Iot Solutions for Industrial Manufacturing
The Internet of Things (IoT) is transforming industrial manufacturing in many ways. It is revolutionizing the industrial sector by seamlessly integrating smart sensors and applications. Byconnecting industrial equipment and machines, IoT Solutions for Industrial Manufacturing facilitate efficient machine-to-machine communication, ultimately enhancing operational efficiency. IoT can help manufacturers improve efficiency, productivity, and quality by connecting machines, devices, and people. IoT solutions for industrial manufacturing can help manufacturers save time and money, improve safety, and increase production.
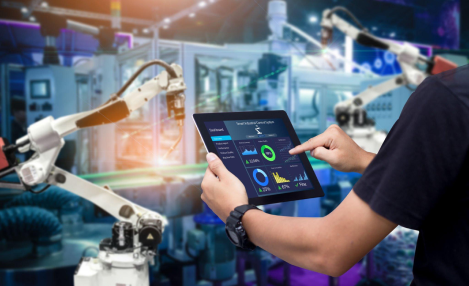
Condition Monitoring Services

Asset Tracking:
IoT can be used to track the location and status of assets, such as equipment, inventory, and materials. This information can be used to improve asset management and reduce downtime.

Predictive Maintenance:
IoT can be used to collect data from machines and devices to identify potential problems before they cause downtime or damage. This can help manufacturers to improve asset reliability and reduce maintenance costs.

Quality Control:
IoT can be used to collect data from production processes to monitor quality. This data can be used to identify and correct problems before they cause defects.

Supply Chain Management:
IoT can be used to track the movement of goods and materials through the supply chain. This information can be used to improve efficiency and reduce costs

Remote Monitoring:
Detecting and addressing potential bearing issues early can help improve safety by reducing the risk of catastrophic equipment failure, which can be dangerous for workers and cause significant damage to equipment and facilities.
These are just a few examples of the diverse IoT solutions available in industrial manufacturing, all aimed at streamlining operations, reducing costs, and improving overall efficiency.
Benefits of IoT Solutions for Industrial Manufacturing
The benefits of IoT Solutions for industrial manufacturing are numerous.
Some of the most common benefits include:

Improved efficiency
IoT can help manufacturers to improve efficiency by automating tasks, reducing waste, and improving communication. For example, IoT-connected machines can automatically order replacement parts when they are running low, which can help to reduce downtime. IoT can also be used to track the movement of goods and materials through the supply chain, which can help to improve efficiency and reduce costs.

Increased productivity
IoT can help manufacturers to increase productivity by improving quality, reducing downtime, and increasing output. For example, IoT-connected machines can be used to monitor quality in real-time, which can help to identify and correct problems before they cause defects. IoT can also be used to schedule maintenance tasks in advance, which can help to reduce downtime.

Enhanced quality
IoT can help manufacturers to enhance quality by improving traceability, identifying defects, and reducing variability. For example, IoT-connected machines can track the location of every part of a product, which can help to identify and correct problems before they cause defects. IoT can also be used to collect data on the performance of machines, which can be used to identify and correct problems before they cause variability.

Reduced costs
IoT can help manufacturers to reduce costs by improving efficiency, productivity, and quality. For example, IoT-connected machines can automatically order replacement parts when they are running low, which can help to reduce downtime. IoT can also be used to track the movement of goods and materials through the supply chain, which can help to improve efficiency and reduce costs.

Improved decision-making
IoT can help manufacturers to improve decision-making by providing real-time data and insights. For example, IoT-connected machines can collect data on the performance of machines, which can be used to identify and correct problems before they cause downtime. IoT can also be used to track the movement of goods and materials through the supply chain, which can help manufacturers to make better decisions about inventory and production.
Key Aspects to Look For
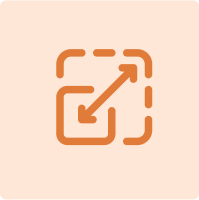
Scalability
As a manufacturing operation grows, it is important to have an IoT solution that can scale with it. This means that the solution should be able to handle the increased volume of data and the increased number of connected devices.
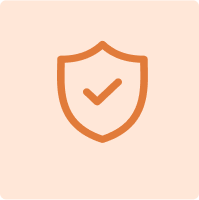
Security
Sensitive data, such as production data and customer information, is often stored in manufacturing operations. It is important to have an IoT solution that is secure to protect this data from unauthorized access.
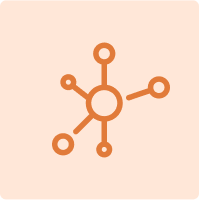
Interoperability
Many manufacturing operations already have a variety of systems in place. It is important to have an IoT solution that is interoperable with these existing systems to avoid the need for costly integration.
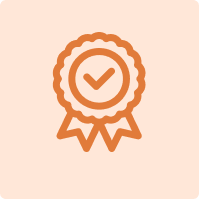
Reliability
An IoT solution must be reliable to ensure that it is always available when needed. This is especially important for solutions that are used to monitor critical equipment or processes.
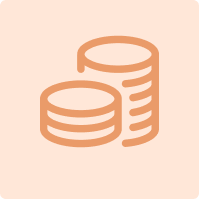
Cost-effectiveness
The cost of implementing an IoT solution must be justified by the benefits that it provides. It is important to select a solution that is cost-effective and that will provide a return on investment.
IIoT represents a veritable treasure trove for the manufacturing industry, offering immense potential for optimizing processes and bolstering financial gains. Undoubtedly, IoT is a powerful tool that can help manufacturers improve their operations.
How Can we help?
As a leading provider of predictive maintenance solutions, Nanoprecise Sci Corp specializes in the deployment of Artificial Intelligence and IoT technology for predictive asset maintenance and reducing the carbon footprint of manufacturing plants. We help our global customers monitor and analyze the health & performance of all types of industrial machines with IoT solutions that seamlessly integrate with the manufacturing processes, to drive their Industry 4.0 journey. The predictive maintenance solutions from Nanoprecise are deployed at scale across a range of industries to provide a cost-effective means for every company to achieve greater sustainability and have a positive impact on reducing energy consumption & costs. We prioritize scalability, stability, and uncompromising security, ensuring that our offerings are tailored to meet your specific requirements. The ease and speed of implementation provide companies with a clear means to start addressing these larger challenges today. Trust us to provide you with the cutting-edge IoT manufacturing solutions you need to drive success in your industry.
Request a Call Back
Frequently Asked Questions
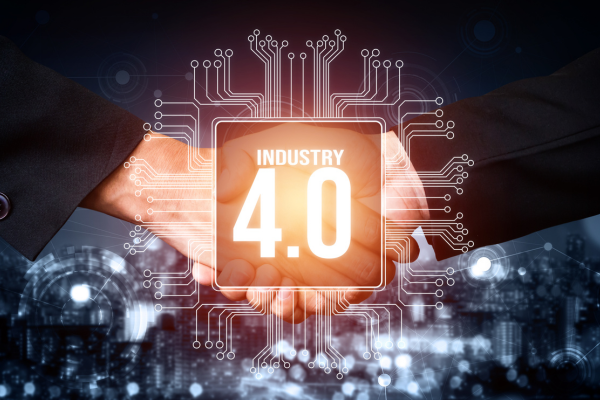
Let us show you how!
Explore the transformative potential of predictive maintenance. At Nanoprecise, we specialize in tailoring predictive maintenance to your unique needs. Reach out today, and together, let’s pave the way for a more efficient, profitable and sustainable future.