Wireless Predictive Maintenance: A New Way to Keep Your Machines Running at Peak Performance.
Wireless Predictive Maintenance is a data-driven, proactive approach that monitors the condition of the industrial assets along with its performance in real-time, to predict failures. It uses a combination of condition monitoring sensors, and data science, to identify the early signs of failures.
Introduction to wireless predictive maintenance
Wireless predictive maintenance is a new way to ensure that the machines are running at their peak performance. It comprises of innovative technologies like internet of Things (IoT) and Artificial Intelligence (AI), that helps organizations to implement global predictive maintenance programs across their manufacturing plants.
It focusses on leveraging the power of the internet of things, wireless Industrial IoT sensors, and machine learning for real-time insight into machinery performance. This technology is pioneering a new era in the manufacturing industry because of its capability to improve the productivity and uptime of machines while limiting downtime.
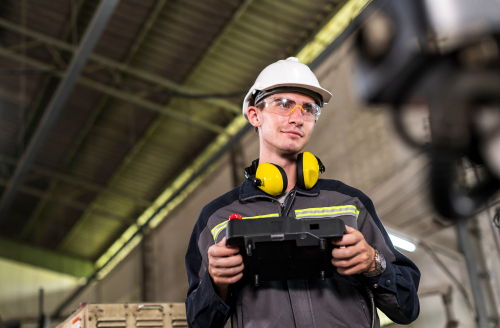
How does wireless predictive maintenance work?
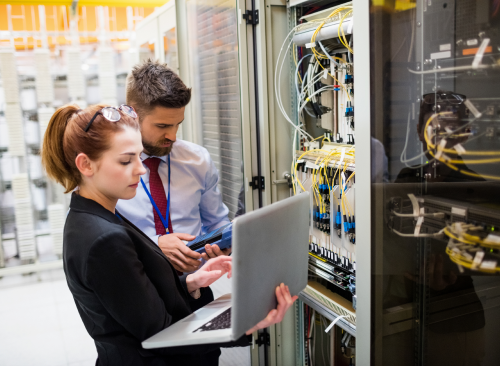
Wireless Predictive Maintenance is a technique that includes continuous monitoring of the health & performance of machines, to investigate their output parameters such as Vibrations or Sound, inorder to acquire meaningful insights about its future performance. This approach helps maintenance & reliability professionals to identify faults that may lead to failures in advance.
The technique involves installing wireless sensors to collect data on machine performance, and analyzing this data to obtain meaningful insights, to identify the initial signs of failures in assets, which in turn is used to predict when the equipment will fail. This provides maintenance engineers with ample amount of time to undertake preventative actions, thereby maximizing the uptime of machines.
Wireless Predictive Maintenance is a technique that includes continuous monitoring of the health & performance of machines, to investigate their output parameters such as Vibrations or Sound, inorder to acquire meaningful insights about its future performance. This approach helps maintenance & reliability professionals to identify faults that may lead to failures in advance.
What does this mean?
The automated solution will evaluate different machine parts & their condition, and give a prediction on when they might need maintenance.
What does this mean for businesses?
Maintenance professionals can plan ahead and schedule preventative maintenance before anything goes wrong. This way, manufacturing & production plants can avoid costly downtime – and deliver higher quality products to customers, thereby maintaining their competitive edge.
Why is it a great investment for my company?
Wireless predictive maintenance is an innovative technology that can be a valuable asset to organizations. It offers many benefits to organizations, such as:
- Improved productivity and uptime while limiting downtime
- Identifying potential failures before they happen
- Increased workplace safety
Increased lifespan of equipment setsThese benefits show how wireless predictive maintenance can be beneficial for manufacturers & operators in the long run. And in the short term, it will lead to increased efficiency.
By investing in wireless predictive maintenance, businesses can monitor machines better than ever before, and operators can take corrective actions to prevent unplanned downtime. Wireless Industrial IoT sensors capture data on the machine performance and this information is then sent wirelessly to the server where it’s stored for analysis with machine learning software – which means stakeholders will know if there’s an issue before it becomes a problem!
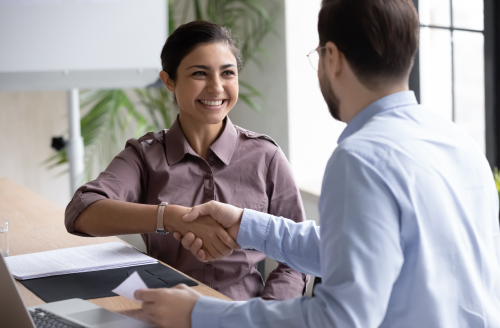
What are some of the benefits of using this new technology?

Predictive maintenance programs are able to identify potential failures before they happen. When there is an early sign of failure, predictive maintenance solutions alert technicians so that operators can take corrective actions before the equipment fails.

Wireless predictive maintenance solutions give technicians and engineers enough time to schedule repairs, thus reducing unplanned downtime.

By identifying early signs and predicting faults in advance, wireless predictive maintenance tools reduce the number of equipment failures.

By reducing the time needed for the manual data collection and analysis, wireless predictive maintenance enhances the safety and efficiency of the business operation.

Wireless predictive maintenance when implemented appropriately, can significantly improve the operational excellence of the whole manufacturing operation. It can also increase the asset lifetime, by allowing professionals to take preventive actions at the right time.

It significantly reduces the amount of time & money required for maintenance activities, by optimizing the available resources.
Conclusion
Predictive maintenance is a great way to keep your machines running at peak performance without having to take them offline for maintenance. The best part is, it doesn’t require any human involvement, making it a completely autonomous process. Wireless predictive maintenance programs can automatically monitor your machines and trigger an alert if they sense something is amiss, thereby helping to prevent unplanned downtime of machines. And it’s not just the equipment you’ll be saving, either. These programs can also reduce safety risks, reduce costs, and improve efficiency.
Request a Call Back
Frequently Asked Questions
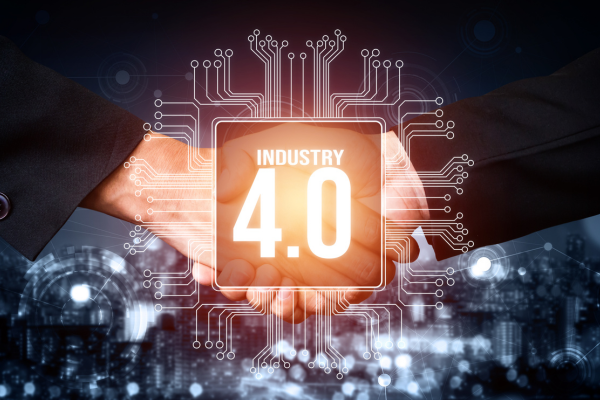
Let us show you how!
Explore the transformative potential of predictive maintenance. At Nanoprecise, we specialize in tailoring predictive maintenance to your unique needs. Reach out today, and together, let’s pave the way for a more efficient, profitable and sustainable future.