“Machines rarely fail due to a change in just one isolated parameter. So why rely on analyzing a single-parameter anomaly in isolation? This is where Condition Intelligence comes in.
Traditional condition monitoring (CM) technologies often treat a singular anomaly as a warning, which can flood maintenance teams with false notifications or worse, cause them to miss early indicators of real failure. Without analyzing multiple parameters together, CM tends to remain inconclusive, leading teams to fall back on reactive maintenance, causing costly unplanned downtime.
Condition Intelligence (CI) bridges the gap between inconclusive notifications and actionable insights. By evaluating multiple interrelated parameters simultaneously, CI identifies meaningful correlations while filtering out irrelevant noise. This enables early, confident detection of potential failures, guiding maintenance teams from data collection to intelligent, predictive decision-making.“
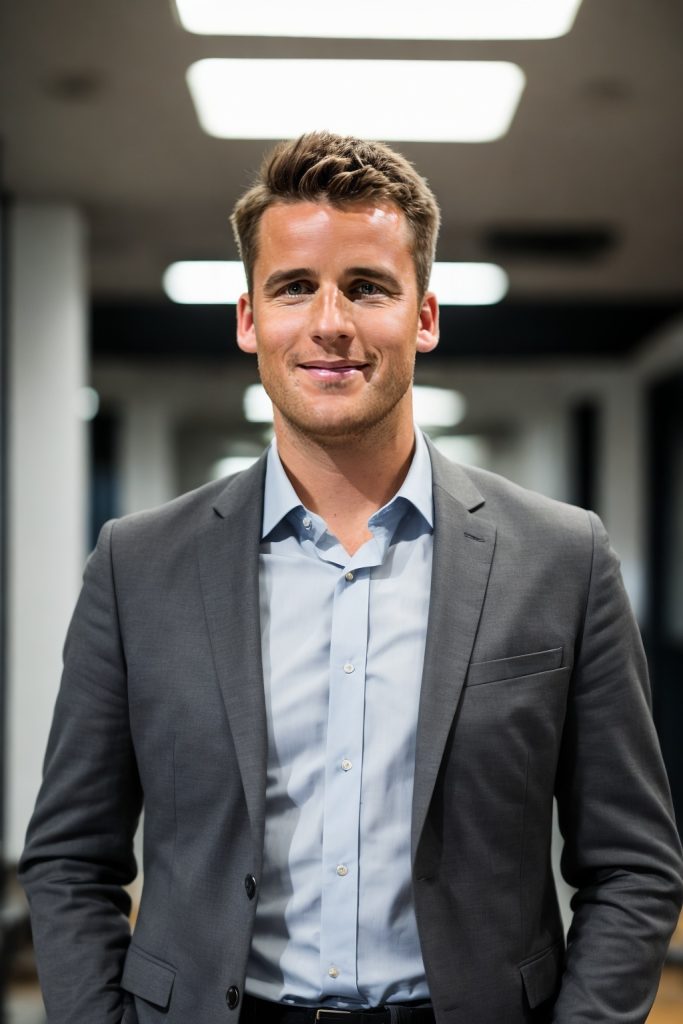
VP – Product, Nanoprecise
As a CAT IV Vibration Analyst myself, for years, I’ve championed predictive maintenance as the ultimate solution to unplanned downtime, rising maintenance costs, and inefficient operations. If we could just collect the right data and analyze it correctly, predicting failures before they occur would finally become possible. We’d minimize downtime, reduce expenses, and optimize industrial efficiency.
Yet for many maintenance teams, the reality tells a different story..
Despite the promises of predictive maintenance, most teams are still overwhelmed by false alarms and distracted by irrelevant data, causing them to miss critical failures. The fundamental problem? Traditional predictive maintenance relies heavily on basic thresholds and simple statistical models, typically applied to one or two isolated parameters. These simplistic methods fail to reflect the complex reality of industrial equipment operations.
The real challenge isn’t merely flagging changes in equipment conditions, it’s understanding which changes truly matter and then acting swiftly on those insights. That’s why Nanoprecise heavily invests in innovating technologies like Condition Intelligence.
The Traditional Condition Monitoring Approach
Condition Monitoring, integrated with predictive maintenance strategies, has notably improved asset reliability by reducing unplanned downtime, particularly for critical equipment. However, traditional CM approaches could significantly benefit from technological advancements to effectively scale these reliability improvements without requiring disproportionate resources or increasing reliance on specialized expertise.
