Predictive Maintenance in Malaysia
Introduction
Predictive maintenance is gaining momentum in Malaysia as industries embrace Internet-of-Things and AI technologies to reduce downtime, optimize equipment performance, and improve the productivity of their manufacturing operations. The adoption of predictive maintenance in Malaysia is on the rise, as industries recognize its potential to enhance equipment reliability, minimize maintenance costs, and improve overall operational efficiency.
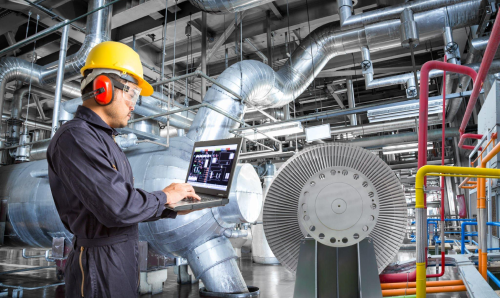
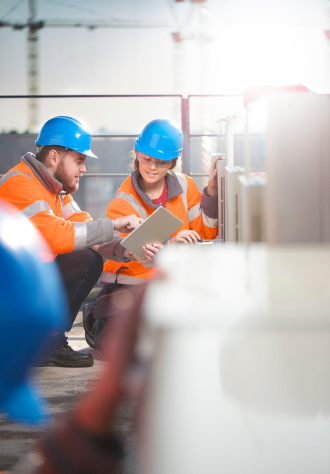
Predictive Maintenance
Traditional maintenance approaches often follow a reactive or preventive schedule, which may lead to unnecessary maintenance or overlooking critical issues. Predictive maintenance takes a proactive approach by leveraging data analytics, and condition monitoring techniques. This most needed and avoiding unnecessary maintenance tasks.
Predictive maintenance is becoming an increasingly important aspect of modern industrial maintenance. There are many companies that offer predictive maintenance solutions in enables businesses to optimize maintenance strategies, focusing resources where they are Malaysia to help businesses optimize their maintenance schedules, reduce equipment downtime, and lower maintenance costs. These solutions typically involve the use of sensors and advanced analytics to detect potential problems before they occur.
Current Landscape of Predictive Maintenance in Malaysia
The predictive maintenance market in Malaysia is still in its early stages, but it is expected to grow rapidly in the coming years. With the increasing adoption of Industry 4.0 technologies, predictive maintenance solutions are becoming more important than ever before. Companies in Malaysia are looking for ways to optimize their operations, reduce downtime, and cut maintenance costs, and predictive maintenance is seen as a key tool to achieve these goals. Industries that are likely to see the greatest adoption of predictive maintenance in Malaysia include manufacturing, oil and gas, and transportation. As the market continues to mature, manufacturers can expect to see more providers offering predictive maintenance solutions tailored to the specific needs of these industries.
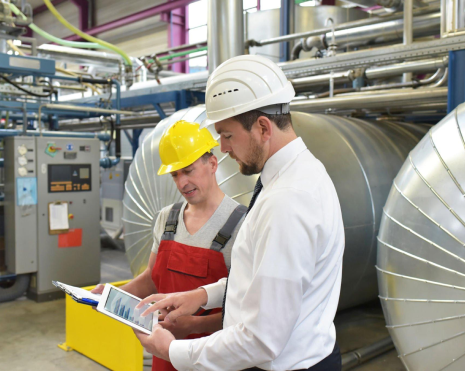
Future of Predictive Maintenance in Malaysia
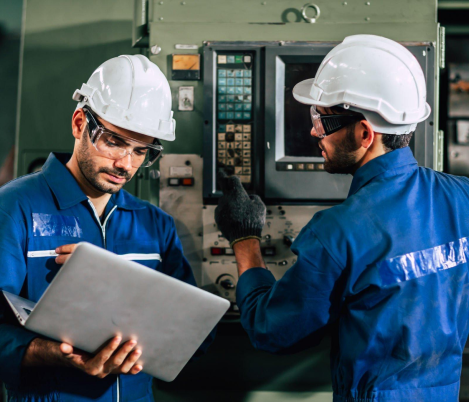
The future of predictive maintenance in Malaysia looks bright, with emerging trends and opportunities presenting themselves. One of the most exciting areas of development is the use of artificial intelligence (AI) to predict equipment failure. As AI and machine learning technologies continue to evolve, we can expect to see predictive maintenance solutions becoming even more accurate and effective. Other emerging trends include integration with existing enterprise systems, to allow seamless data exchange and to incorporate multiple operational processes such as asset management, maintenance planning, and supply chain management.
