Equipment Health Analytics
Enhance operational efficiency using right analytics
Challenges Industries Face Without A Robust Platform To Monitor Asset Health
In the absence of the equipment health analytics platform, industries rely upon reactive maintenance approaches where repairs take place based on equipment failure. This legacy approach leads to costly downtime and production losses. Another critical reason equipment health analytics is important is that with data-driven insights, maintenance and resource allocation decisions become easier and more efficient. In this aspect, manual data collection and analysis are time-consuming and prone to errors, hindering the ability to identify emerging issues promptly.
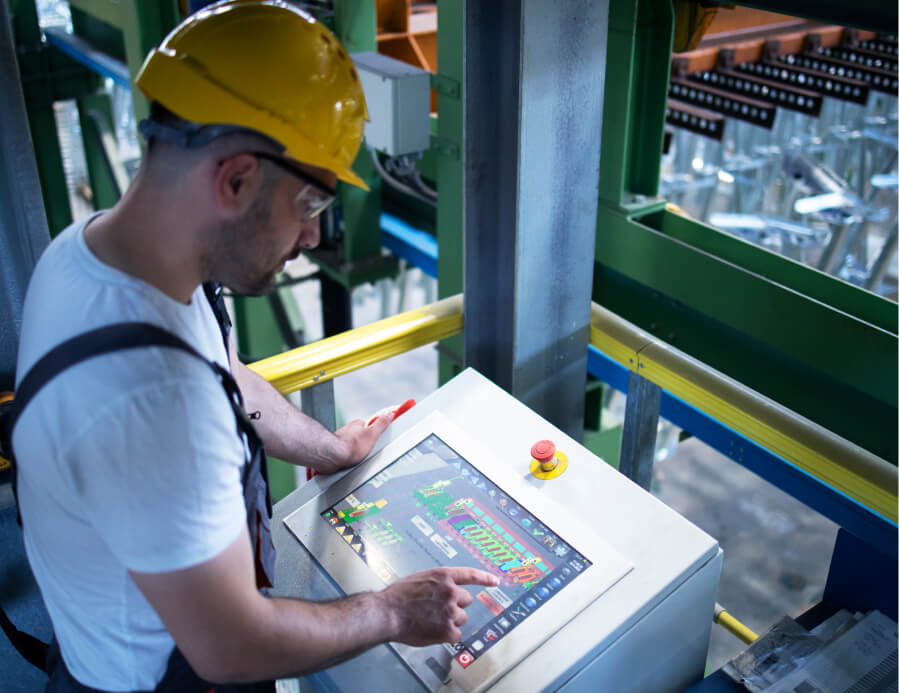
RotationLF from Nanoprecise
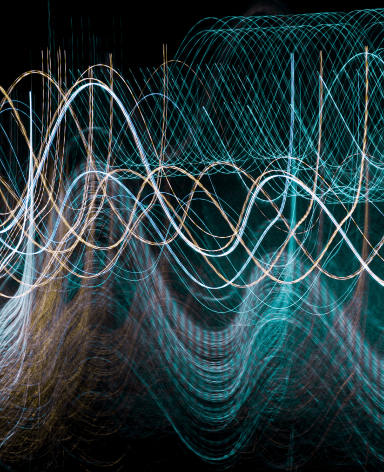
Nanoprecise revolutionized the equipment health analytics space with RotationLF, a cutting-edge platform integrated with AI, physics-based models, and IIoT. The solution from Nanoprecise is highly scalable and designed to fit various equipment, including motors, pumps, gearboxes, engines, bearings, turbines, reactors, and generators.
RotationLF has AI as the backbone, minimizing learning cycles, reducing false alarms by up to 90%, and setting a new benchmark in predictive maintenance. Apart from detecting anomalies, the platform offers insight into specific fault modes and the estimated time to failure. Such a comprehensive overview of complex machine health with sensor-agnostic data ingestion makes it adaptable to any setup.
One notable feature of RotationLF, is its cloud-based nature and support for last-mile automation through an open API, ensuring seamless integration with existing systems. By combining advanced AI with CEEMDAN, the platform creates customized solutions for different plants and complex equipment. With improved signal processing and fault detection, the solution can identify issues in equipment health in as little as five days. This helps us keep operations running smoothly and equipment in good condition.
The Significance Of Asset Health Monitoring
Equipment Health Analytics is a vital proactive maintenance strategy for industrial operational efficiency. With the help of IIOT-based sensors, real-time data, and AI-driven platforms, one can predict failures that help in timely intervention to fix a critical machine. Such preventive approach not only optimizes maintenance of the critical machines but also extends the overall lifespan of an equipment.
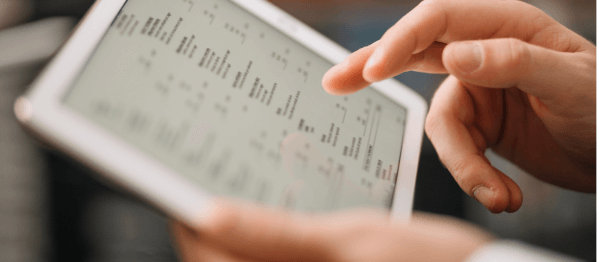
Distinctive Features of the Nanoprecise Health Analytics Platform
Sensor Agnostic
Works with any hardware.
Remaining Useful Life
Pinpoints component, fault, and failure time.
Quick Detection
Value in 5 days with AI learning.
Minimize False Alarms
Adaptive thresholds for precise alerts.
Request a Call Back
Frequently Asked Questions
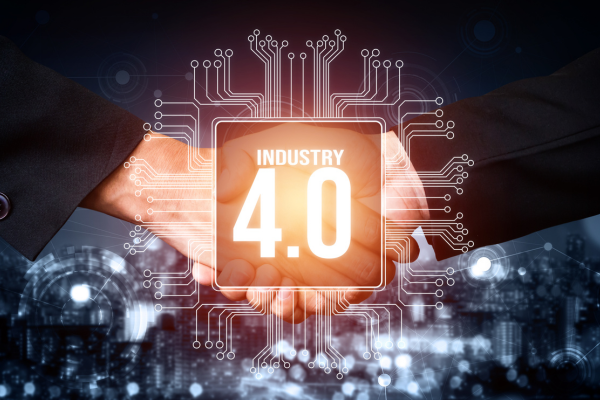
Let us show you how!
Explore the transformative potential of predictive maintenance. At Nanoprecise, we specialize in tailoring predictive maintenance to your unique needs. Reach out today, and together, let’s pave the way for a more efficient, profitable and sustainable future.