Most traditional CM solutions are based on threshold monitoring. Notifications are triggered when specific parameters such as vibration (RMS, Peak, Velocity, Acceleration), temperature, or sound exceed predefined limits. While thresholding can be effective for certain failure modes, it assumes that crossing a single value is a clear indicator of risk. Equipment failures often involve complex, multi-parameter interactions that single-threshold methods struggle to detect with high confidence.
For instance, an isolated spike in vibration might simply result from a temporary load fluctuation, not necessarily indicating imminent equipment failure. Yet, traditional CM treats these deviations as equally significant, resulting in potentially unnecessary notifications and added workload for maintenance teams.
Key areas where traditional CM approaches can benefit from advancements include:
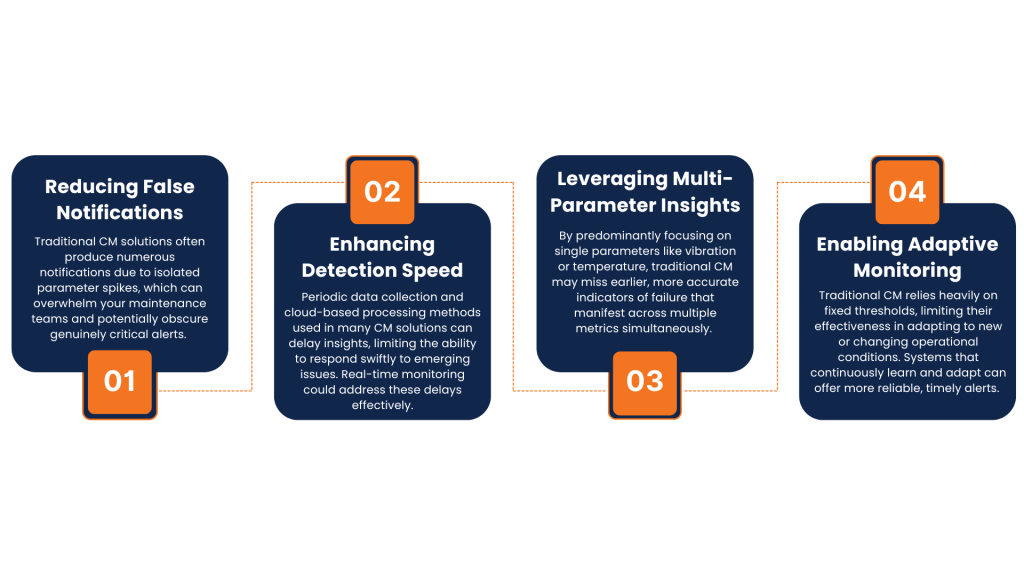
The Opportunity for Innovation
Embracing technological innovations like CI can significantly enhance traditional CM approaches. CI employs advanced analytics, multi-parameter monitoring, adaptive algorithms, and real-time insights, transforming predictive maintenance into a truly proactive and intelligence-driven strategy.
Moreover, advanced approaches must also prioritize data privacy, secure data handling, anonymization, and effective data curation, ensuring the integrity and usability of maintenance data for improved decision-making.
Condition Intelligence represents an essential evolution, enabling maintenance teams to transition from data collection to actionable intelligence effectively and confidently.
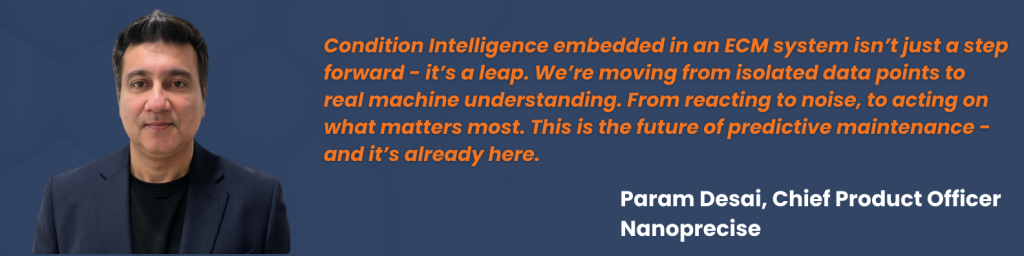
Machine behavior is rarely defined by a single data point
The illustration below shows how Condition Intelligence leverages multivariate analysis and Principal Component Analysis (PCA) to detect subtle but significant changes in machine condition over time.
Rather than watching individual parameters in isolation, CI understands how they behave in combination. The chart visualizes how seemingly small variations across multiple signals may still fall within acceptable thresholds individually but together, they shift the machine’s overall operating profile into a new region.
