Motor Condition Monitoring
Discover the benefits of motor condition monitoring and reduce the chance of outage.
Understanding Motor Condition Monitoring
Motors are the key component in any industrial setup that helps to run machineries and any production process. The failure of these motors can cause costly downtime and operational outage. To avoid such unwanted disruptions, motor condition monitoring is important.
With continuous monitoring and assessment of the motor health, operational efficiency of the manufacturing plant is ensured. It also prevents sudden failures and helps in extending the lifespan of the machine. Again, through motor condition monitoring, issues can be identified early that enable proactive maintenance and improved reliability.
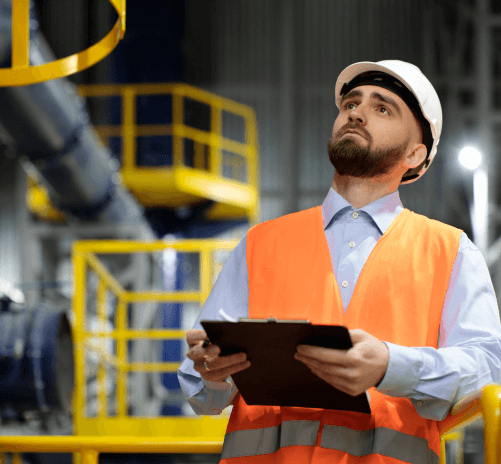
The Importance Motor Condition Monitoring (CM)
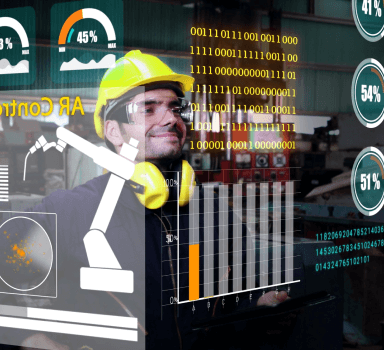
It provides key insights into the health and performance of the equipment, thereby allowing maintenance teams to take proactive measures for preventing unplanned downtime and improving the overall efficiency of manufacturing plants. The practice of Motor Condition Monitoring is an important component of predictive maintenance, as effective motor condition monitoring enables scheduled maintenance and proactive measures to be taken, preventing failures and minimizing unplanned downtime. With the increasing demand for high-quality products and the need for optimal utilization of resources, motor condition monitoring has become a critical component of manufacturing operations.
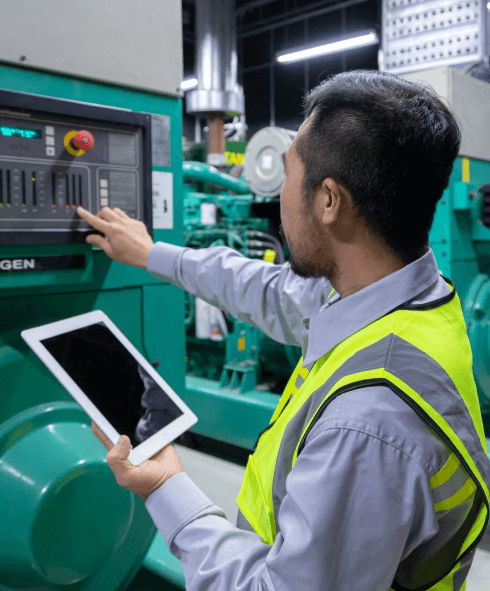
Achieve Manufacturing Excellence with Motor Condition Monitoring
Motor Condition Monitoring is a critical component in driving manufacturing excellence on a global scale. By continuously monitoring motor health, manufacturers can identify potential issues early and take proactive measures to prevent costly downtime and ensure optimal performance.
As the demand for high-quality manufacturing and sustainable manufacturing practices continues to rise, companies are increasingly turning to advanced motor condition monitoring technologies. These solutions go beyond simple performance tracking, providing detailed insights into energy consumption and carbon emissions. By leveraging these technologies, manufacturers can not only enhance operational efficiency but also significantly reduce their environmental footprint, aligning with sustainability goals and achieving long-term operational success.
