Predictive Maintenance Software
by Nanoprecise
What is Predictive Maintenance Software?
Predictive maintenance (PdM) software is a specialized tool designed to monitor, analyze, and predict the condition of an equipment in real-time. It aims to predict failures and breakdowns that helps Manufacturing Industries strategize solutions before the failure happens.
The Predictive Maintenance Software makes this possible by analyzing data gathered from sensors, machines, or external systems through advanced algorithms and data analytics. Such a proactive approach helps to improve the performance of the machine with detailed insight and reduce any unplanned downtime. It also directly reduces the maintenance cost in the process by identifying fault patterns and early indicators of issues.
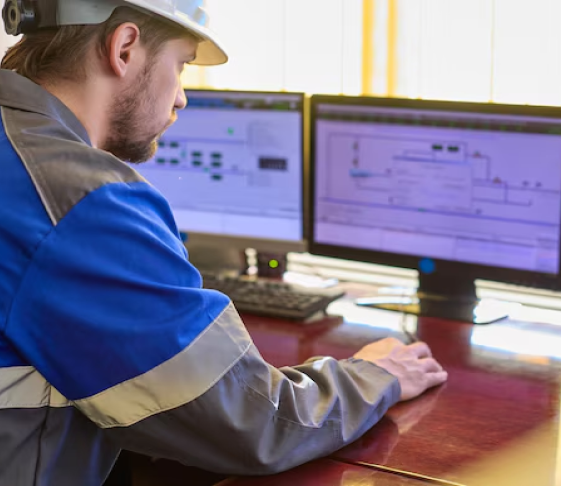
The role of AI and IIoT in predictive maintenance
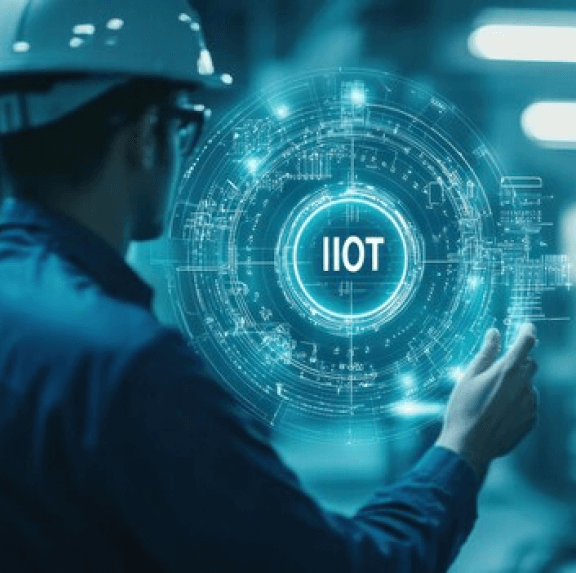
The combination of Artificial Intelligence (AI) and the Industrial Internet of Things (IIoT) has transformed the way Predictive Maintenance Software can work. While AI allows machines to learn from past data, making predictions more accurate and complex failure patterns more visible. IIoT on the other hand, links physical equipment to digital platforms, making it easier to collect data from sensors, monitor machines around the clock and in real-time to measure performance better.
AI and IIoT when combined together creates smarter Predictive Maintenance Software by:
- Automating the process of data analysis
- Enhancing precision in detecting faults
- Reducing human intervention as much as possible during monitoring
- Scaling maintenance strategies across large and complex operations without hassle and additional cost
Understanding the evolution of PdM from reactive to proactive approach

Predictive Maintenance Software has come a long way. In the past, companies followed a reactive approach, repairing equipment only after it broke down, which was both expensive and inefficient. The next improvement was preventive maintenance, where routine checks were performed on a set schedule, regardless of whether problems existed.
Now, with Predictive Maintenance Software, predictive maintenance takes a more proactive approach where assistance is offered with the help of advanced data collection, AI, and machine learning. In fact, Predictive Maintenance Software can accurately predict equipment failures, that enables a business to carry out maintenance activities of their equipment only when it’s truly needed.
