5 minute read
Could predictive maintenance be the solution to increasing profit and achieving a better ROI in the CPG Manufacturing Industry?
Companies introduce new consumer products daily. Yet in the haste to launch these products, the manufacturing process lags behind. Old machines and inefficient maintenance processes create hidden costs that reduce profit; but, many companies still believe: “if it isn’t broken, don’t fix it.”
However, ignoring machine health and energy consumption prevents companies in the CPG industry from reaching their full potential. This blog uncovers the top 5 ROI Killers in the CPG industry, as well as how integrating an energy centered predictive maintenance solution can mitigate all of them!
1. Production Downtime Hurting All ROI Aspects
Unplanned downtime drains money. Every minute your line is down, you’re paying for it with the compounding costs of:
- Machine maintenance.
- Onsite staff doing nothing.
- Production reworks.
- Delayed shipping.
- Administrative costs.
As well as other hidden costs such as brand impact or revenue loss.
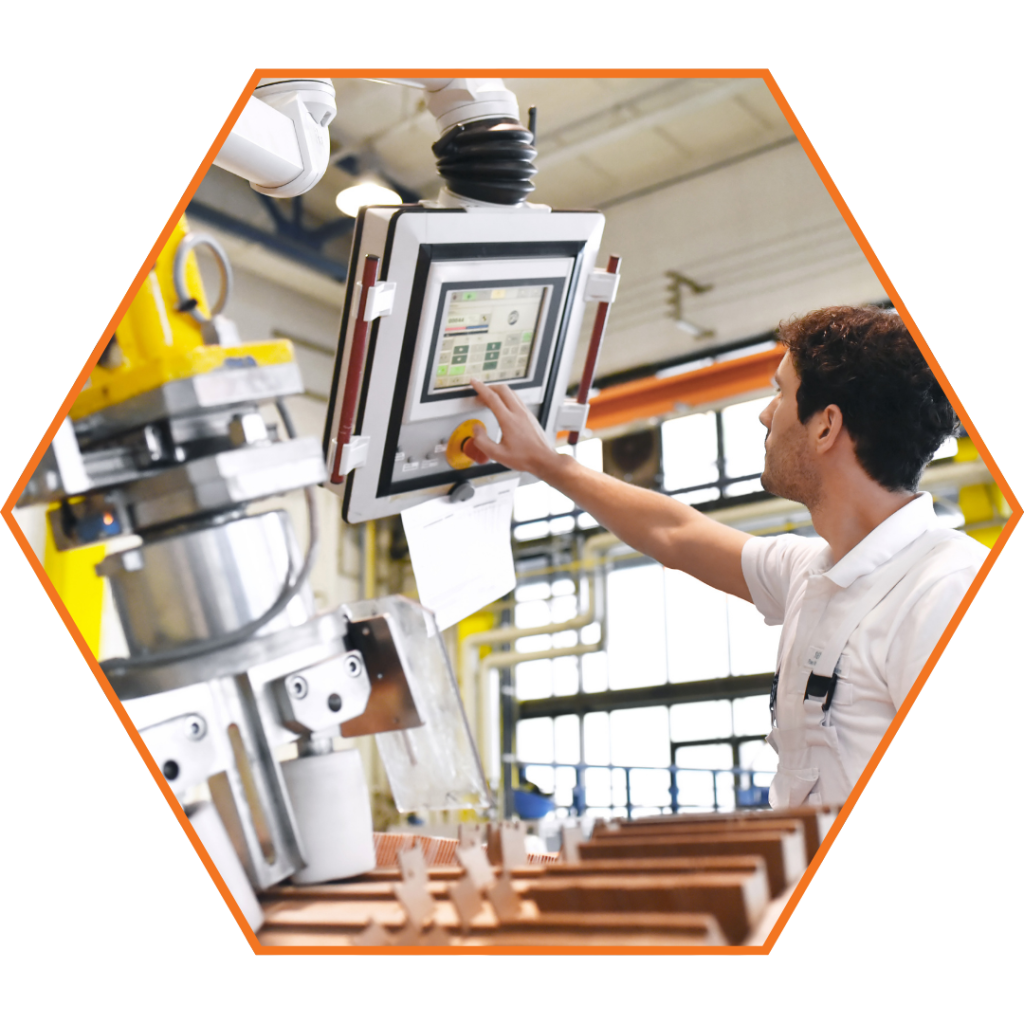
Why it Happens: Without ongoing machine health monitoring, maintenance is usually reactive, or happens on an annual schedule, instead of when it is actually needed.
