Machine Condition Monitoring Services
Nanoprecise Sci Corp offers Machine Condition Monitoring services to empower maintenance and reliability professionals with the right data at the right time, thereby reducing unplanned downtime, improving the productivity and the overall efficiency of the manufacturing operations
What is Machine Condition Monitoring?
Machine condition monitoring is comprised of techniques that are adopted to assess the health of a machine over a time period.
Condition monitoring aims to monitor parameters such as equipment efficiency, wear & tear, and key performance indicators like usage & maintenance statistics as well as the overall output of the machine.
Machine condition monitoring is carried out through physical means such as vibration monitoring, load monitoring, temperature monitoring and so on.
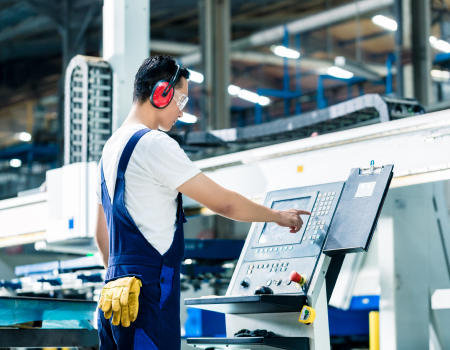
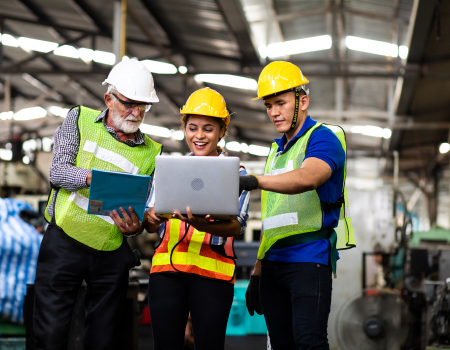
Machine condition monitoring can contribute to an increase in the overall production efficiency as it can help the maintenance & reliability team make important decisions such as whether to continue production, for how long and the trade-offs thereof.
Regular condition monitoring can enable machines to work to their optimum capacity by reducing downtime and the cost of parts significantly.
What is Machine Condition Monitoring?
Machine condition monitoring can increase the longevity of the equipment. It can also monitor & identify specific parameters that indicate machine or component damage right away. Underlying issues can be addressed and rectified before any downtime or long-term damage to the machine occurs.
Simply put, machine monitoring can help manufacturers extract the maximum output from an existing machine without spending time or budget on non-essential maintenance. Data analytics and deep insights on machine performance can be utilized for more effective decision making.
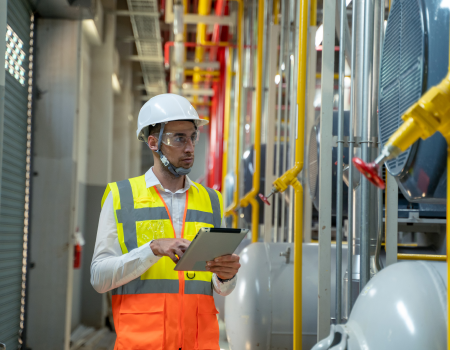
The primary benefits of machine condition monitoring

Eliminating or reducing unscheduled downtime

Enhancing equipment quality

Enabling automation based on data of real-time machine condition

Improving overall production efficiency

Obtaining complete visibility of the overall manufacturing process
Types of Machine Condition Monitoring

