Predictive Maintenance in Steel Plant
Steel Industry
Steel is an important economic component that has an impact on everyone’s daily lives. Steel is essential to every major industry, from blade manufacture to railways and airplanes. Without steel production, the economy would struggle to survive.
Steel production and supply are heavily influenced by the speed of production and demand. Unplanned downtime is expensive in any sector, but it’s especially costly for a company in the metal industry. When a steel mill shuts down, it loses a significant amount of metal production as well as a significant amount of money. This in turn affects the growth of other industries which are dependent on steel plants for raw materials.
Steel plants feature unique machinery, settings, and layouts that necessitate entirely different maintenance methods and procedures than other industries. As a result, each manufacturing location often has its own maintenance plan that is adapted to its own needs.
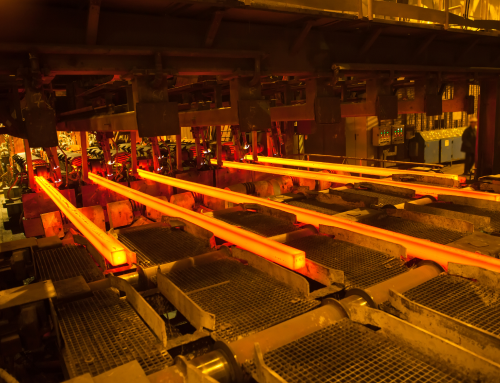
Why predictive maintenance?
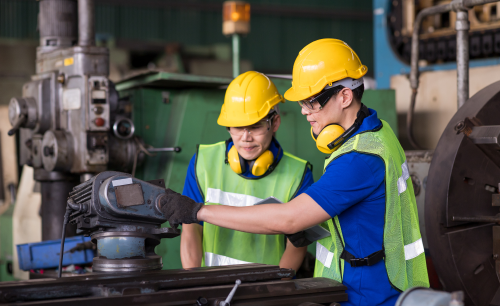
The importance of preventative maintenance in ensuring the efficient functioning of plants cannot be overstated. Periodic inspection of machinery to ensure proper operation is a standard preventative strategy. This keeps machinery from breaking down and helps to anticipate an issue that could cost the company money.
When compared to modern maintenance procedures, time-based maintenance approaches in steel and metal industries increase operator risk while also raising expenses. To boost operational efficiency, therefore, predictive maintenance is the key.
Predictive maintenance solution assists steel plants to avoid unplanned downtime by predicting defects months ahead of time. Asset availability and output is maximized while maintenance expenses are reduced. It also helps to avoid unplanned downtime as well as the increasing expenses associated with preventative maintenance regimes. It provides a increased transparency to the overall manufacturing operations, with improved worker safety and enhanced operational efficiency.
Why choose Nanoprecise?
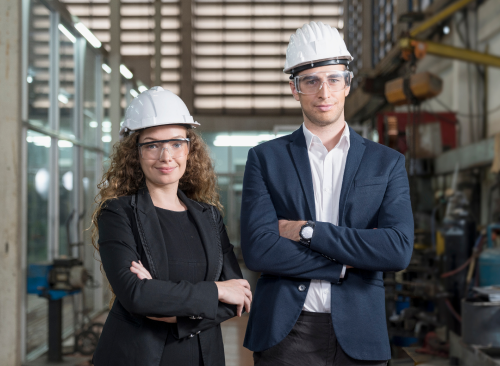
Nanoprecise specializes in the delivery of comprehensive, cloud-based solutions for the lifecycle monitoring of equipment in steel plants. We offer a wide range of solutions to support steel manufacturers at every stage of their operations.
Nanoprecise has been making a significant contribution towards the implementation of AI based predictive maintenance in steel plants. We have been working with customers in the steel manufacturing for many years.
We excel in the implementation of AI-based predictive maintenance in steel plants, to drive the digital transformation of steel manufacturers. We enable manufacturers to start their Industry 4.0 journey with a relatively small budget focussed on key goals, while laying the foundation for IoT implementation at scale.