Energy as a core component in Predictive Maintenance Software
A key focus in predictive maintenance today is energy management. As Industries work to meet sustainability targets and cut down on energy use, Predictive Maintenance Software can help pinpoint inefficiencies caused by equipment issues. When machines start consuming more energy due to wear and tear or faults, this software can detect the problem early, allowing for timely fixes that reduce waste.
This approach, known as Energy-Centered Maintenance (ECM), goes beyond just maintaining equipment—it also tracks energy use to optimize performance. By identifying areas of excess energy consumption, Industries can not only improve the health of their machines but also lower costs and reduce their environmental impact.
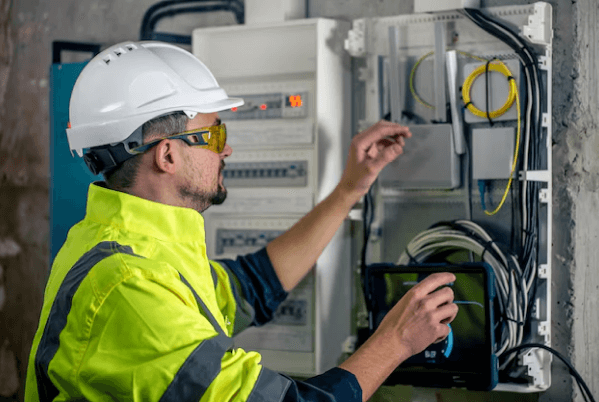
Nanoprecise’s role in Predictive Maintenance Software
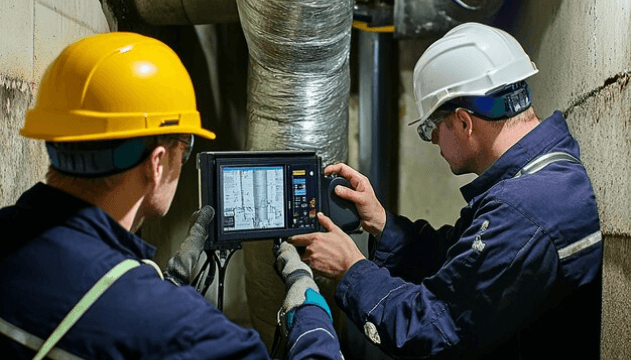
With innovation and creativity, Nanoprecise is leading the way in predictive maintenance software by combining AI and IIoT. With the help of cutting-edge 6-in-1 sensors, detailed and precise insights into the machine health is now possible. Factors like; vibration, temperature, and magnetic flux gives a comprehensive view of equipment condition.
Hence, as a solution, it can;
- Detect issues early reducing potential downtime
- Optimize energy usage supporting sustainability
- Offer secure and scalable systems that are easy to integrate
With Nanoprecise’s predictive maintenance software, companies now can extend the lifespan of their assets, minimize operational risks, and meet their energy efficiency goals in no time.
Request a Call Back
Frequently Asked Questions
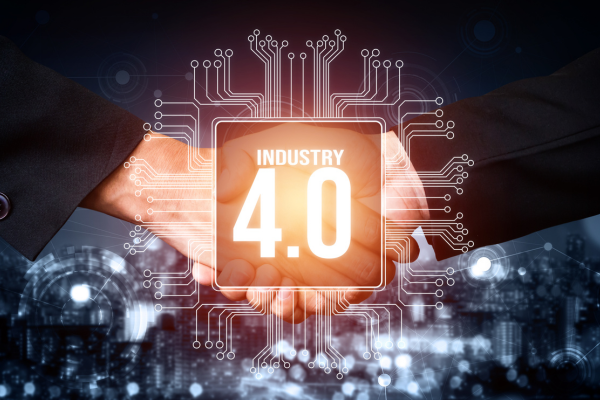
Let us show you how!
Explore the transformative potential of predictive maintenance. At Nanoprecise, we specialize in tailoring predictive maintenance to your unique needs. Reach out today, and together, let’s pave the way for a more efficient, profitable and sustainable future.