Journal Bearing Failure Prevention
Simple Steps to Keep Your Equipment Reliable
Journal bearings are part of almost all rotating machinery, such as engines, turbines, and generators. They support rotating shafts and ensure smooth operation by reducing friction and wear. Monitoring these journal bearings is essential to prevent failures that can cause costly downtime and catastrophic equipment damage. When these bearings fail, the consequences can include unexpected downtime, costly repairs, and even safety hazards. The good news is that knowing the common causes of failure and using the right tools can help you prevent issues and keep operations running smoothly.
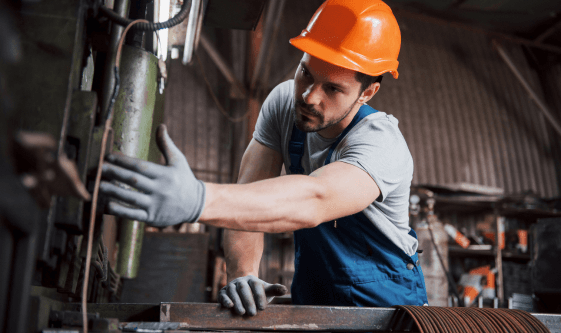
What Causes Bearing Failures in Industrial Equipment?
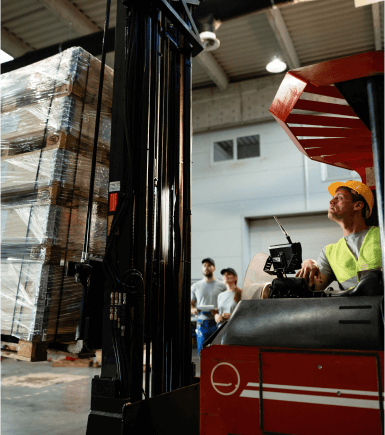
Here are the most common reasons:
Lack of Lubrication:
Insufficient or degraded lubrication increases friction and damages components.
Contamination:
Particles like dirt, water, or debris in the lubricant can harm bearing surfaces.
Misalignment:
Improper alignment during installation puts excessive stress on bearings.
Overloading:
Heavy loads or operational pressures can accelerate wear and tear.
Wear and Tear:
Over time, bearings naturally degrade due to continuous use.
Solution with AI integration and predictive maintenance
Follow these best practices to improve equipment reliability:
Monitor Lubrication Levels:
Keep lubricants clean and at optimal levels to reduce.
Ensure Accurate Installation:
Proper alignment and assembly are crucial for reducing stress on bearings.
Track Operating Conditions:
Monitor temperature, vibration, and loads regularly to catch abnormalities early.
Conduct Periodic Inspections:
Routine checks can identify contamination, wear, or other issues.
Adopt Predictive Maintenance:
Tools like Nanoprecise’s sensors provide real-time data to help you make proactive decisions.
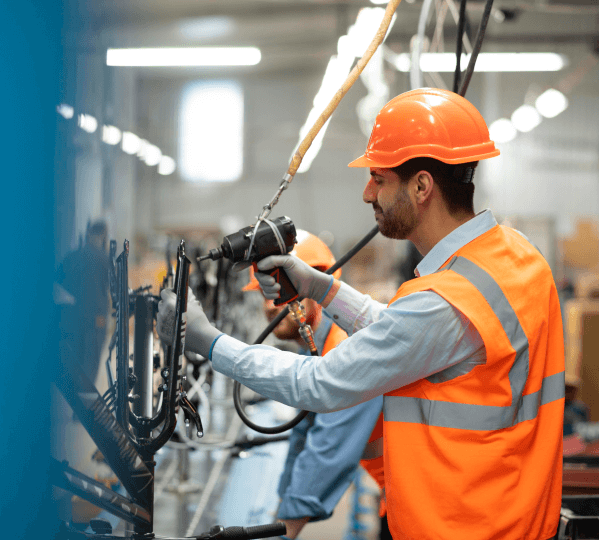
How Nanoprecise Can Help with Equipment Health
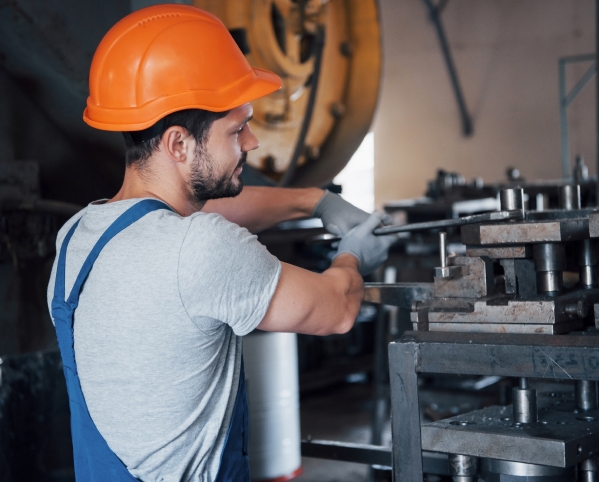
Nanoprecise offers advanced monitoring tools that make maintaining your equipment easier and avoiding unexpected breakdowns. Our technology tracks important parameters like temperature, vibration, acoustics, and Magnetic Flux in real time, so you always know how your machinery is performing or not performing. This AI-powered system identifies potential issues like wear and tear, contamination, or misalignment early on, giving you enough time to fix them before they cause major problems.