This involves inspecting equipment for general wear & tear and documenting equipment failures & other information. Maintenance personnel will be physically present on-site to gather the relevant information.
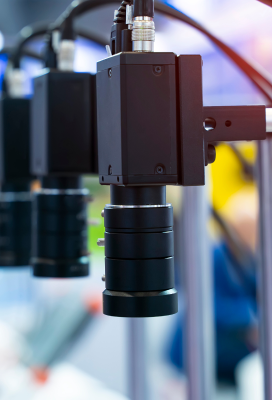
This involves extraction of data directly from the machines using analog or digital devices, or putting sensors on the machines to collect and analyze the data from the output parameters of the machines.
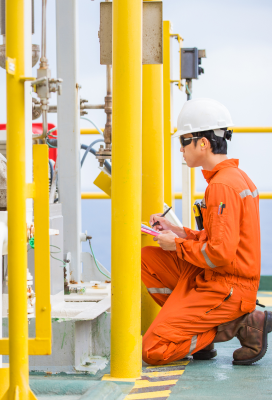
It strives to find the faults at the beginning of its occurrence with the help of the data collected by monitoring electric motors and rotating equipment. Motor current analysis, infrared thermography, vibration analysis, and acoustic analysis are a few of the techniques used for this purpose. The advantages of motor condition monitoring are enhanced reliability, reduced downtime, low replacement costs and better spare management.
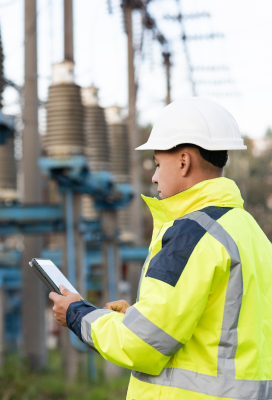
It helps to monitor several conditional parameters of a transformer to identify any small change that can indicate an impending failure. Condition Monitoring of Transformers can be classified into two types: Working condition monitoring – This monitors all parameters of a transformer and takes corrective actions to keep them within prescribed limits.Emergency condition monitoring – This method brings out the equipment from its regular working and it is monitored for emergency breakdowns or mishaps.
Nanoprecise Sci Corp
Nanoprecise Sci Corp is an end-to-end solution provider that offers Machine Condition Monitoring Services to help prevent unplanned downtime. Nanoprecise specializes in the delivery of comprehensive, cloud-based solutions for the lifecycle monitoring of equipment, using IoT, AI and Data science applications.
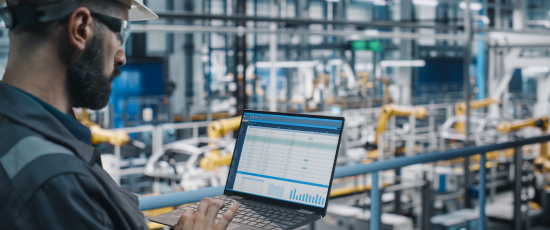
Remote Monitoring
We at Nanoprecise implement sensors on your critical rotating equipment to continuously monitor for any abnormalities in 6 important parameters and detect potential failures with far more time sensitivity than route-based monitoring and at a lower expense than traditional wired systems. Our sensors use very less power and are water & dust resistant.

Near Real-time Alerts
The condition monitoring system from Nanoprecise brings data to your fingertips. Our sensors can send near real-time information about the health & performance of machines and offers 360-degree alerts from the factory on-site to the concerned engineers. The team can then analyze the asset’s health information and allow the technicians to take prescriptive maintenance action to address the issue before an unexpected failure.
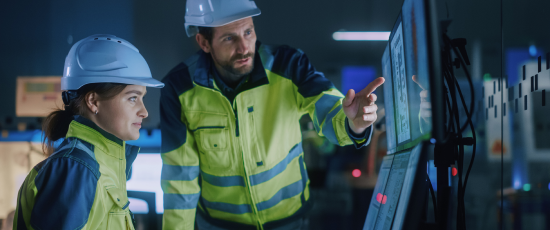
Continuous Monitoring
Continuous monitoring is imperative for production critical machinery. Depending upon the application, Nanoprecise offers a range of solutions for machine condition monitoring to ensure that your assets run at their optimum levels. Nanoprecise condition monitoring solutions include hardware selection, system configuration and integration.
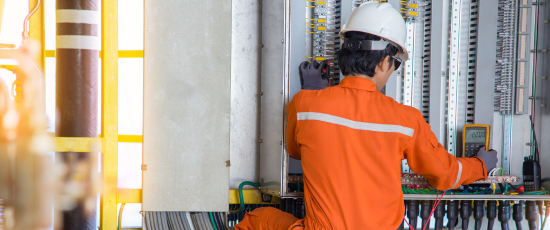
Troubleshooting
Due to several years of experience in many sectors and applications, experts at Nanoprecise can identify and troubleshoot defects quickly. First, different types of information are incorporated into the analysis. Our troubleshooting experts can then immediately identify malfunctions and devise solutions & countermeasures.
Request a Call Back
Frequently Asked Questions
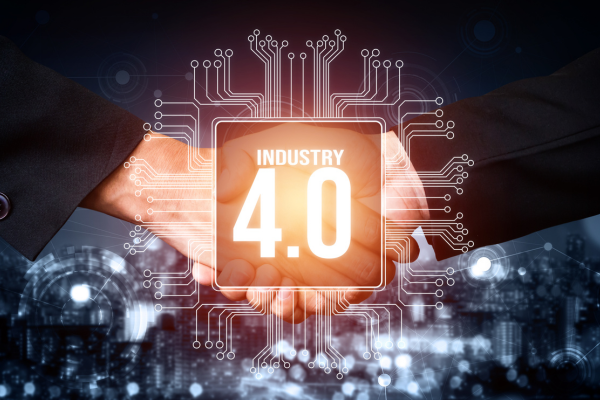
Let us show you how!
Explore the transformative potential of predictive maintenance. At Nanoprecise, we specialize in tailoring predictive maintenance to your unique needs. Reach out today, and together, let’s pave the way for a more efficient, profitable and sustainable future.