Efficiency Monitoring Analytics
Best Practices for Industrial Energy Efficiency Management
Energy efficiency monitoring at manufacturing plants is essential in today’s world, where energy is a vital yet limited resource. Sensible consumption and regulation are crucial to ensuring sustainability and operational efficiency. By leveraging the right Energy efficiency management tools and technologies, manufacturers can avoid energy waste while cutting costs, improving operational efficiency, and reducing environmental impact.
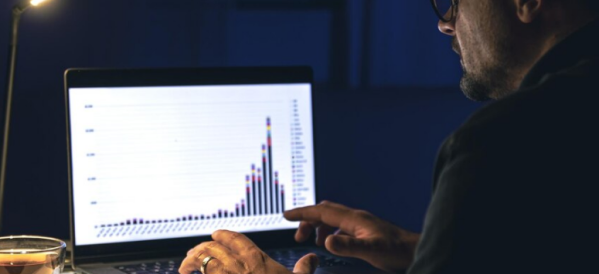
Benefits of Energy Efficiency Management in Industries

Ensure Cost Reduction by lowering energy expenses –
Free up cost resources for other
essential activities.

Contribution to Net Zero and Sustainability Goals by
Supporting global environmental targets and
sustainable practices.

Prevent potential fines and legal issues
by adhering to Regulatory
Compliance.

Demonstrates a commitment to sustainability,
enhancing the company’s image and attracting
eco-conscious consumers and investors.

Directly contribute to CO2 emissions reduction.
Typical Industrial Equipment and Faults Requiring Energy Efficiency Monitoring
Motors often face issues such as imbalance, misalignment, bearing problems, rotor bar defects, winding issues, and phase-related problems, all of which can impact energy efficiency.
Fans may experience unbalance, misalignment, bearing issues, impeller-related problems, or looseness, which can affect their operational efficiency.
Pumps are prone to unbalance, misalignment, cavitation, blade or vane failure, and flow-related issues, hindering their performance and energy use.
Compressors can suffer from unbalance, misalignment, bearing problems, screw mesh issues, lobe mesh problems, and looseness, leading to inefficiencies.
Gearboxes may encounter unbalance, misalignment, bearing problems, and gear defects, affecting their energy efficiency and performance.
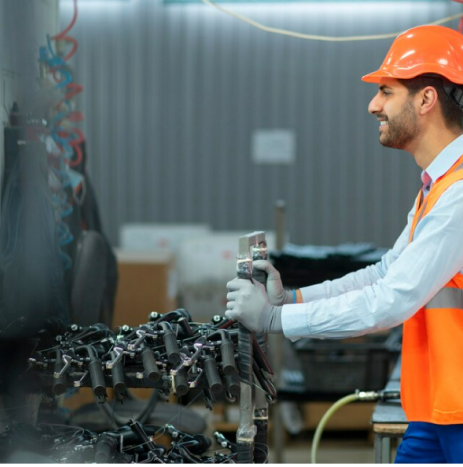
How Nanoprecise NrgMonitor is Revolutionizing Industrial Power Use
Given the importance of reducing power consumption, integrating effective digitization into your industrial ecosystem is crucial. This is where NrgMonitor, from Nanoprecise, comes into play. Designed to help plants manage and monitor their energy consumption, NrgMonitor offers real-time energy efficiency monitoring and analytics.
These real-time data insights enable immediate identification and rectification of inefficiencies, faults, and defects. Its comprehensive analytics dashboard makes it easy to spot areas of excessive energy use, allowing for strategic improvements based on insights from our reliability engineers. With predictive maintenance at its core, NrgMonitor forecasts potential operational issues before they escalate, enhancing equipment efficiency and minimizing energy waste.
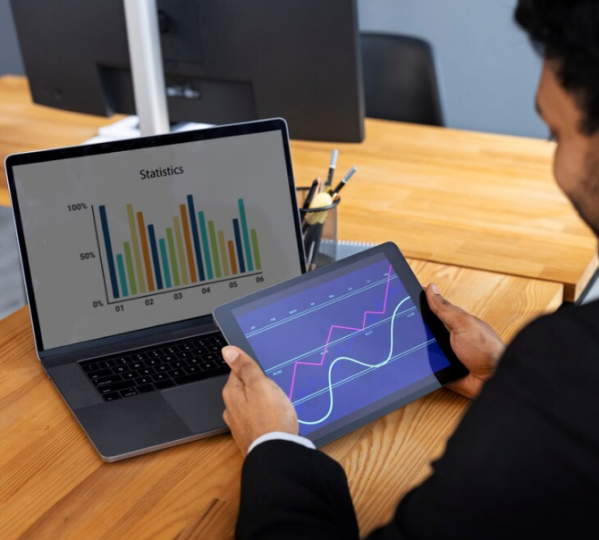
Areas Enhanced by Nanoprecise NrgMonitor in Energy Efficiency Management
1. Anomaly Detection – Identify unusual patterns and deviations in energy usage
2. Fault Mode Identification – Pinpoint specific faults affecting equipment performance
3. Remaining Useful Life Prediction – Forecast the remaining lifespan of equipment to optimize maintenance schedules
4. Outcome Feedback Assistance – Provide actionable insights and feedback on efficiency improvements
5. Emissions Reduction – Quantify and avoid unnecessary emissions
6. ROI-Based Money-Back Guarantee – Ensure value with a guarantee based on return on investment
Request a Call Back
Frequently Asked Questions
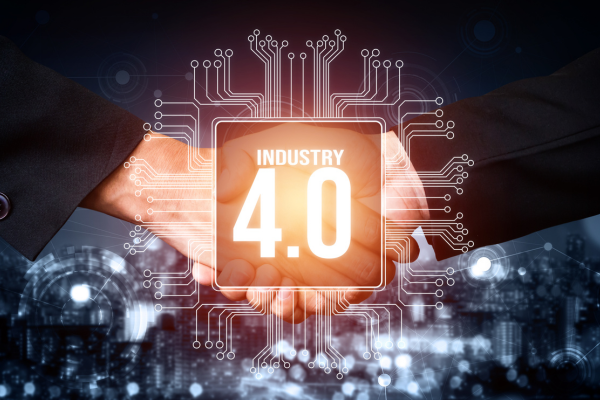
Let us show you how!
Explore the transformative potential of predictive maintenance. At Nanoprecise, we specialize in tailoring predictive maintenance to your unique needs. Reach out today, and together, let’s pave the way for a more efficient, profitable and sustainable future.