Predictive Maintenance Tools
Maintenance is an extremely crucial aspect of a wide range of organizations, particularly the ones associated with manufacturing. It is vital to a functioning production and may have a significant impact your bottom-line profits.
Introduction
Maintenance can also aid in managing expenses by doing smaller and less costly repairs earlier, rather than waiting for major repairs.
In cases where equipment and assets are not provided with proper maintenance then they may malfunction and even break down suddenly, causing downtime.
Today advanced Predictive Maintenance Tools are available that you may use to ensure the maintenance and upkeep of your assets while reducing human efforts to collect routine data and boosting efficiency.
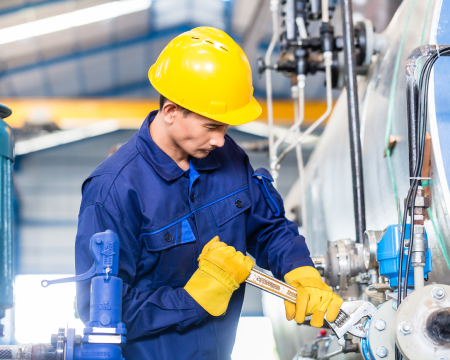
What is Predictive Maintenance?
In simplest terms, predictive maintenance refers to a data-driven approach that analyses the condition of the machines & equipment sets in real-time, to prevent unplanned downtime and emergency repair expenses.
It is a proactive analysis process that allows you to make sure that all the important equipment, devices, and assets are functioning efficiently.
With the assistance of Predictive Maintenance Tools, you can determine the overall condition of a certain asset and subsequently predict when it would need maintenance.
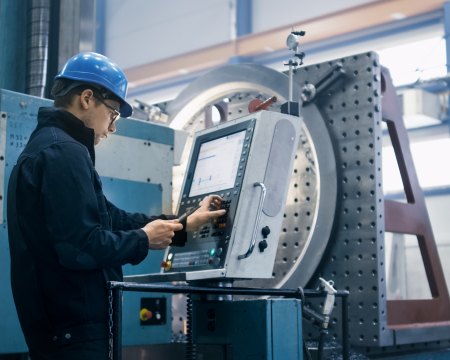
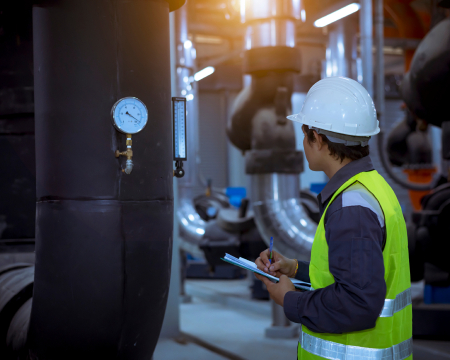
Businesses typically suffer a lot due to sudden equipment breakdown, especially if it leads to production interruption.
When the health & performance of the assets are monitored in near real-time through automated systems, as opposed to quarterly manual inspections, it helps maintenance & reliability professionals to focus on the bad actors and take appropriate remedial action in order to prevent downtime.
Predictive Maintenance Tools
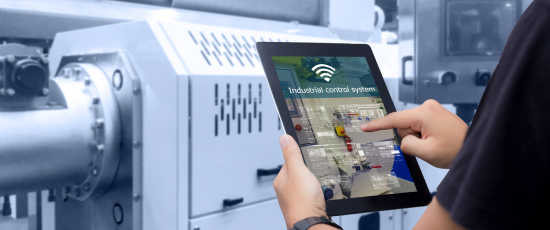
Wireless Industrial IoT Sensors
Wireless industrial IoT sensors can be used to measure & collect different output parameters of equipment sets, such as temperature, pressure, humidity, and vibration among others. These sensors collect complex machine health data without wires and can transmit data wirelessly over long distances, thereby overcoming the challenges of traditional wired sensors.
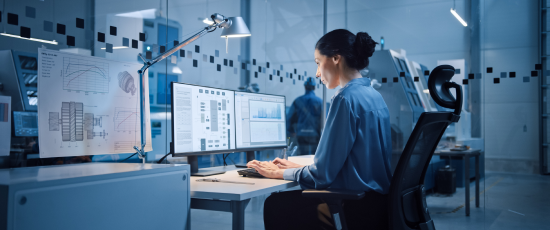
Predictive Maintenance Software
Predictive maintenance software is a powerful asset monitoring tool that typically uses complex data processing algorithms for the purpose of analyzing asset performance and predicting potential equipment failures. Maintenance and Reliability professionals can use this tool to subsequently create a proactive upkeep strategy that can cut down unplanned downtime.
Instead of waiting until an asset breaks down to perform a repair, predictive maintenance software would automate the maintenance procedure by scheduling upkeeps at the very first sign of a potential equipment problem.
Near real-time monitoring of an equipment set is possible with the help of automated predictive maintenance software, and it has the ability to competently track equipment performance over time. These tools, such as sensors and gauges, can monitor any kind of changes in equipment vibrations, temperature, or sound, in order to flag potential issues. This information subsequently syncs with the software that runs predictive maintenance analytics in order to competently evaluate equipment performance and determine whether repairs are needed or the asset has to be wholly replaced.
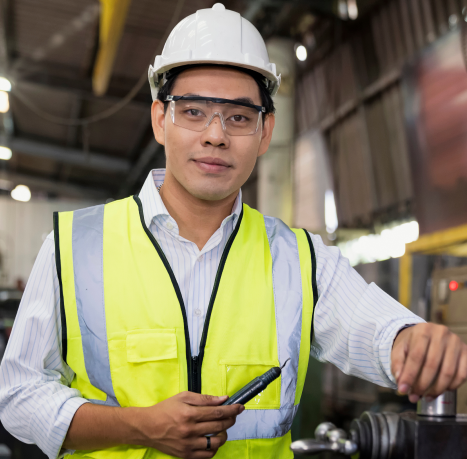
How can we help?
It is time to take initiative and leverage proper predictive maintenance solutions that allow your team to make informed decisions in time.
For gaining a competitive edge in the market, Nanoprecise Sci Corp uses advanced analytics to predict potential problems and resolve them before they arise.
Our latest predictive maintenance technologies can have a real impact on your production efficiency, and ensure fewer incidents and outages.
Request a Call Back
Frequently Asked Questions
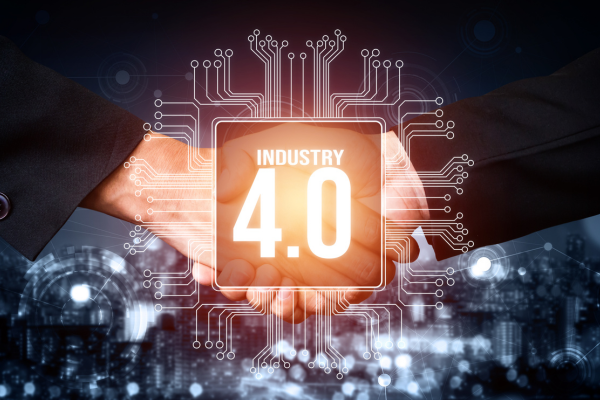
Let us show you how!
Explore the transformative potential of predictive maintenance. At Nanoprecise, we specialize in tailoring predictive maintenance to your unique needs. Reach out today, and together, let’s pave the way for a more efficient, profitable and sustainable future.