The future of predictive maintenance will also see the development of industry-specific solutions tailored to address the specific challenges and needs of sectors such as manufacturing, energy, transportation, and Infrastructure & Facilities. These specialized solutions will consider industry-specific variables, regulations, and performance indicators, allowing businesses to optimize maintenance strategies and maximize operational efficiency within their respective industries. Additionally, predictive maintenance will also contribute to sustainability efforts by enabling businesses to adopt a proactive approach, by determining the energy consumption patterns of industrial assets, thereby enabling operators to reduce resource wastage, and minimize the environmental impact of equipment failures.
As the predictive maintenance market in Malaysia continues to grow, we can expect to see more opportunities for businesses to optimize their operations, reduce costs, improve safety, and increase sustainability.
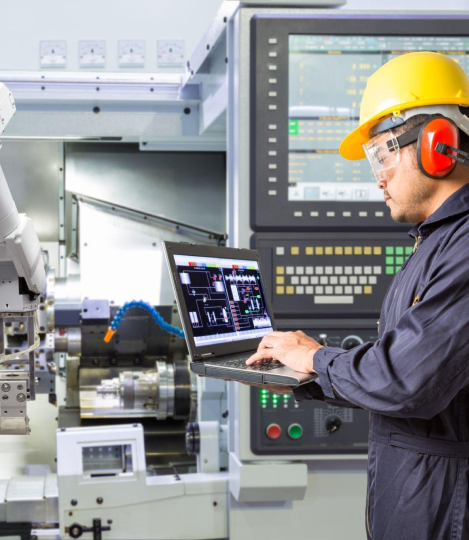
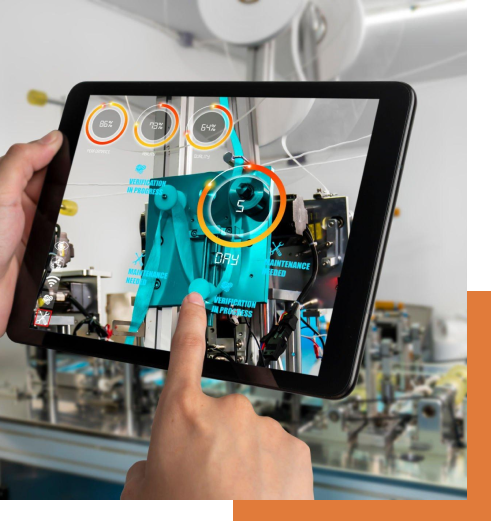
Why Choose Nanoprecise Sci Corp
Nanoprecise specializes in the implementation of Artificial Intelligence and IIoT technology for predictive asset maintenance and reducing the carbon footprint of manufacturing plants. With our innovative solutions and comprehensive expertise, we empower businesses across Malaysia to achieve operational excellence and elevate their performance to new heights. We bring cutting-edge manufacturing technologies to Malaysian businesses, enabling you to embrace digitalization of your operations.
Our comprehensive solutions, industry expertise, and commitment to innovation can help your business optimize operations, enhance productivity, improve product quality, and gain a competitive advantage in the market. Contact us today to embark on the journey of driving manufacturing excellence in Malaysia.
Request a Call Back
Frequently Asked Questions
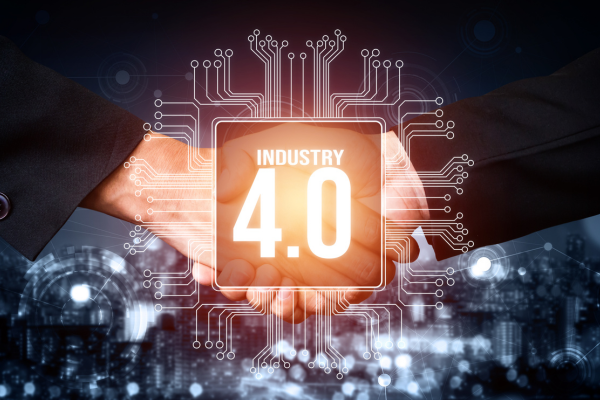
Let us show you how!
Explore the transformative potential of predictive maintenance. At Nanoprecise, we specialize in tailoring predictive maintenance to your unique needs. Reach out today, and together, let’s pave the way for a more efficient, profitable and sustainable future.