Condition Intelligence recognizes these deviations early tracking them in the latent space so teams can take informed action before failure modes develop. This is the foundation of how CI enables smarter, faster, and more confident decision-making.
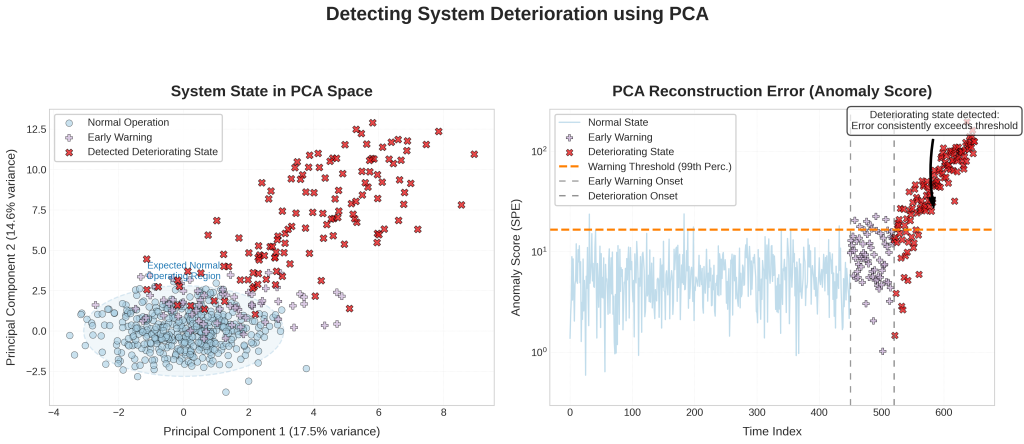
How Condition Intelligence Works: Smarter, Faster, and More Reliable
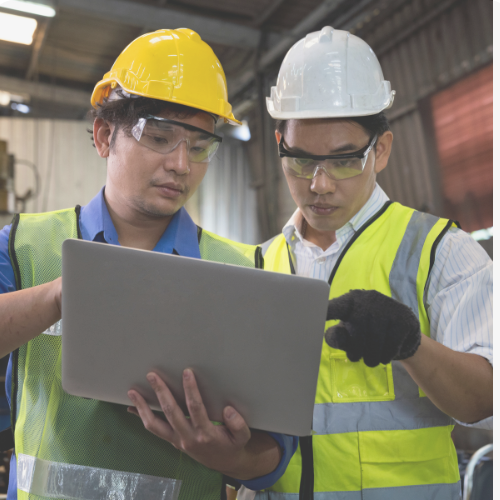
- Multivariate Intelligence: Seeing the Full Picture, Not Just One Variable
Traditional systems monitor one variable such as vibration or temperature and react when a threshold is crossed. However, failures typically emerge from complex interactions among multiple parameters.
CI addresses this by applying:
- Multivariate Analysis: CI analyzes more than 18 vibration-related parameters, including RMS, kurtosis, and peak values, to detect complex patterns that precede failure.
- Dimensionality Reduction with PCA: Principal Component Analysis (PCA) is used to identify latent patterns in high-dimensional data. This enables the system to capture machine behavior holistically and flag subtle deviations in the latent space.
- Correlation-Based Diagnostics: CI examines how features interact with each other. For example, a small increase in peak acceleration may be insignificant on its own, but when combined with shifts in velocity RMS and kurtosis, it can signal early-stage degradation.
Why It Matters
- Recognizes failure patterns rather than reacting to individual thresholds.
- Reduces false positives by understanding feature relationships.
- Produces high-confidence, statistically grounded notifications that improve response accuracy.
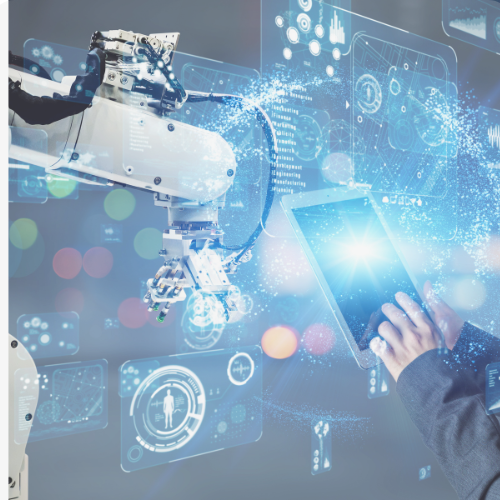
2. Adaptive Learning: Statistical Models That Evolve with Machines
Rigid threshold-based systems do not adapt to changes in machine usage or operating conditions. CI offers continuous learning and refinement through:
- Time Series Learning: CI builds and updates a reference baseline by analyzing operational behavior over sliding windows such as two weeks, one month, or three months.
