Energy Management Software
Make your industry operation sustainable and energy efficient with energy-centered maintenance
Energy-Centered Maintenance
Monitoring and managing energy efficiently are essential to establish a sustainable environment. In this regard, Energy-Centered Maintenance (ECM) is an energy management software with an innovative and sustainable approach to reduce energy consumption and wastage. To do that, ECM ensures that excess energy usage or any energy wastage can be monitored through signals that will indicate the need for maintenance or repairs.
ECM involves six essential steps:
- Identifying energy-related equipment
- Collecting data and predicting baseline energy use
- Developing an ECM inspection plan
- Monitoring equipment performance and comparing it to the baseline, with deviations prompting a root cause analysis
- Selecting necessary maintenance actions to restore efficiency
- Improving maintenance plans
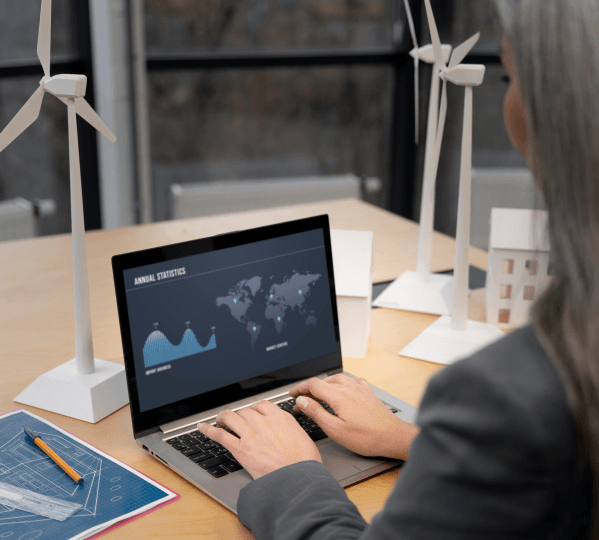
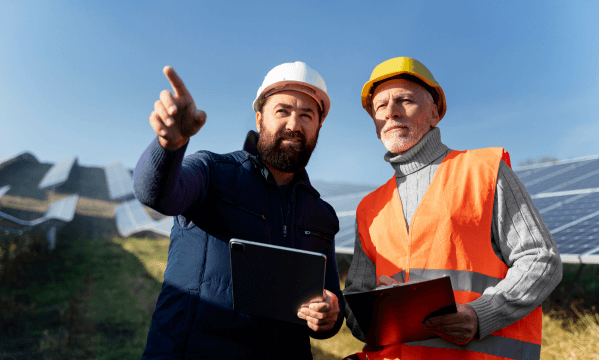
With an overall accuracy in measurement, high-quality, and reliable technology; ECM’s potential to make a difference is substantial. According to one of the recent case study, ECM can reduce energy consumption by up to 30%. Considering the fact that 60% of global electricity is used by motor-driven machinery, any wastage can significantly increase the consumption of energy. Hence, ECM can optimize the power consumption. Its hardware solution of a wireless IIoT-based sensor features a large battery, and gather diverse data, such as acoustic emission and vibration. While its software solution automates prediction and prescription, detects anomalies with high accuracy, diagnoses faults confidently, and predicts failure meticulously.
Best energy management software
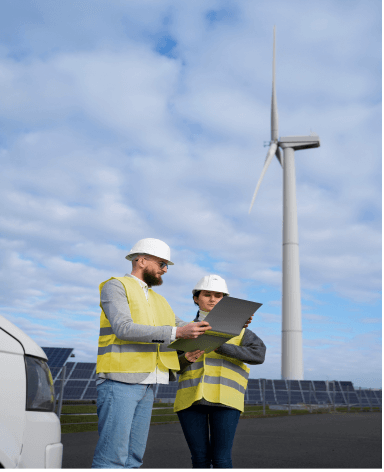
Since efficiency and environmental sustainability are important factors to begin with, embracing continuous innovation and advanced data analytics is essential. This is where, Nanoprecise Sci Corp’s Energy Dashboard, NrgMonitor appears as a dependable offering. NrgMonitor is an advanced energy monitoring software and has the ability to transform the traditional maintenance strategy.
The Energy Dashboard of NrgMonitor leverages real-time data analytics to monitor and analyze energy consumption patterns. It identifies inefficiencies and predicts potential issues before they escalate. Its intuitive interface empowers users to visualize energy usage across various equipment and systems, enabling them to make informed decisions and proactive maintenance. By prioritizing energy efficiency, the energy dashboard not only helps in reducing operational costs but also contributes to environmental sustainability. Hence, such advanced technology and comprehensive insights make Nanoprecise Sci Corp’s NrgMonitor the best software tool for organizations committed to optimizing energy usage and achieving sustainability goals.
NrgMonitor offers a complete spectrum of energy visibility
Now, energy optimization requires a detailed understanding of how much energy machines consume and its requirement for maintenance. Here, NrgMonitor comes to the rescue. It tracks the energy consumption patterns for motor-driven equipment and provides visibility on the overall power consumption and its efficiency. Through real-time data collected by the MachineDoctor sensors, NrgMonitor monitors help with changes in power consumption that is resulted by equipment operating in a faulty state. NrgMonitor also helps to track the increase in CO2 emissions, ensuring compliance to regulations.
The best part about NrgMonitor is that it is compatible with various equipment types such as; motors, pumps, gearboxes, engines, bearings, turbines, reactors, and generators. Since it’s powered by AI, it can seamlessly integrate via IIOT Sensors and can be easily deployed wherever required. This cost-saving solution ensures quick ROI, making it one of the best energy monitoring software in the market.

Features and insights of Nanoprecise’s energy management software – NrgMonitor
Let’s take a quick look at the features of Nanoprecise’s energy management software that enables it to stand out from its traditional counterpart. The fact that NrgMonitor is a comprehensive analytical tool specially designed to optimize energy management, is a game changer.
it offers several key features
- Baseline energy consumption measurement for the equipment to identify any deviations and inefficiencies to prescribe corrective measures.
- Trend monitoring to track changes in energy consumption as per the identified baseline that helps to indicate any underlying issues.
- Predictive accuracy and real-time monitoring powered by advanced algorithms ensure accuracy that it further validated through rigorous internal testing.
These features provide deep insights into energy usage patterns, ensuring proactive maintenance and energy optimization. Through continuous monitoring and data analysis, this energy management software reduces equipment inefficiencies and in turn operational costs.
Request a Call Back
Frequently Asked Questions
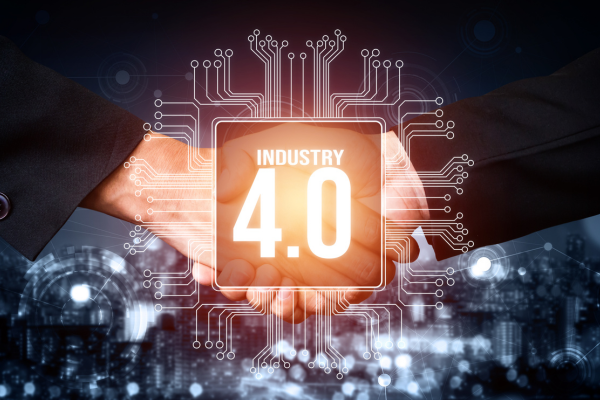
Let us show you how!
Explore the transformative potential of predictive maintenance. At Nanoprecise, we specialize in tailoring predictive maintenance to your unique needs. Reach out today, and together, let’s pave the way for a more efficient, profitable and sustainable future.