Understanding Journal Bearing Monitoring in Rotating Machinery
Journal bearing monitoring
Journal bearing monitoring refers to the practice of assessing the condition & performance of journal bearings in rotating machinery, such as engines, turbines, and generators. Journal bearings are crucial components that support rotating shafts and ensure smooth operation by reducing friction and wear. Monitoring journal bearings is essential to prevent potential failures that can cause costly downtime and even catastrophic equipment damage.
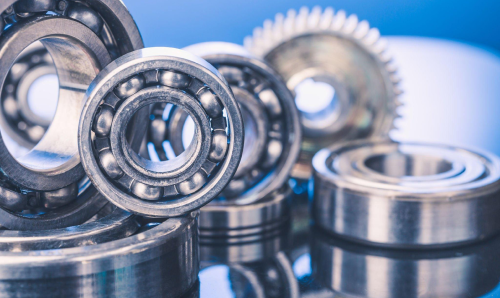
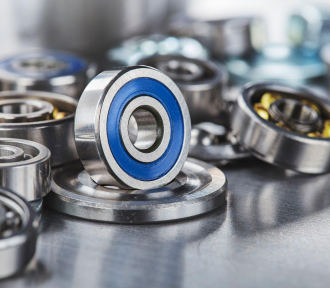
Journal bearings are an essential component of many machines, and their failures can result in various negative consequences, including:
- Increased friction and heat
- Vibration and noise
- Reduced efficiency
- Seizure
- Damage to other components
How Does Journal Bearing Monitoring Work?
Monitoring journal bearings is essential to prevent potential failures that can cause costly downtime and even catastrophic equipment damage. There are several methods used to monitor journal bearings, including:
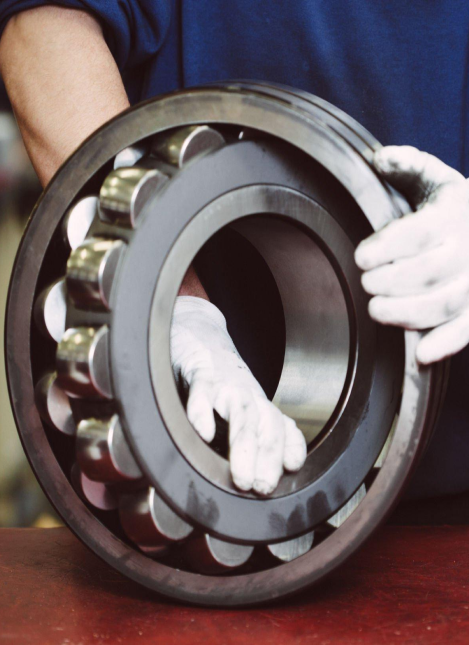
Vibration analysis : This technique involves using sensors to measure vibrations generated by the rotating machinery. Any changes in vibration patterns can indicate bearing wear, misalignment, or other issues.
Oil analysis : This method involves taking samples of lubricating oil used in the machinery and analyzing them for various parameters such as metal particles, viscosity, and acidity. Monitoring the lubricating oil can provide information on the presence of wear particles and other contaminants that can damage journal bearings.
Temperature monitoring : Journal bearings can overheat due to excessive friction caused by wear or lack of lubrication. Temperature sensors can detect abnormal heat buildup in the bearings and alert operators to potential issues.
Acoustic Emission Analysis : Acoustic emission analysis involves using sensors to measure the sound waves generated by the bearings during operation. By analyzing the acoustic emissions, maintenance teams can detect changes in the sound patterns that may indicate bearing wear, damage, or other issues.
By using these monitoring methods, maintenance teams can detect & diagnose potential bearing issues before they cause downtime.
For instance, oil analysis can detect the presence of metal particles that can be a sign of bearing wear, while temperature monitoring can detect abnormalities and alert operators to potential issues, such as lack of lubrication or misalignment.
These methods can provide valuable information about the condition of the bearings, which can help increase the useful life of the equipment.
Continuous monitoring of journal bearing can help maintenance teams identify and address potential problems before they cause equipment damage or unplanned downtime. This helps improve equipment reliability and extends the lifespan of critical components.
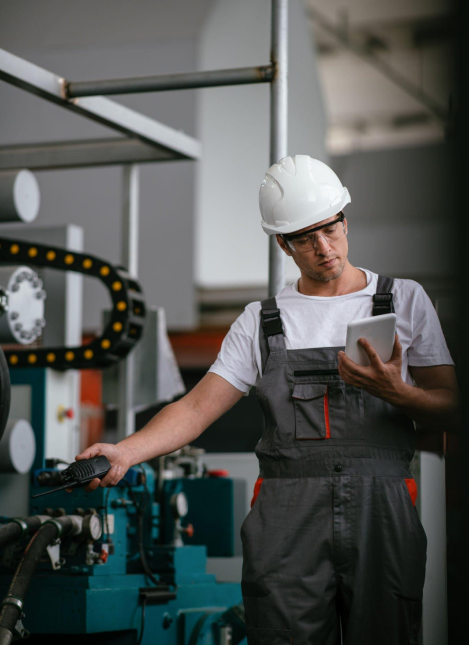
Benefits of Journal Bearing Monitoring

Early detection of potential problems
Journal bearing monitoring allows maintenance teams to detect potential problems with the bearings before they cause damage or failure. For instance, vibration analysis can detect changes in vibration patterns that may indicate misalignment, while oil analysis can detect the presence of metal particles that can be a sign of bearing wear.

Improved equipment reliability
By detecting and addressing potential bearing issues early, journal bearing monitoring can help prevent unexpected equipment downtime, which can be costly and disruptive. This can help improve equipment reliability and reduce maintenance costs.

Extended equipment lifespan
Journal bearing monitoring can help extend the lifespan of critical components, by reducing wear & tear and preventing catastrophic failures.

Cost Savings
Journal bearing monitoring allows maintenance teams to detect potential problems with the bearings before they cause damage or failure. For instance, vibration analysis can detect changes in vibration patterns that may indicate misalignment, while oil analysis can detect the presence of metal particles that can be a sign of bearing wear.

Improved safety
Detecting and addressing potential bearing issues early can help improve safety by reducing the risk of catastrophic equipment failure, which can be dangerous for workers and cause significant damage to equipment and facilities.

Analyzing the data
By using a combination of monitoring methods and regularly analyzing the data, maintenance teams can optimize the performance of rotating machinery and increase its useful life.
Request a Call Back
Frequently Asked Questions
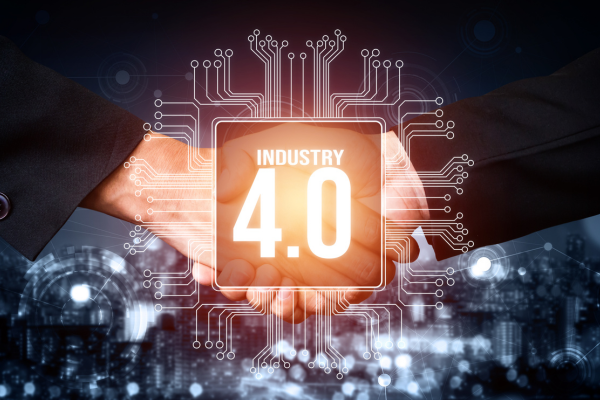
Let us show you how!
Explore the transformative potential of predictive maintenance. At Nanoprecise, we specialize in tailoring predictive maintenance to your unique needs. Reach out today, and together, let’s pave the way for a more efficient, profitable and sustainable future.