- Baseline Drift Detection: Each new data point is scored against the PCA reference model using Root Mean Squared Log Error (RMSLE) to detect meaningful deviations over time.
- Model Evolution: As operations evolve due to factors like seasonal changes or load variations, CI can be retrained manually or automatically to ensure alerts remain relevant and reliable.
Why It Matters
- Adapts to changing environments and avoids irrelevant alerts.
- Tracks long-term degradation trends for better planning.
- Builds trust with operators through consistent and useful insights.
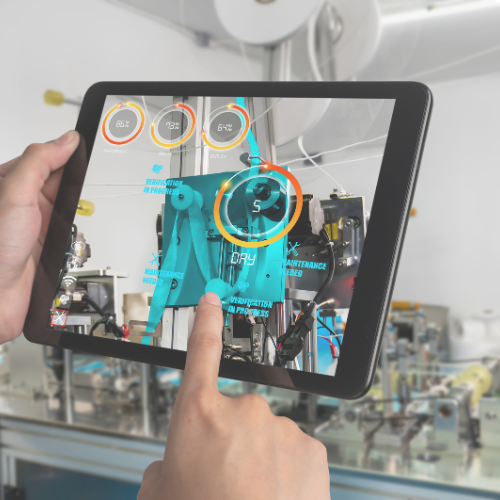
3. Edge Intelligence: Insights Without Cloud Lag
In time-critical industries, latency can lead to delayed responses and costly downtime. CI ensures timely detection by embedding intelligence at the point of data collection.
- Edge ML Inference: Models run directly on our powerful MachineDoctor sensor, enabling alerting without relying on cloud processing.
- Battery Optimization: By avoiding transmission of redundant or identical data, CI conserves bandwidth and significantly extends battery life.
- Immediate Actionability: Data is processed on the sensor, allowing condition changes to be detected within minutes instead of hours.
Why It Matters
- Enables rapid response to emerging equipment issues.
- Reduces data transmission costs and power consumption.
- Supports remote operations through local processing and efficient communication
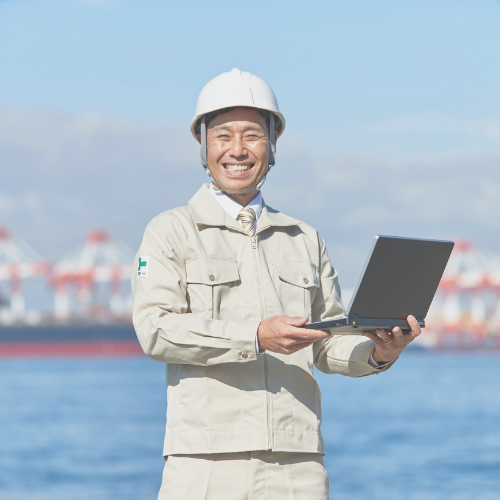
4. Intelligent Notifications: Only What Matters, When It Matters
One of the most common complaints in traditional systems is excessive notifications with little actionable value. CI focuses on delivering relevant and timely alerts through:
- Smart Scoring System: Condition changes are tracked over time and scored on priority in the backend, ensuring that only persistent or escalating anomalies trigger notifications.
- Pattern Classification: Events are labeled based on the dominant direction of deviation, such as simultaneous changes in Acceleration RMS and Velocity RMS.
- Contextual Delivery: Notifications are sent via dashboard, email, SMS, or integrated CMMS platforms, ensuring that maintenance teams receive alerts where and when they are most useful.
Why It Matters
- Prevents notification fatigue by filtering out noise.
- Provides actionable context rather than raw signals.
- Helps teams prioritize actions and avoid unnecessary downtime
What’s Next: From Anomaly Detection to Equipment Health States
Condition Intelligence is evolving beyond anomaly detection. It is laying the groundwork for full Equipment Health States, where the focus shifts from isolated incidents to a comprehensive understanding of machine condition. By combining PCA-based diagnostics, trend scoring, re-baselining capabilities, and future support for additional parameters such as temperature and acoustics, CI is moving toward real-time classification and prediction of machine health. This approach empowers maintenance teams not just to react, but to anticipate and plan, transforming reliability into a proactive discipline.
