Condition Based Maintenance
Condition based monitoring strategy monitors the real-time condition of an asset to decide what maintenance needs to be performed. It requires that maintenance should only be performed when certain indicators show signs of irregularities, decreasing performance or indicates an upcoming failure.
Condition-based Maintenance Strategy
Condition-based maintenance is a maintenance strategy that tells maintenance technicians what condition the equipment is in (such as temperature, humidity, and power), not how it is performing.
The maintenance technician can then determine if the system is in good condition, or in need of repair. In a Condition Monitoring and Maintenance strategy, maintenance is performed when certain indicators indicate that a system is in danger of failure.
When specific indicators show signs of decreasing performance or impending failure, it is in the best interest of the equipment to have maintenance performed before a failure occurs, to avoid shutdowns and downtime.
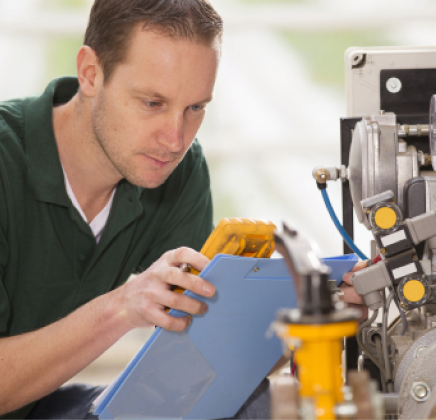
Goal of condition-based maintenance
Condition-based maintenance helps lower the failure rate of a system. It tells us when maintenance will be most useful. When working on a non-mission critical system, such as say a flight simulator, condition-based maintenance will tell us to perform no maintenance on that system for a period of time.
Of course, the failure rate will go up dramatically, but we will be keeping our pilots safe, and we will not be catching flight line workers in the process of dealing with the failure.
The goal of a condition monitoring maintenance framework is to reduce costly disruptions and maintain predictable operational performance of the machines. It helps maximize maintenance resources and reduce the impact of maintenance problems.
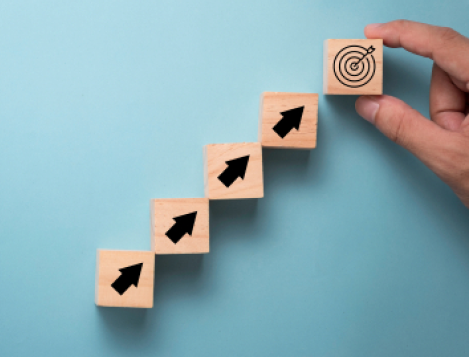
What is Effective Condition Monitoring Maintenance?
Effective Condition Monitoring Maintenance involves an assessment of performance, equipment, maintenance intervals, and human performance. These elements are examined and given a grade. The results of the assessment provide recommendations to reliability professionals on how to respond to the condition of the equipment.
For example, if you are unable to perform work during scheduled maintenance intervals due to severe corrosion or part failure, condition-based maintenance can detect the condition and automatically schedule preventive maintenance. If a part is scheduled for replacement, Condition Monitoring Maintenance can guide you through a phase-out strategy.

Types of condition-based maintenance
There are several types of condition-based maintenance, each with different objectives, however, not all types are applicable to all machines. These includes, oil analysis, vibration analysis Ultrasound analysis, Electrical analysis, Pressure analysis and Temperature analysis among others.
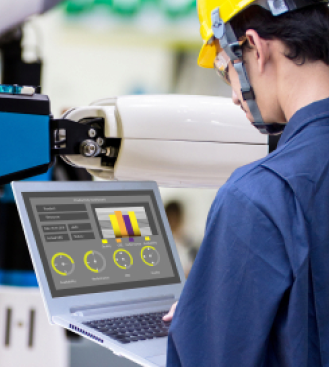
Performance-based Monitoring
The condition-based maintenance has also moved ahead with technology advancements, thereby incorporating newer techniques such as Performance-based monitoring, which was unheard of earlier.
Performance based condition monitoring is similar to traditional condition-based maintenance, but it also focuses on the actual performance and reliability of the equipment. If a machine is running at less than 80% of its operating potential, then maintenance should be done to keep it in that condition. If a machine is running at 95% of its potential, then it needs no maintenance at all.
