Iot Predictive Maintenance
Predictive maintenance with IoT enables strategic allocation of resources to optimize equipment performance throughout the organization. It allows to avoid unwanted pitfalls that causes wastage of time and resources while delivering productive results from the start.
Introduction
Across the world, manufacturing equipment faces failures and downtime, while in different environments, due to the nature of repetitive tasks being performed by them. However, with a higher demand for efficiency and quality in production & manufacturing, these unplanned downtime causes delays and customer-loss, thereby hitting the bottom-line of the organization. Therefore, it is essential to limit the possibility of unplanned downtime as much as possible, to improve the bottom-line and gain competitive advantage.
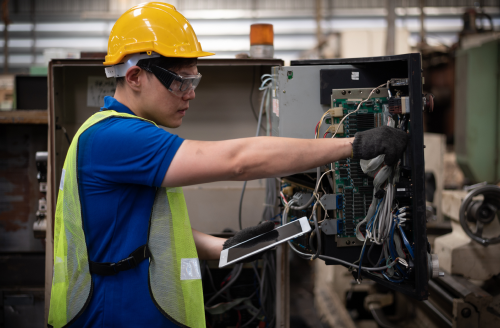
What is Predictive Maintenance with IoT?
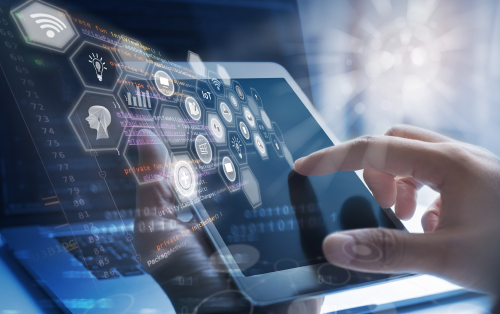
Industrial Internet of Things (IoT), also known as IIoT, is the use of the Internet of Things (IoT) in the manufacturing/industrial sector. It constitutes the use of Wireless Industrial IoT sensors & applications, to connect machines and equipment sets, in order to facilitate machine-to-machine communication that improves the efficiency of overall manufacturing processes.
Predictive maintenance with IoT refers to the use of a data-driven approach, that analyses the equipment condition to predict when that equipment requires maintenance. It is a technique that can significantly improve the performance and lifetime of assets.
Predictive maintenance is a multi-step process that helps maintenance & reliability professionals monitor the equipment health to prevent failures and unplanned downtime. It uses data from sensors and predictive algorithms to estimate the correct time of equipment failure and schedule maintenance activities accordingly. It identifies the root cause of issues in complex machinery and the parts that need replacement. Predictive maintenance process generally involves:
- Remote Condition Monitoring of equipment to collect real-time performance data.
- Gaining actionable insights from the analysis of complex machine condition data.
- Taking remedial measures based on the insights obtained, to maximize the asset uptime.
Technologies that drive Predictive Maintenance
At a macro level, Predictive Maintenance with IoT uses advanced technologies such as Smart Sensors, Internet of Things, Big Data, Machine Learning, Cloud Computing, Edge Computing and Wireless Communication Networks. Engineers and Professionals bring these technologies together to build a robust Predictive Maintenance Solution. Predictive maintenance technology is based on a simple architecture as mentioned below:

Wireless Industrial IoT Sensors are installed in the proximity of an asset / machine, which then captures various output parameters (such as vibration, temperature, sound etc.) of these machines, and converts it into signals.

These signals are transmitted via wireless networks to the servers located either on cloud or on-premise. Generally, these signals are transmitted to the server using gateways. However, newer advancements have paved the way for smart sensors that can transmit signals without the need for a gateway. These sensors work on Cellular or LoRa networks, thereby eliminating the hassle of complex wiring and multiple components.

Once the signals are received by the server, machine learning algorithms filter & analyse it to provide meaningful insights about the health and performance of the machines.
Important Steps for implementing Predictive Maintenance with IoT
Following are some important steps for implementing a robust Predictive Maintenance solution:
- Establishing a clear plan to start small implementation programs
- Choosing the right assets
- Choosing the right condition monitoring methods to monitor patterns in real-time
- Establishing a holistic Data Collection & Analysis mechanism
- Pilot Testing of the solution
- Deciding on an appropriate response procedure
- Building a clear data analysis strategy
- Establishing a continuous improvement process for implementation at scale.
These practices should assist maintenance & reliability professionals to deal with issues and extract value from full scale implementation of predictive maintenance.
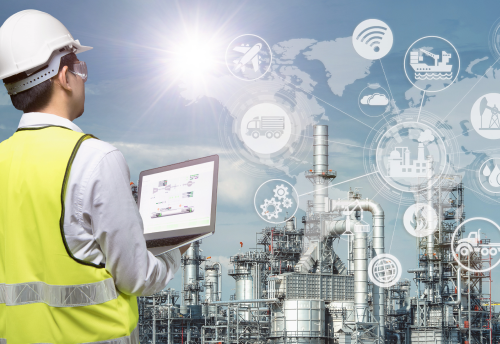
Conclusion
Industrial IoT Predictive Maintenance has the potential to offer significant competitive advantage to organizations, which is an essential component for continued success in an ever-changing business environment. Ultimately, Predictive Maintenance with Industrial IoT opens a brave new world for manufacturers aiming to reduce downtime, increase productivity, improve worker safety and lower costs.
Nanoprecise is an Industrial IoT Predictive Maintenance solution provider that offers real-time predictive information about the genuine health and performance of industrial assets. Nanoprecise offers IoT Solutions for Industrial Manufacturing with our unique 6-in-1 Wireless Industrial IoT Sensor and patented AI-based analytics platform. The Industrial IoT Predictive Maintenance Solutions from Nanoprecise uses a combination of AI + IoT + LTE-driven seamless monitoring, to offer prescriptive diagnostics. Nanoprecise specializes in scaling Industrial IoT across various sectors to empower maintenance and reliability professionals with the right data at the right time.
Request a Call Back
Frequently Asked Questions
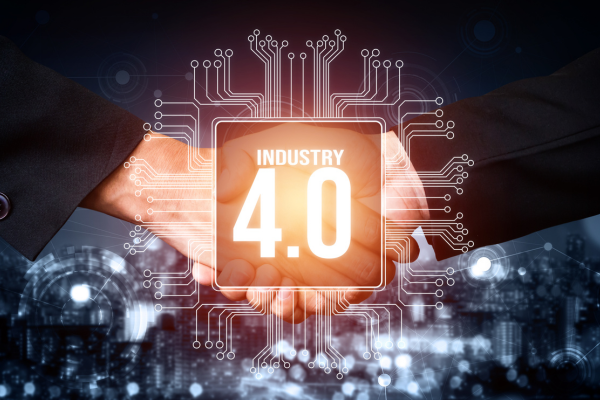
Let us show you how!
Explore the transformative potential of predictive maintenance. At Nanoprecise, we specialize in tailoring predictive maintenance to your unique needs. Reach out today, and together, let’s pave the way for a more efficient, profitable and sustainable future.