Additionally, our system generates detailed reports that give you a clear understanding of how your equipment is performing over time, making it simpler to plan your maintenance schedules.
Nanoprecise helps you avoid downtime, save on repair costs, and keep your operations running smoothly without any interruptions. Our solutions make it easy to maintain your equipment and ensure everything stays in good condition effortlessly.
Ensure Maximum Uptime for Your Journal Bearings
With advanced monitoring solutions, you can prevent journal-bearing failures and enhance the performance of your industrial equipment. Talk to the experts to learn how we can help improve the reliability and longevity of your machinery.
Nanoprecise is the trusted choice for bearing monitoring, offering proven reliability that helps industries worldwide minimize downtime and optimize maintenance schedules. Our advanced AI-driven analytics provide actionable insights tailored to your specific operations, ensuring you can make informed decisions to prevent issues before they occur. With a strong focus on sustainability, our solutions help reduce energy consumption and extend bearing lifespan, supporting your ESG goals. Backed by deep expertise in manufacturing, oil & gas, and power generation industries, Nanoprecise understands the unique challenges you face and is committed to helping you achieve peak performance and reliability.
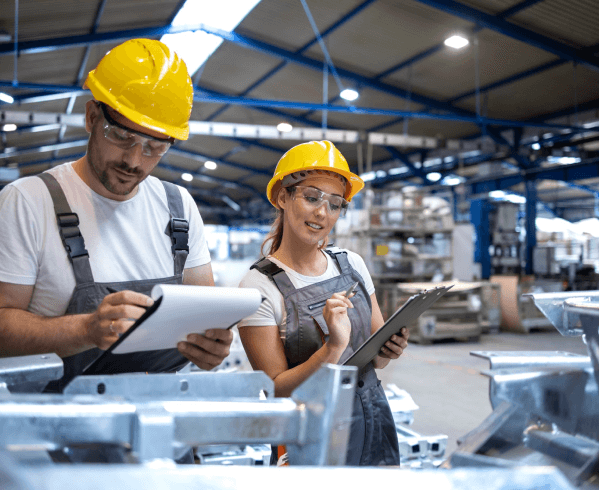
Request a Call Back
Frequently Asked Questions
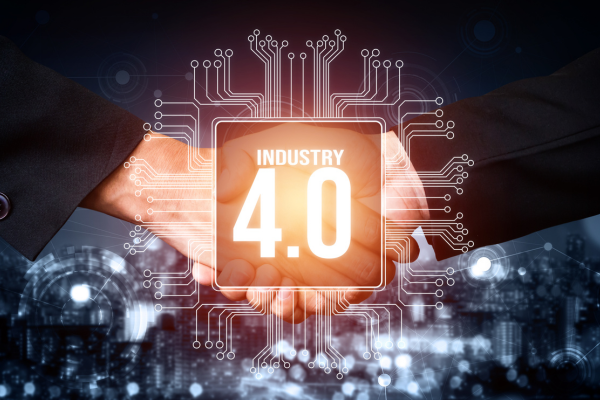
Let us show you how!
Explore the transformative potential of predictive maintenance. At Nanoprecise, we specialize in tailoring predictive maintenance to your unique needs. Reach out today, and together, let’s pave the way for a more efficient, profitable and sustainable future.