Performance based monitoring makes it easier to understand performance data and understand its historical context. A technician can then compare the number of failures of the same type at a different time.Of course, the failure rate will go up dramatically, but we will be keeping our pilots safe, and we will not be catching flight line workers in the process of dealing with the failure.
Challenges of condition-based maintenance
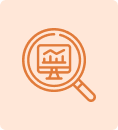
Condition-based maintenance is a critical strategy for large and complex assets such as electrical power grid and oil & gas pipelines. However, its implementation in industrial operations is limited by its ability to detect process system degradation before it occurs. It also requires a high-level of automation and integration within asset lifecycle management softwares.
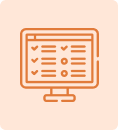
Only a few Asset Information Management softwares integrate condition-based maintenance data with their asset health management data. That is where predictive maintenance adds value. It mitigates the challenges associated with traditional condition-based maintenance by offering real-time predictive information about the genuine health and performance of industrial assets.
Future of condition-based maintenance
With newer advancements in technology, condition based maintenance strategies evolve at a much faster pace to accommodate a wide variety of equipment sets across various sectors.
The evolution of Industrial Internet of Things (IIoT) and Artificial Intelligence (AI) systems in manufacturing operations offers a foundation for next-generation maintenance strategies through interconnected network of systems that help monitor, collect and analyze machine health data, thus facilitating real-time performance information of machines.
It enables maintenance and reliability professionals to detect inefficiencies & anomalies earlier than the conventional techniques, which helps manufacturers to take critical business decisions in an accurate & timely fashion, thereby saving time & money.
Integrated predictive maintenance system from Nanoprecise propels condition monitoring & maintenance to the next level, by helping manufacturers lower maintenance costs, reduce downtime, increase productivity and improve equipment reliability.
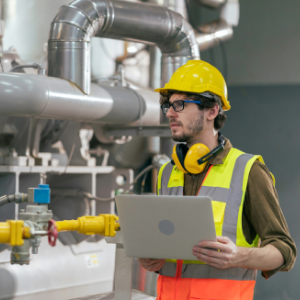
Conclusion
The biggest challenge that companies face when it comes to maintenance are the costs involved with repairs. Although maintenance can be costly, it’s not all bad. Maintenance can save time & money because it ensures proper functioning of the equipment, and offers real-time machine health data that can help decision makers to make prudent business decisions. Also, it saves equipment from breakdown, which otherwise can cause huge problems for the company as well as their customers.
Nanoprecise offers Automated end-to-end predictive maintenance systems that help customers across sectors such as Chemicals, Pharmaceuticals, Cement and Metals among others, with its state-of-the-art IoT hardware and Artificial Intelligence, to predict faults, prescribe solutions and avoid catastrophic failures by overcoming the downsides of a traditional condition-based maintenance regime. AI-based Predictive Condition Monitoring & Maintenance Solutions from Nanoprecise helps manufacturers significantly improve their equipment’s performance, increase their efficiency and reduce downtime, thereby helping them to stay competitive in the global markets.
Request a Call Back
Frequently Asked Questions
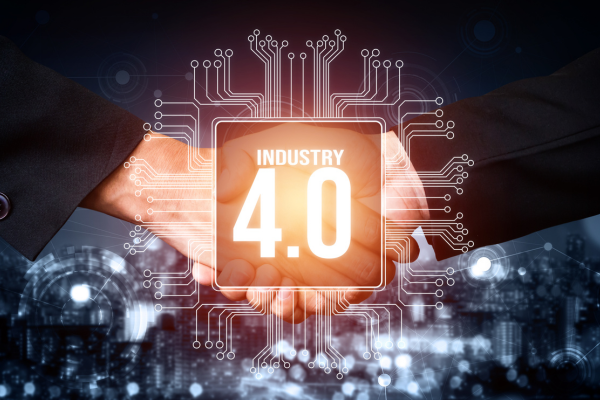
Let us show you how!
Explore the transformative potential of predictive maintenance. At Nanoprecise, we specialize in tailoring predictive maintenance to your unique needs. Reach out today, and together, let’s pave the way for a more efficient, profitable and sustainable future.