Why Maintenance Teams Are Rewriting Their Playbook with Condition Intelligence
Condition Intelligence is not just about better detection. It’s about creating a system that understands how machines behave, how teams work, and how knowledge is built over time. In the field, data rarely lives in isolation. Technicians often spot early signs, like a motor running hotter post-alignment or increased vibration following maintenance. CI enables these moments to be logged, tracked, and understood in real-time. Combined with historical trends and sensor analytics, this creates a continuous loop between people, machines, and systems.
In recent deployments, teams using CI-based anomaly detection saw a 55x reduction in irrelevant alerts compared to older threshold-based models. But more importantly, they gained something harder to measure – trust in the system.
Here’s what that looks like in practice:
Fewer silos. More collaboration.
CI connects field teams, planners, and systems through a shared understanding of machine health.
Technician input becomes intelligence.
Field observations directly inform the model enhancing future detection.
Built-in memory.
CI remembers what changed, when, and why across machines, sites, and time.
From reacting to planning.
Data Insights and trend scoring help teams prioritize proactively, not just respond.
Adapts as you evolve.
CI re-baselines with changing operations, load shifts, and seasonal variation.
Smarter system. Stronger strategy.
CI is the foundation for connected, contextual, and strategic maintenance.
What an Energy-Centered Predictive Maintenance System Should Look Like
Predictive maintenance is evolving. Today, it’s not just about avoiding downtime, it’s about improving energy efficiency, lowering carbon impact, and extending asset life, without compromising reliability. That’s the core of Energy-Centered Maintenance (ECM).
A true ECM-ready solution doesn’t just detect faults. It identifies energy waste, reveals inefficiencies early, and guides corrective action at scale.
Here’s what that looks like:
With MachineDoctor capturing granular machine behavior, Condition Intelligence delivering precise diagnostics, and RotationLF exposing hidden mechanical inefficiencies, Nanoprecise provides more than condition monitoring, it delivers actionable, energy-aligned insights.
This is what Energy-Centered Predictive Maintenance looks like.
Smarter. Cleaner. Ready to scale.
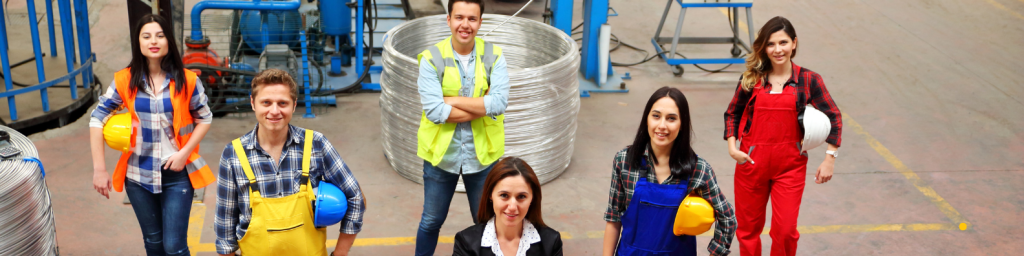
To Summarize
Condition Intelligence is a fundamental shift in how we understand machines behavior, communicate, and respond to operational risks. By moving from static predictions to dynamic, real-time intelligence, organizations can:
- Reduce unplanned downtime.
- Eliminate false alarms.
- Improve maintenance efficiency.
The question is no longer – “when will machines fail?” The question is: Are you ready to act before failure even begins?
Book a Demo with our team to experience the power of ECM with Condition Intelligence.
About the Author
Dries Van Loon, VP Product
Dries Van Loon isn’t just another product leader – he’s spent his career deep in the world of industrial reliability, where the difference between noise and intelligence can make or break operations. With over 15 years of experience in predictive maintenance, vibration analysis, and condition monitoring, Dries has worked with some of the most complex industrial systems across the globe. From leading online condition monitoring projects at Fluke Reliability to helping companies implement AI-driven predictive maintenance strategies, he knows firsthand where traditional PdM solutions fall short – and what it takes to fix them. At Nanoprecise, he drives innovation by ensuring that predictive maintenance doesn’t just predict – it understands. With a background in industrial and electromechanical engineering and certifications including CAT IV Vibration Analyst and Certified Reliability Leader, Dries is dedicated to helping industries transition from reactive maintenance to true operational intelligence.
Because for him, maintenance isn’t just about preventing failure – it’s about making sure companies can trust every decision they make.