Our predictive maintenance solutions make use of the Artificial Intelligence/Machine Learning (AI/ML) model to provide asset health monitoring, real-time as well as historical data on the health and performance of machines and equipment sets. The state-of-the-art AI based Predictive Maintenance from Nanoprecise detects looseness in machines, as well as misalignment, and unbalance among other faults in real-time. Our AI-based solution is a powerful tool that helps to reduce maintenance spending and increase the mean time between repairs by proactively identifying detrimental system conditions prior to catastrophic machine failure. Our cloud-based analytics platform employs a dashboard that displays waveforms to assist you to assess the overall equipment efficiency of assets. This avoids unnecessary downtime, and lowers inventory costs dramatically.
We help steel manufacturing companies to reduce downtime & costs, increase availability & productivity, protect employees, and improve operational efficiency.
What makes us unique?
- We are not simply data science specialists. What makes us different is that we adopt an industrial approach to establishing strong, analytical processes and automating them so that fully operational solutions may be deployed.
- We use a methodology that supports all stages of the project, from early needs to operational deployment, with a focus on integrating business expertise.
- We collaborate with customers and partners to develop and deliver solutions, leaving them equipped and capable of supporting and further developing them. Our vision and mission are to ensure that our services and processes add value to our partners’ projects and operations, thereby providing them with a competitive advantage in their respective sector.
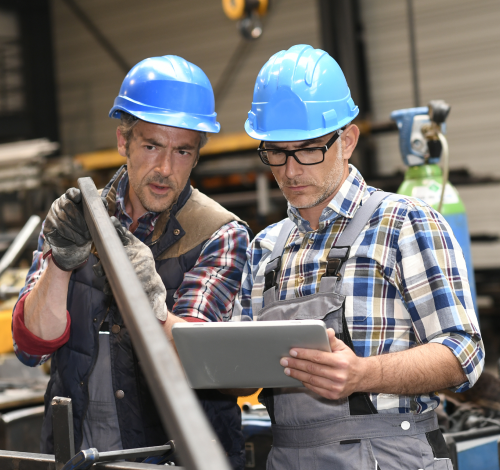
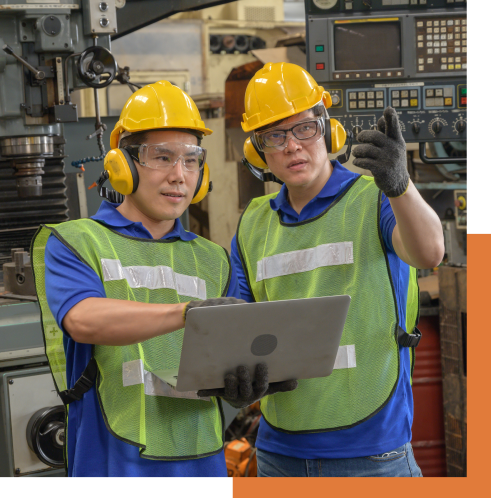
What makes us unique?
Automated AI based Predictive Maintenance Solutions from Nanoprecise uses a combination of AI + IoT + LTE-driven seamless monitoring, advanced sensors, and prescriptive diagnostics to achieve productive results from day one. We use cutting-edge, scalable technology to monitor equipment health and reduce unnecessary downtime, which costs the global economy roughly $100 billion each year. It’s time for you to save money and level up your steel plant operations.
Request a Call Back
Frequently Asked Questions
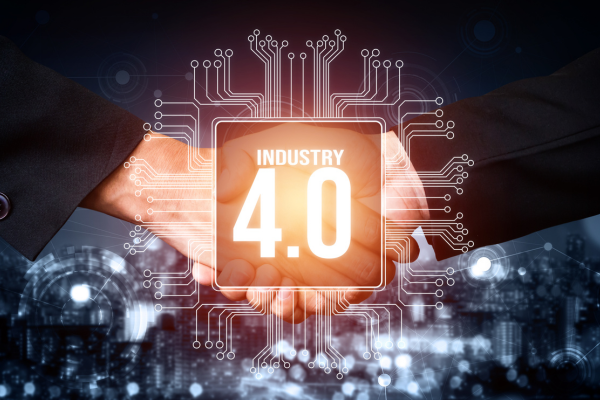
Let us show you how!
Explore the transformative potential of predictive maintenance. At Nanoprecise, we specialize in tailoring predictive maintenance to your unique needs. Reach out today, and together, let’s pave the way for a more efficient, profitable and sustainable future.