Emerging Trends and Opportunities in Motor Condition Monitoring
The future of Motor Condition Monitoring looks bright, with several emerging trends and opportunities. One significant development is the integration of condition monitoring with advanced technologies like AI and machine learning (ML). This combination enables predictive maintenance, allowing manufacturers to optimize asset performance. AI-powered algorithms can identify patterns and anomalies in data, empowering maintenance teams to make informed decisions and take proactive measures to prevent downtime.
Another trend gaining traction is the adoption of cloud-based monitoring systems. These systems offer numerous benefits, including easy scalability, real-time monitoring, and cost efficiency. By utilizing cloud computing, manufacturers can achieve a comprehensive view of their industrial assets’ health and make decisions based on up-to-date information.
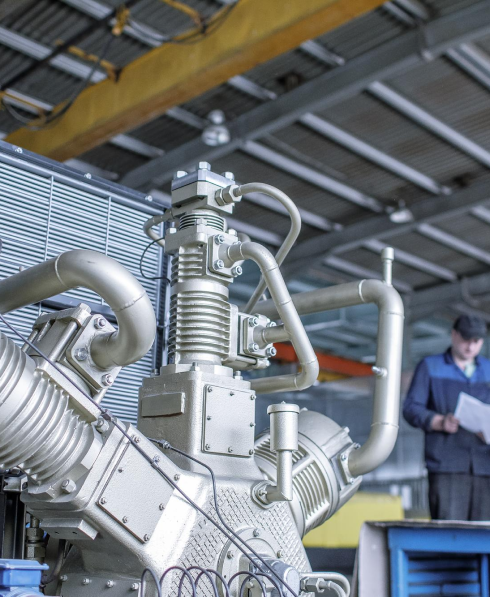
Energy Savings with Motor Condition Monitoring Solutions
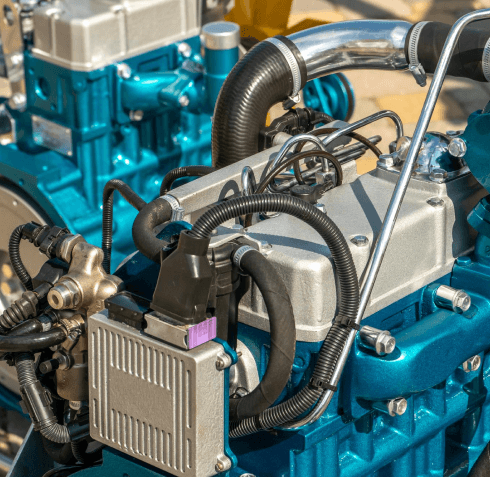
Motors and motor-driven equipment represent a staggering 65% of global energy consumption. A significant portion of this energy usage—up to 25%—is lost due to frictional losses, which can escalate by over 10% when faults are present. Furthermore, maintenance-related inefficiencies can lead to a 10-20% increase in energy costs, compounding energy consumption.
The impact of unplanned downtime is equally severe, costing the global economy over $600 billion annually. By implementing the right Motor Condition Monitoring solutions, Industries can proactively identify and address potential faults before they escalate, significantly reducing maintenance-related energy costs.
Picking the right Motor Condition Monitoring technologies such as the Nanoprecise solution not only to enhance efficiency but also to contribute to substantial energy savings and sustainability goals.
Request a Call Back
Frequently Asked Questions
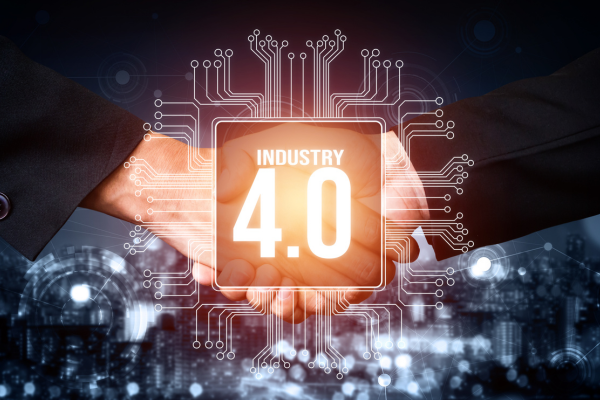
Let us show you how!
Explore the transformative potential of predictive maintenance. At Nanoprecise, we specialize in tailoring predictive maintenance to your unique needs. Reach out today, and together, let’s pave the way for a more efficient, profitable and sustainable future.