Predictive Maintenance in Chemical Plant
Today, the popularity of preventive maintenance has been eclipsed by a data-driven, and more effective technique known as predictive maintenance. This is mainly because predictive maintenance helps in making complex decisions and reduces unscheduled downtime, and improves chemical plant efficiency.
Chemical Plant Maintenance
For any chemical plant owner, unplanned downtime of equipment sets is bad news. Missed output quotas, higher maintenance expenses, and even hazards to staff safety are all possible outcomes.
Preventive maintenance, which is scheduled after a given amount of time regardless of whether a fault has been identified, used to be a classic technique of reducing unplanned asset downtime.
This was based on the idea that all assets would ultimately fail, thus it’s best to maintain or even replace them after a given amount of time has passed.
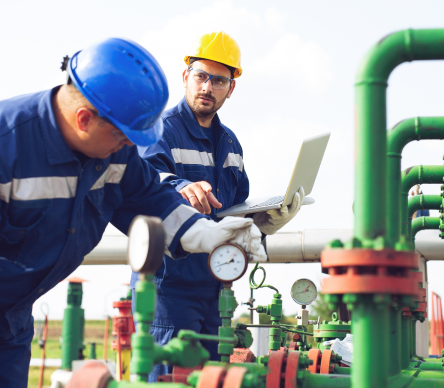
Why is predictive maintenance the call of the hour?
Predictive maintenance has proven to be more effective in reducing unplanned downtime at several chemical plants. This is due to the fact that it gathers and analyzes actual motor/asset data in order to predict when a certain motor/asset will fail.
Your chemical plant’s maintenance engineer will be notified as an asset starts to show signs of failure. This would give the engineer enough time to schedule repairs.
Advanced predictive maintenance systems can detect the developing issues way before it happens, giving plant owners enough time to plan maintenance activities thereby reducing (and even eliminating) unexpected downtime.
The promise of advanced wireless predictive maintenance technologies has piqued the interest of the chemicals industry, as well as many others. These new approaches hold enticing potential.
They warn operators when and how a component is likely to go wrong in the future with a high level of confidence, by using machine-learning algorithms to sift through previous as well as current machine performance and failure data. It helps to reduce the impact of equipment failures and the cost of measures to prevent such failures.
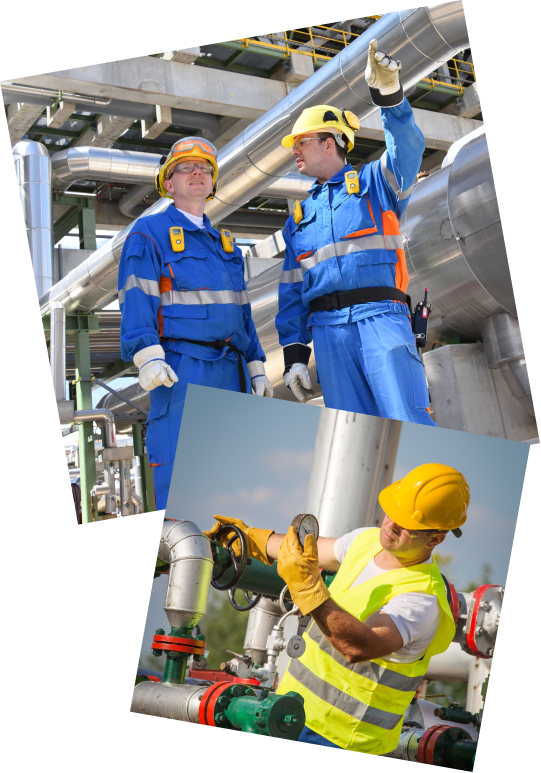
Smart data equals better decision
Predictive Maintenance offers real-time insights about the health and performance of the machines and equipment sets in a chemical plant, helping chemical manufacturers prevent equipment failure and avoid unplanned downtime. It empowers maintenance and reliability professionals with the right data at the right time, allowing them to make smarter and better decisions.
Better utilization of resources
A predictive maintenance strategy allows for better utilization of maintenance resources.
This is due to the fact that maintenance staff is dispatched only after an asset defect has been identified. As a result, the maintenance workload is reduced, which reduces the plant’s operating costs.
This ensures that the resources are utilized to their utmost potential.
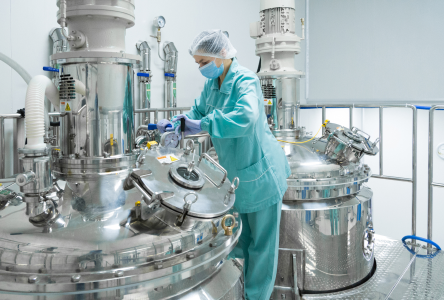
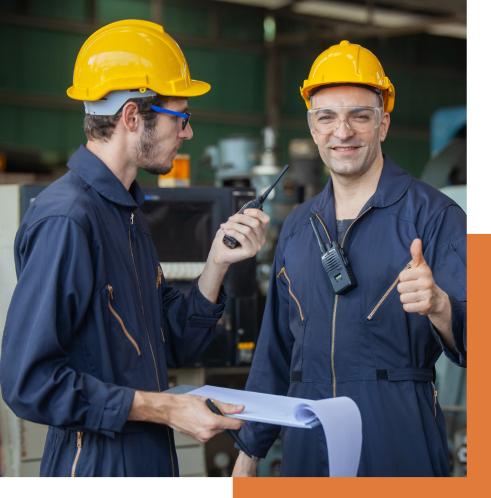
Choose Nanoprecise
Asset failures occur without warning, and the problem is to recognize the warning indications in time to schedule repairs. Our automated AI-based predictive maintenance solutions provide real-time information, with a key focus on early detection of even minor changes in machine operations before they have an impact on output or cause downtime.
Our AI-driven analytics can help your chemical company achieve new levels of reliability by extending asset life and influencing top-line growth by predicting potential machine problems. Our wireless predictive maintenance solutions powered by IoT gives chemical manufacturing companies, a lot of flexibility and agility.
Request a Call Back
Frequently Asked Questions
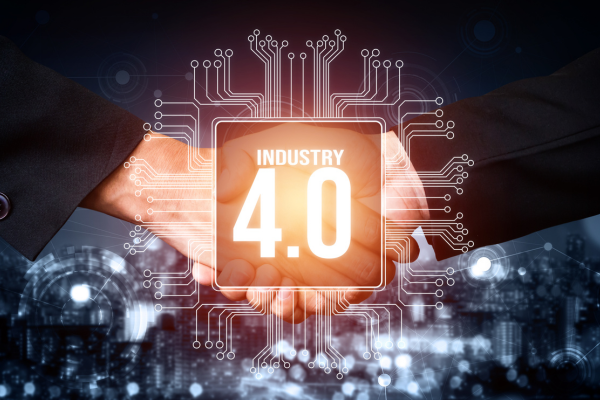
Let us show you how!
Explore the transformative potential of predictive maintenance. At Nanoprecise, we specialize in tailoring predictive maintenance to your unique needs. Reach out today, and together, let’s pave the way for a more efficient, profitable and sustainable future.