become harder to maintain and the surface finish deteriorates, thereby affecting the performance negatively. Breakdowns may occur when maintenance is deferred long enough. Vibration monitoring services allow you to steer clear of such a situation.
What is meant by vibration monitoring?
Vibration monitoring is the process of using sensors to monitor changes in various types of machines and equipment sets.
Increased levels of vibration can be an indication of a developing malfunction, process restriction, or even a failure. Proper vibration monitoring of rotating equipment is vital to a competent and successful maintenance program.
It can lead to a reduction in unplanned downtime, as well as repair and maintenance costs while optimizing machine performance.

Predicting repair with vibration monitoring and analysis
Almost all factories have rotating machinery and equipment, like motors, pumps, and gearboxes. All of these equipment sets tend to run smoothly at first, but then usage, as well as slight imperfections in installation or manufacturing, takes a toll.
Their shafts bend and go out of alignment, couplings start to fail and bearings begin to wear. As these failures develop, the vibration of the equipment starts to increase. At first, it’s a gradual progression, accelerating as the equipment reaches the point of failure.
The vibration of any object in motion tends to be characterized by variations in frequency, intensity, and amplitude. Such vibration signatures can be correlated to a physical phenomenon, which makes it possible to make use of the vibration data in order to gain insights into the overall efficiency and health of the equipment.
Vibration monitoring services typically are a part of the overall maintenance program. It aids manufacturers in avoiding breakdowns and quality issues. These services aid in identifying characteristic vibration signatures and subsequently predict when key components need replacing.
By partnering with a company like Nanoprecise Sci Corp that specializes in Gearbox Vibration Monitoring, you can get adequate time to source the new parts for your equipment, plan their installation, and maintain your production schedules properly, without having to deal with the hassles of quality problems or overdue orders.
Talk to our experts
Getting the most from vibration monitoring
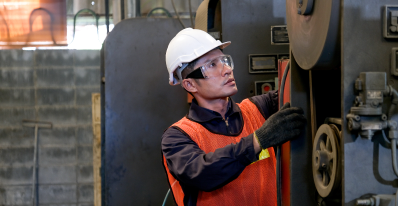
Detecting common problems using vibration
Vibration may prematurely wear components, result in safety issues, shorten the life of the equipment, and create noise. Misalignment and imbalance in rotating assets may break driveshafts and other components.
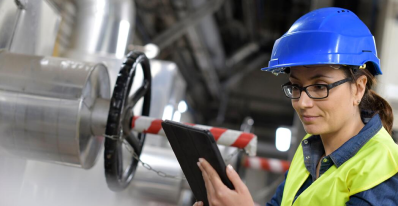
Visually illustrating the severity of vibration
Vibration monitors make use of a color-coded hierarchy to inform maintenance teams of the vibration intensity. As the performance indicators of assets deviate from pre-set baselines, the predictive maintenance software sends an alarm indicating that the thresholds have been exceeded.
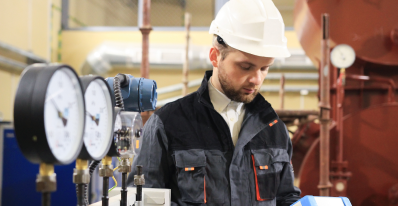
Tracking asset health with temperature and vibration
Capturing changes in surface temperature may not precisely identify the internal problem, but condition changes in regards to ambient temperature are known to be a good indicator of the impending fault and can be used to notify engineers/technicians for further evaluation.
Providing specialized Vibration Monitoring services
- Establishing a robust vibration monitoring system includes much more than just buying a vibration analyzer.
- It requires an in-depth knowledge of vibration testing software and devices, along with an understanding of rotating equipment design.
- Knowing how to properly use data in machine vibration analysis is also needed. The complexity of the processes such as Vibration Analysis in Gearboxes can be daunting to many.
- This is where we come in. Nanoprecise Sci Corp has the knowledge and experience to deliver advanced automated vibration monitoring services specific to the needs of your business.
- With this approach, even novice users can get value out of the sophisticated system while still allowing for those that are highly skilled to interrogate the data in great depth.
Request a Call Back
Frequently Asked Questions
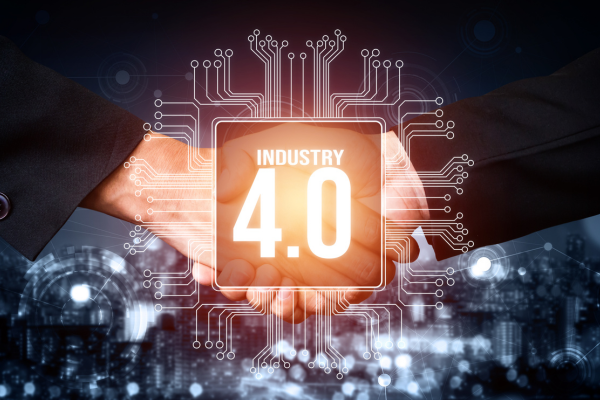
Let us show you how!
Explore the transformative potential of predictive maintenance. At Nanoprecise, we specialize in tailoring predictive maintenance to your unique needs. Reach out today, and together, let’s pave the way for a more efficient, profitable and sustainable future.