Protect Your Assets with Condition Monitoring of Transformers
Remote and Onsite Condition Monitoring of Transformers.
Why Condition Monitoring of Transformers is Essential ?
Transformers are essential in keeping power flow smooth. Over time, however, transformers will wear out due to environmental and operational stress. This can lead to unexpected failures, downtime, and costly breakdowns.
Regular condition monitoring of transformers helps catch issues early, ensuring reliable performance and avoiding unplanned downtime.
Learn more about TransformerLF: Smart Transformer Monitoring
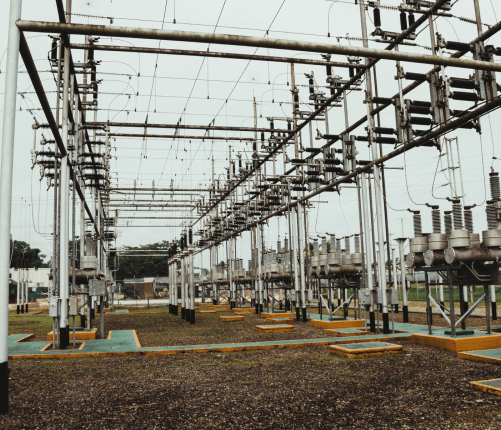
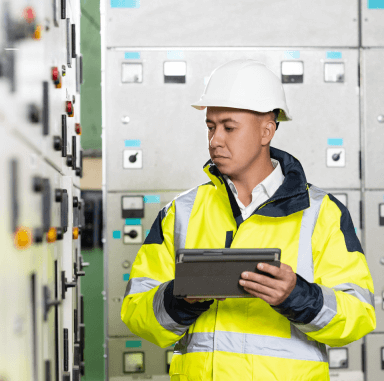
The Benefits of Condition Monitoring of Transformers
By continuously monitoring your transformers, you can:
- Detect early issues like overheating or insulation breakdowns and enable a prevention maintenance approach instead of a reactive one.
- Helps reduce repair costs by addressing problems before they become expensive operational issues.
- Extend the lifespan of transformers by reducing the need for emergency or unexpected replacements.
- Ensure a consistent power supply, especially for critical operations in the plant
- Prevent safety hazards like fires or electrical shocks and ensure plant personal safety.
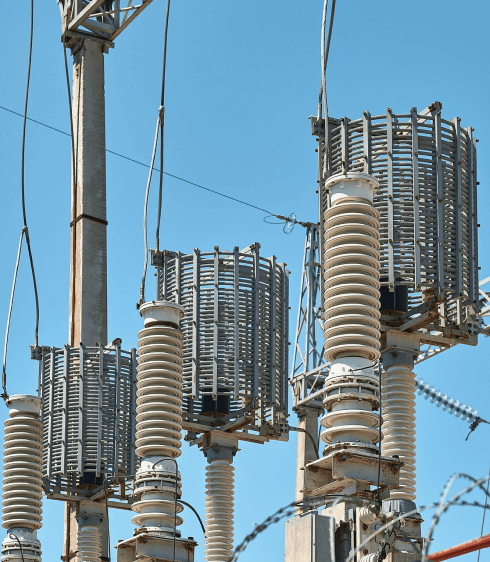
What Parameters Should be considered while performing Condition Monitoring of Transformers?
Multi-parameter condition monitoring of transformers involves tracking critical factors that impact their health.
- Advanced wireless sensors measure acoustic emissions (up to 160kHz) to detect early faults.
- Monitoring vibrations, temperature, humidity, and magnetic flux is also important. These parameter measurements ensure the early detection of issues, such as overheating or insulation breakdown, which helps prevent costly failures and extend the transformer’s operational life.
- Edge sensor technology provides insights and data to ensure reliability in transformer operations.
Nanoprecise is Leading the Way in Condition Monitoring of Transformers
Nanoprecise’s TransformerLF makes it simple to monitor transformers. It collects data on key factors like acoustic emission, humidity, temperature, and vibrations. It helps industries and plant personnel with critical transformer assets track them remotely through a web or mobile AI-driven application. The system and solution are enabled by IOT sensors, which are very easy to install, don’t require any special setup, and ensure security with strong encryption.
The solution from Nanoprecise designed for Transformers helps know when a part might fail, giving enough time for maintenance. It predicts the Remaining Useful Life of the transformer. The AI analytics part of the solution starts detecting issues, in most cases, within just five days, and helps reduce unnecessary false alerts so that the plant managers only focus on real problems and not waste time and effort on false alarms
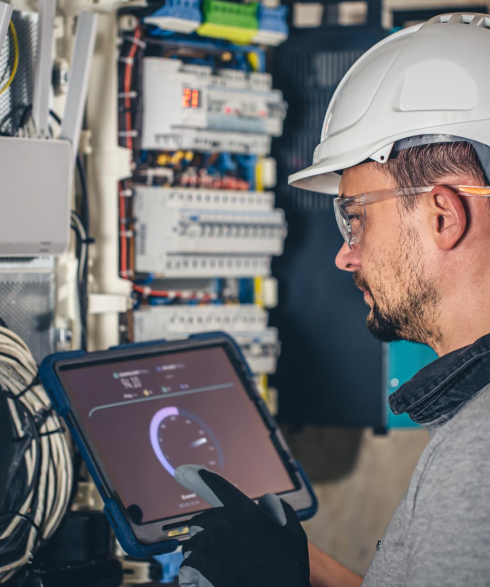
Request a Call Back
Frequently Asked Questions
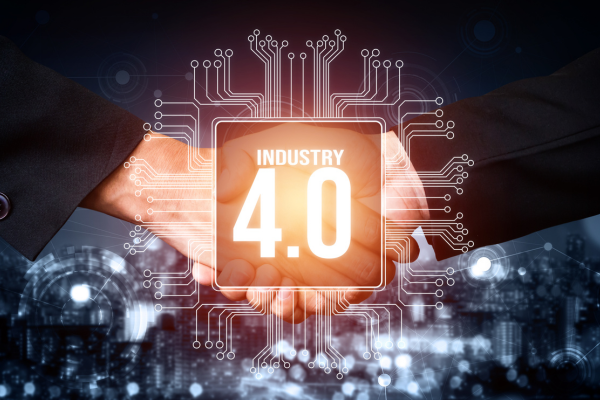
Let us show you how!
Explore the transformative potential of predictive maintenance. At Nanoprecise, we specialize in tailoring predictive maintenance to your unique needs. Reach out today, and together, let’s pave the way for a more efficient, profitable and sustainable future.