In today’s highly competitive manufacturing landscape, operational efficiency and sustainability are no longer just aspirational goals—they are critical imperatives. Industrial motors, essential to manufacturing processes, represent one of the largest energy consumption areas in the sector. Unfortunately, a significant portion of that energy is often lost due to operational inefficiencies.
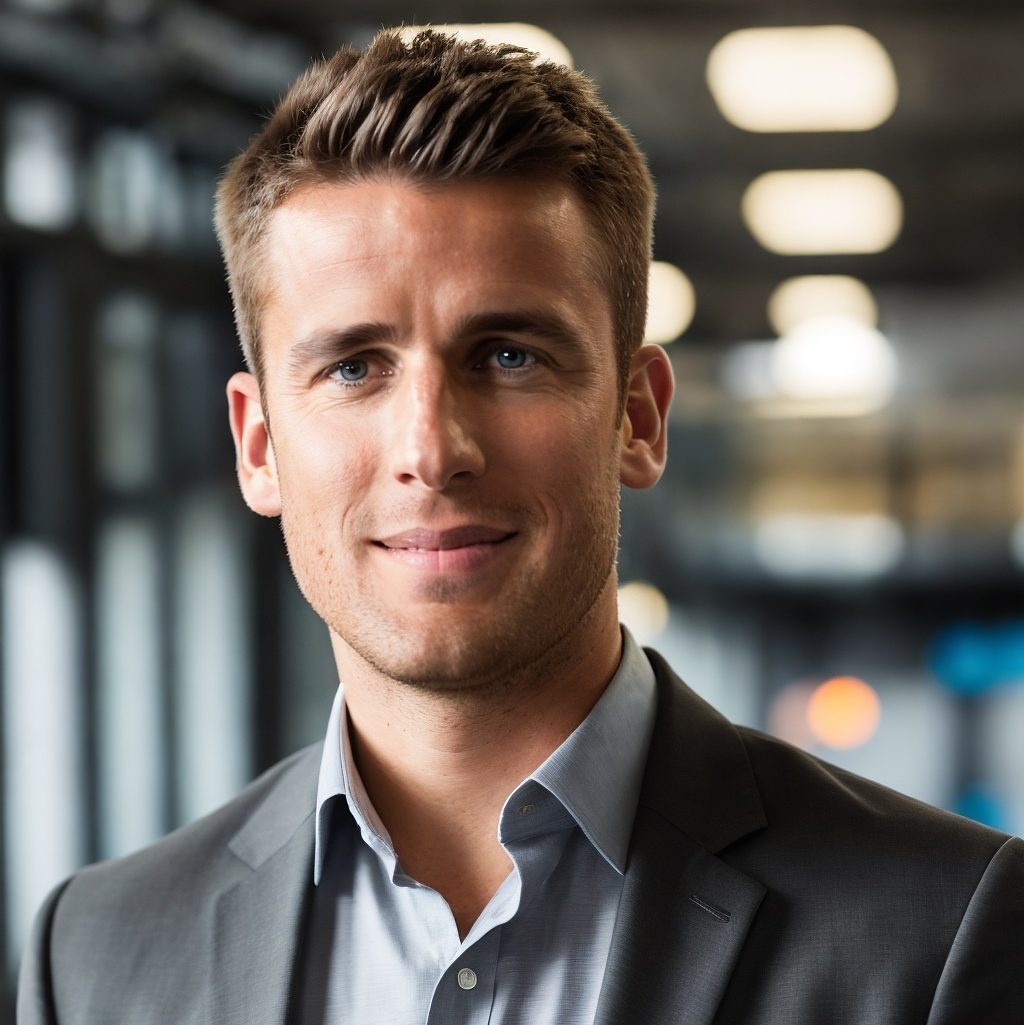
VP Product, Nanoprecise
At Nanoprecise, we specialize in leveraging advanced condition monitoring technologies to pinpoint inefficiencies and accurately identify their root causes. By enabling timely maintenance interventions, we help improve both energy consumption and equipment reliability, driving sustainable practices and operational excellence in manufacturing.
The Critical Role of Industrial Motor Efficiency in Manufacturing
Industrial motors power a vast array of critical applications within the manufacturing industry, from assembly lines to heavy machinery. Research indicates that these motors account for approximately 60% of all electrical energy consumption in manufacturing environments. Unfortunately, common inefficiencies—such as imbalance, misalignment, mechanical wear, and improper operation—can lead to substantial energy waste. This not only costs companies millions in excess utility expenses but also negatively impacts environmental sustainability.
