Predictive Maintenance in Cement Plant
Cement Manufacturing Sector
The global cement industry is a giant player contributing to the world economy. As of 2020, the cement industry contributed an impressive $313 Billion to the global GDP. Not only does it provide employment to a vast number of people, but also have – over the decades – played a very important part, in the growth of infrastructure around the world.
It is one of the oldest and complex manufacturing industries in the world, and is characterized by continuous and high-volume production. The manufacturing process involves crushing, blending, heating and cooling of raw materials, to produce the final product which is used in a number of applications in our day-to-day life. Unexpected failures or shutdowns of any of these practices will have significant impact on the efficiency of the overall manufacturing operation.
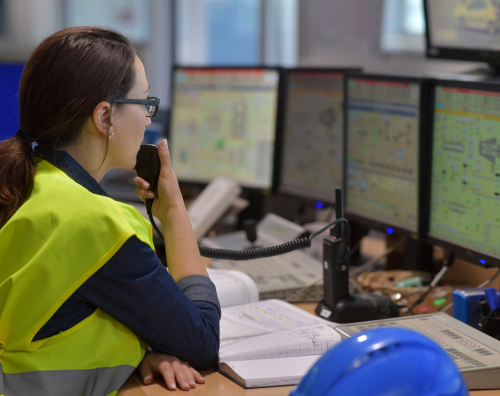
Cement Manufacturing
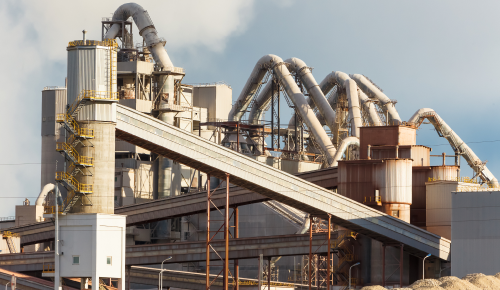
The important steps that constitute the cement manufacturing process are:
- Mixing of Limestone and Clay in the Quarry.
- Blending the mixture in exact proportions
- Heating up the ingredients in the kiln and subsequent cooling.
- Storing the final product in Clinker Store
- Packing and dispatching using conveyor belts and/or other transportation means.
The basic process of cement production not being a secret, it is not a difficult task to keep track of all of the processes. However, the process of monitoring asset conditions in a cement manufacturing plant is a much more complicated endeavour. With diverse and complex equipment sets often placed in hard-to-reach, remote locations, the challenge of frequent manual monitoring in a cement plant is a huge challenge.
Equipment failures in cement manufacturing plants results in severe consequences for the manufacturers, with loss of production, increased maintenance costs and danger to worker safety.
Predictive Maintenance in Cement Plant
Predictive maintenance refers to the use of a data-driven approach, that analyses the equipment condition to predict when that equipment requires maintenance.
Predictive maintenance has proven to be extremely effective in reducing unplanned downtime at several cement manufacturing plants. This is due to the fact that it collects complex machine data and analyses it to provide meaningful insights for the maintenance and reliability professionals.
Advanced predictive maintenance systems can detect the developing issues way before it happens, giving plant owners enough time to plan maintenance activities thereby reducing (and even eliminating) unexpected downtime. Therefore, it is essential for the manufacturers to work with Predictive Maintenance Specialists for continuous monitoring of the machine-health, so as to improve the efficiency and reduce machine downtimes.
An integrated predictive maintenance system captures machine health data, analyses it and gauges the function of that machine, to differentiate between process upset/variation and actual faults. The data allows engineers and technicians to undertake maintenance activities and schedule repairs with increased precision and higher safety.
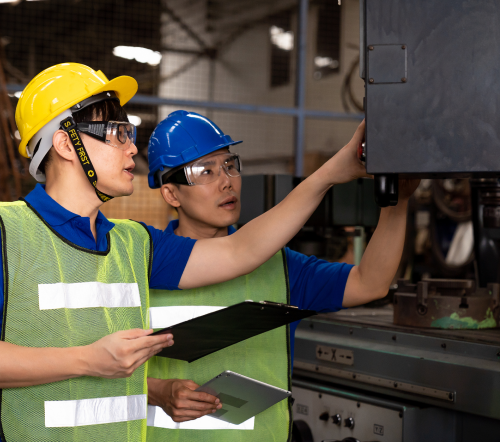
Benefits of Predictive Maintenance in Cement Plant
Predictive Maintenance offers various advantages to the operators in cement manufacturing plants. These include:

Real-Time condition Monitoring
Predictive maintenance is a revolutionary technique that offers real-time monitoring of the condition of equipment and machines, thereby helping to curb the occurrence of unplanned downtime. An integrated predictive maintenance system allows real-time monitoring of vibration, temperature, RPM and other parameters, to detect anomalies and predict failures.
Real-time insights on machine health and performance of Ball Mills, Crushers, Kilns, Clinker cooler & dryer, Roller Press, Silos or any other critical piece of machinery throughout the manufacturing processes can be achieved with an automated predictive maintenance system. This helps maintenance and reliability professionals to make faster and accurate decisions, that drive efficiency and improve the competitive advantage.

Fault prediction
An automated end-to-end predictive maintenance solution aids in the detection of anomalies and potential faults through analysis of real-time data. It offers insights into the possible wear & tear and loss of function of machinery which helps the system predict failures at an early stage.
As the variables in the environment keep changing, the system also keeps looking for signals that help diagnose faults in manufacturing systems through machine learning.

Reduced Time to Maintenance
Even with the checklist used to conduct inspections – faults often go unnoticed as it is usually not an overnight incident. The time lost to observe signs of failures would be reduced to less than half, with the implementation of a predictive maintenance system, thereby saving significant amount of time spent on data capture and analysis.

Improved Operational Efficiency
Real time information from analytics dashboard helps the users to plan maintenance activities and increase equipment uptime, leading to improved operational efficiency and optimized usage of resources.
Features of Predictive Maintenance in Cement Plants

Interconnectedness
An automated end-to-end predictive maintenance system facilitates wireless condition monitoring of equipment sets, thereby offering an interconnected network of machines.

Interoperability
The beauty of predictive maintenance lies in its ability to support wireless connectivity even with the legacy equipment, using APIs to achieve interoperability of information either on a common cloud or on premise.

Security
The system generally offers a high level of security with advanced encryption protocols to address all kinds of security issues.

Communication
Advanced Predictive Maintenance systems use one of the highest communication standards to facilitate faster and seamless data transfer
Request a Call Back
Frequently Asked Questions
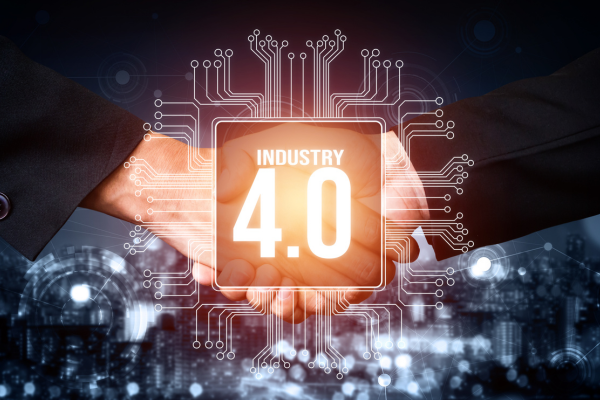
Let us show you how!
Explore the transformative potential of predictive maintenance. At Nanoprecise, we specialize in tailoring predictive maintenance to your unique needs. Reach out today, and together, let’s pave the way for a more efficient, profitable and sustainable future.