Global Predictive Maintenance with Nanoprecise
Analyzing the Surge in the Global Predictive Maintenance Market
With rapid digitalization and the global predictive maintenance (PdM) market projected to exceed $23.5 billion by 2027, it is gaining both visibility and importance across industries worldwide.
Global predictive maintenance has become very important to reduce unnecessary downtime and reduce maintenance costs, while boosting efficiency. Hence, companies in manufacturing, energy, automotive, and other sectors are increasingly adopting advanced global predictive maintenance strategies to remain competitive in a market that prioritizes both innovation and sustainability.
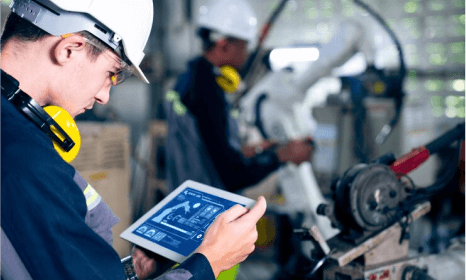
Key Challenges to Eliminate in Maintenance Today with Global Predictive Maintenance Solutions
Maintenance challenges can impact both productivity and profitability of an organization. Hence, understanding these challenges can help to develop strategies, that can improve efficiency and reduce costs.
Unplanned equipment failures are every manufacturing plants worst nightmare since it causes production delays and revenue loss.
Traditional maintenance strategies like reactive or scheduled maintenance often led to inefficient use of resources. With reactive maintenance, repairs only happen after a breakdown occurs while with scheduled maintenance servicing can happen for equipment that doesn’t need it. Hence, both approaches waste time, money, labor, or material unnecessarily.
Frequent outages, inefficient machinery, and energy wastage together add up to higher operational costs. Due to inefficiency of machines energy consumption is usually high, which increases the overall cost of production. Again, frequent repairs or replacements also contribute to higher maintenance expenses making it challenging for companies to maintain healthy profit margins, particularly in industries where operating costs are already high.
At present, companies aren’t just expected to be efficient; they also need to be sustainable. However, meeting environmental, social, and governance (ESG) goals while staying compliant with government regulations on emissions, waste management, and energy usage is not easy. Moreover, few industries are always under pressure to reduce their carbon footprint while maintaining a smooth operation. This adds complexity to maintenance and operational efficiency.
Now, to address these challenges, smarter global predictive maintenance strategies must be embraced.
How Global Predictive Maintenance Can Help?
Predictive maintenance plays an important role in modern operational strategies by addressing challenges and offering benefits:
By detecting potential equipment issues early, global predictive maintenance strategies minimizes the risk of unexpected equipment failures and the expensive downtime associated with it.
Real-time performance monitoring ensures that equipment functions efficiently, energy consumption is reduced, sustainability and ESG goals are aligned.
PdM prolongs the life of assets by addressing problems before they lead to major failures. This also reduces the need for frequent replacement.
Shifting from reactive to predictive maintenance improves resource management, production planning, and operational efficiency.
Now, to address these challenges, smarter global predictive maintenance strategies must be embraced.
The Future of Energy-Centered Predictive Maintenance (ECPdM)
Energy-centered predictive maintenance (ECPdM) enhances the scope of global predictive maintenance further by integrating energy consumption as a critical metric. So, apart from predicting equipment failures; it ensures minimal wastage while maintaining machinery health.
This approach ensures:
- Reduction of carbon footprint by tracking and reducing energy usage.
- Minimization of energy cost by detecting and reducing excessive energy consumption.
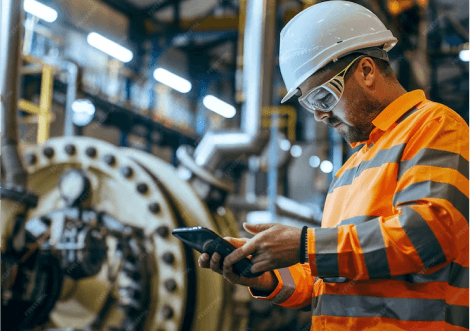
How Nanoprecise is Leading Global Predictive Maintenance Strategies
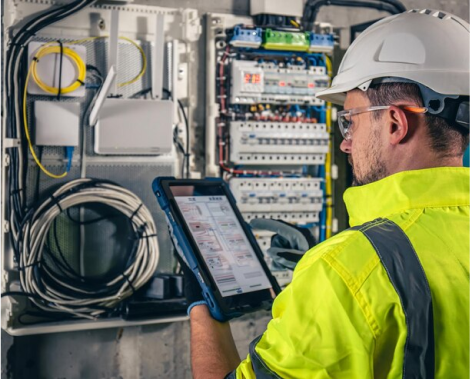
Powered by advanced technology, Nanoprecise is leading the way in global predictive maintenance to provide actionable insights through AI-powered IIoT sensors. Our innovative 6-in-1 sensors track essential parameters like vibration, temperature, humidity, acoustic emissions, RPM, and magnetic flux, enabling the early detection of machinery faults, energy optimization, and extended equipment lifespans.
With a global footprint, from pharmaceuticals in North America to utilities in Europe, we’ve helped industries save millions by reducing downtime and cutting energy costs. Our Energy-Centered Predictive Maintenance solution has prevented hundreds of hours of downtime, lowered CO2 emissions, and saved companies substantial amounts in excess energy use, all while aligning with sustainability and ESG goals to ensure regulatory compliance and reduce carbon footprints.
Ready to Optimize Your Maintenance Strategy?
By adopting Nanoprecise’ predictive maintenance solutions, your business can:
- Minimize unplanned downtime and cut maintenance costs.
- Boost operational efficiency while reducing energy usage.
- Align with global sustainability goals and meet ESG objectives.
Get in touch with us today to discover how Nanoprecise can elevate your maintenance strategy and help you achieve energy efficiency and operational excellence.
Request a Call Back
Frequently Asked Questions
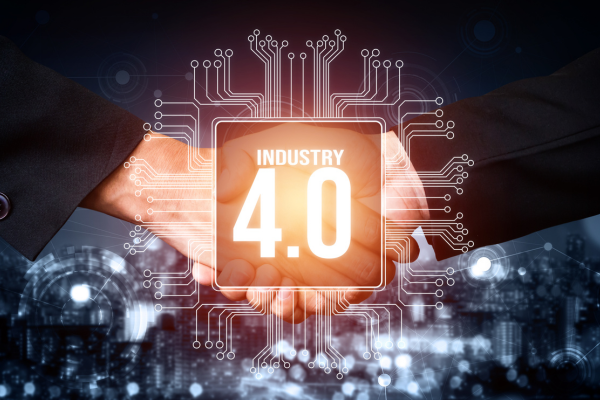
Let us show you how!
Explore the transformative potential of predictive maintenance. At Nanoprecise, we specialize in tailoring predictive maintenance to your unique needs. Reach out today, and together, let’s pave the way for a more efficient, profitable and sustainable future.