Improving motor efficiency is therefore not just a financial imperative but a crucial element of corporate responsibility. By addressing these inefficiencies, manufacturers can significantly reduce energy consumption, lower costs, and contribute to a more sustainable future.
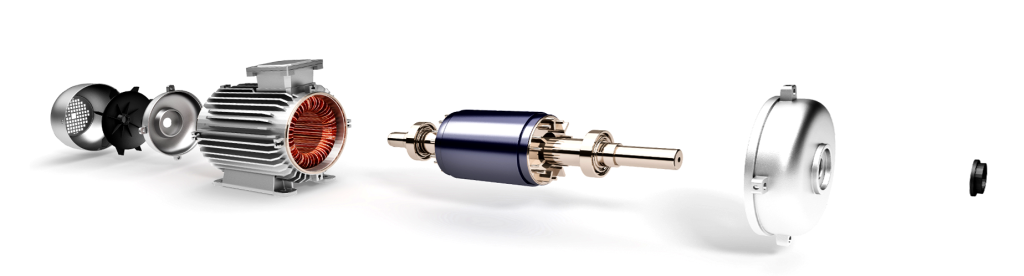
Enhancing the Efficiency and Longevity of Machinery with Condition Monitoring
Condition monitoring involves the use of non-invasive diagnostic techniques—such as vibration analysis, ultrasound, infrared thermography, and oil analysis—to detect anomalies in the operation or health of industrial machinery. By strategically applying a combination of these technologies, it is possible to identify early signs of wear, or other developing issues, before they escalate into serious problems.
This predictive maintenance approach helps prevent unexpected breakdowns and ensures that machines operate at optimal efficiency, reducing unnecessary power consumption and extending the equipment’s life. As a result, the total cost of ownership is significantly reduced, with lower maintenance and operating costs contributing to long-term savings and increased equipment reliability.
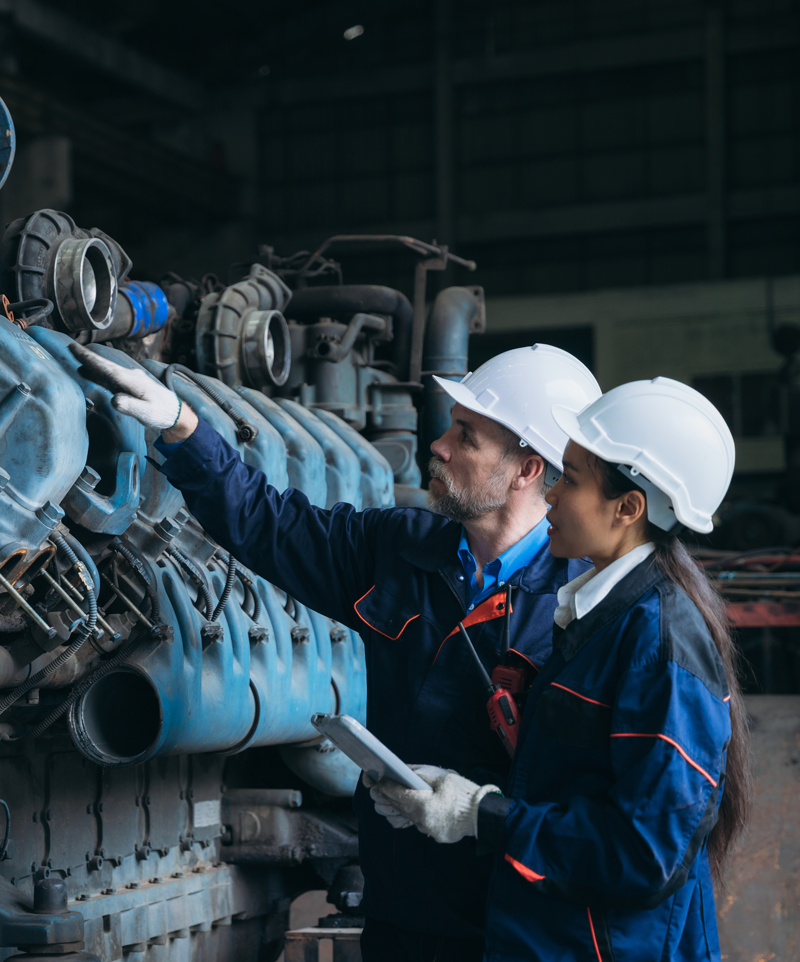
Nanoprecise Revolutionizing Condition Monitoring with Advanced Sensor Technology and AI
At Nanoprecise, we combine cutting-edge edge-powered sensor technology with AI-driven algorithms to deliver continuous monitoring and diagnostic capabilities. Our integrated system merges multiple condition monitoring technologies into a single hardware design, enabling us to detect even the slightest deviations from normal operation. This early detection allows for timely maintenance planning, preventing costly breakdowns and ensuring equipment operates at peak efficiency.
