Bearing Failure Analysis
What is Bearing Failure Analysis?
Bearing Failure Analysis is the process of collecting and analyzing critical data about bearings to determine the cause of bearing failure. When bearings fail to meet their expected performance levels or expected life, the consequences can be disastrous such as increased downtime, revenue loss, high maintenance costs, lost production and missed deliveries. To help mitigate failures and offer remedial action, reliability experts analyze, test and examine a wide range of bearing performance parameters. They use various tools to understand what may have caused the failure and take preventive action. The experts follow strict procedures in inspecting and securing failed components to reach reliable conclusions.

Techniques for bearing failure prevention
Machines break down due to improper bearing motion, but there are ways to prevent unnecessary wear on them and increase their overall service life. Some of the techniques are mentioned below

Choosing right bearing design
The right bearing design is the one that enables it to handle the load being applied on it. Typically, the design that is specified in the documentation provided by the original equipment manufacturer determines the proper bearing operation. It is also vital to choose the appropriate bearing size to avoid premature wear & tear.

Storing bearings actively
Sometimes, machines and bearings are maintained in facility stores in order to avoid transportation delays from potentially unexpected failures. In these situations, the bearings sitting on shelves experience vibration due to the facility around them. It is essential to ensure that e storage area should be vibration free, so as to maximize the number of rolling elements with the raceways. Moreover, these bearings must be stored actively or rotated occasionally. Without occasional rotation, the bearings can experience false brinelling when being stored for longer durations.

Installing the bearings appropriately
Along with force, heat also plays a crucial role in bearing installation. For many bearings, heating the inner race causes it to expand and fit better during installation. After finishing the installation as per the manufacturer’s instructions, you must clean the bearing with a lubricant.

Lubricating the bearings
Lubrication forms a thin oil film over the surface of the bearing, which helps to reduce the friction, prevents corrosion and extends the life of both the bearings and machinery. Without sufficient lubrication, the metal-on-metal operation will wear down the bearings and subsequently the machine, thereby increasing the cost of maintenance and spare parts. At the same time, if over lubricated, the metallic surface will emit more heat that cannot be dissipated making it difficult for the bearing to move correctly.

Aligning the machine accurately
Precise machine alignment is essential to ensure that the machines work in the optimal condition, with minimal requirement of maintenance. Any component misalignment can lead to catastrophic failure, thereby increasing the cost of repair & maintenance. It also threatens the safety of the workers & engineers on the shop floor.
In the absence of precise alignment, the machine bearings may face abnormal wear. Some of the bearings may even wear out prematurely. A misaligned machine may also consume high amounts of energy and experience a decrease in efficiency. Therefore, it is essential to ensure that the machine is aligned accurately to avoid any failures.
Types and causes of Bearing failure
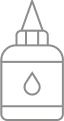
The primary causes of bearing failure are:
Inadequate lubrication
Contamination
Cage damage
False Brinelling
Raceway wearTitle
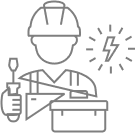
The main types of bearing failure are:
Misalignment of one side of the bearing.
Electrical arc erosion of the bearing parts
Brinelling or damage to the bearing raceway
Fatigue failure caused to the weakening of the bearing steel grain
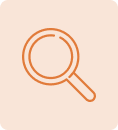
Bearing failure analysis services
Nanoprecise conducts bearing failure analysis following the required procedures and standards for investigation of failed components. Our bearing failure analysis steps include:
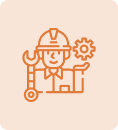
Collection of Data
Our wireless industrial IoT sensors work towards obtaining information related to the health & performance of bearings among other components of the machine. They monitor the operating conditions data such as acoustic emissions, temperature, load speed and magnetic flux, of the surface. Our predictive maintenance tools collect data and automatically creates a range-bound baseline for measuring the equipment performance.
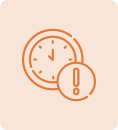
Analysis of the Data
The data captured by our wireless industrial IoT sensor is transmitted to our analytics platform via Wi-Fi or cellular networks. The platform analyses the complex bearing health data using AI & Physics based models to predict any developing faults and offers suggestions for maintenance actions. The real-time dashboard offers information about the health & performance of each component of the machine. This analytics dashboard will also confirm the Remaining Useful of the component, i.e., the time until the component fails completely. Our experienced technical team offers assistance to identify the issues and plan corrective actions right away.
Request a Call Back
Frequently Asked Questions
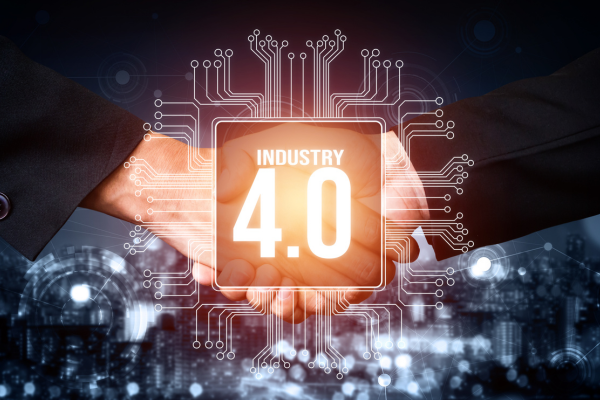
Let us show you how!
Explore the transformative potential of predictive maintenance. At Nanoprecise, we specialize in tailoring predictive maintenance to your unique needs. Reach out today, and together, let’s pave the way for a more efficient, profitable and sustainable future.