Through our case studies, we’ve demonstrated the ability to reduce energy consumption by up to 30% in some scenarios, significantly lowering operational costs and enhancing energy efficiency for our clients.
In addition, we’ve embraced Energy-Centered Maintenance (ECM) with our innovative Energy Dashboard, which leverages data analytics to optimize energy consumption and improve maintenance decisions. This approach not only ensures equipment availability but also prioritizes energy optimization to promote sustainability and cost-effectiveness. By utilizing flux sensor technology and advanced algorithms, our solution monitors and analyzes electromagnetic forces in electric motors, identifying energy consumption deviations that may signal potential inefficiencies or faults.
Implementing Effective Condition Monitoring: A Step-by-Step Guide
- Equipment Selection: Begin with a criticality analysis to identify high-risk or high-impact equipment and potential fault modes. Next, evaluate the return on investment (ROI) of applying condition monitoring to these assets to determine the most suitable candidates.
- Technology Evaluation: Based on the identified equipment and fault modes, select the appropriate technology that will provide the necessary data and insights. This ensures that developing failures are detected early and changes in energy consumption are accurately measured and acted upon.
- Sensor Installation: Ensure that sensors are strategically installed in the right locations to monitor various components and fault modes of interest. Proper installation is crucial for reliable, repeatable data collection over an extended period, all while not interfering with daily operations and maintenance tasks.
- Continuous Monitoring: Once operational, our system provides real-time monitoring, analyzing data both on the edge and in the cloud. This allows for the detection of deviations that could indicate inefficiencies or developing faults. The system delivers actionable insights, enabling timely maintenance planning.
- Insight to Action: The most critical step is translating insights into action. By addressing issues early, companies can avoid costly repairs, reduce energy consumption, and maintain optimal productivity levels. Without this step, the preceding efforts lose their value.
Case Study Spotlight: Analytics-Driven Energy Savings in Water Utilities
In collaboration with a major UK water utility, Nanoprecise deployed ECM olution across 40+ reservoirs and 300+ water pumping stations. One critical insight emerged: a resonance issue in a variable speed pump was causing a detectable increase in vibration between 709 and 739 RPMs, driving up energy consumption.
Using our NrgMonitor, we analyzed stray magnetic flux data and detected three distinct shifts in energy usage, directly correlating with the high points on the RMS vibration chart. Further time-synched data analysis showed a strong link between motor speed, energy consumption, and vibration levels. This multidimensional insight enabled the utility to prioritize repairs, reducing operational costs and excess energy consumption while enhancing reliability across over 25,000 km of water mains.
This case study highlights how continuous monitoring with analytics-based insights can drive efficiency, lower emissions, and support sustainability goals in essential infrastructure.

The Future of Maintenance: Integrating IoT, AI, and Predictive Analytics
Integration of IoT and AI: Ongoing innovations in predictive maintenance technologies are increasingly integrating the Internet of Things (IoT) and artificial intelligence (AI). This fusion enhances analytical capabilities and enables sophisticated automation, bringing the right technical innovations to maintenance technicians and decision-makers. As a result, there is an exponential increase in the efficiency of condition monitoring and subsequent maintenance tasks.
Advancements in Predictive Analytics: Technological advancements, including ever-improving sensor technology (lower power consumption, better connectivity), multi-variant change detection, and increasingly accurate fault and root cause prescriptions, promise to revolutionize maintenance strategies. These innovations are set to improve equipment efficiency and boost overall sustainability.
Driving Industry Changes: As IoT, AI, and predictive analytics technologies continue to evolve, they will reshape the landscape of maintenance practices. This evolution will drive greater energy efficiency, reduce environmental impact, and ultimately transform industries by setting new standards for sustainability and operational excellence.
In Conclusion
Condition monitoring is more than just a maintenance tool; it is a gateway to substantial energy savings and enhanced operational efficiencies. By adopting advanced predictive maintenance technologies, like those offered by Nanoprecise, manufacturers can not only boost equipment reliability but also significantly reduce energy costs and actively contribute to global sustainability efforts.
We invite you to join us on this journey towards smarter, more efficient maintenance solutions, and to be a part of a movement that drives both economic and environmental benefits.