Predictive Maintenance Solution:
PDM helps you catch machine abnormalities before they become problems and lead to downtime. This helps you to do maintenance on machines when they need it instead instead of estimating.
Using predictive maintenance helps you ensure a strong ROI for all your assets. This includes people, administration, and general maintenance.
Case Study: One of Asia’s largest sugar manufacturers prevented 8+ hours of downtime with PDM.
2. Product Wasted from CPG Manufacturing Equipment Failure
When equipment in CPG manufacturing breaks, it can cause problems. This includes machines like fans, mixers, or packaging equipment. If they fail during production, you might lose an entire run of product.
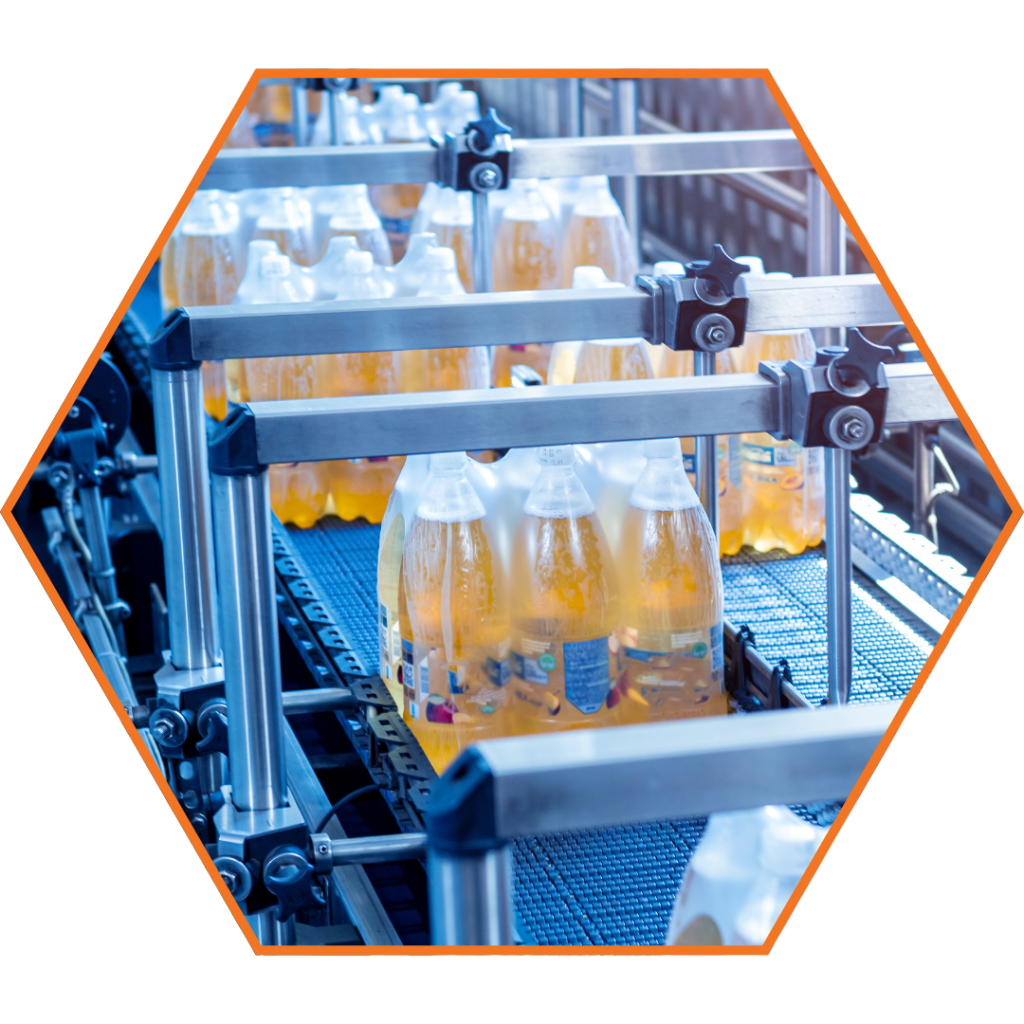
Ruined products include everything from wasted ingredients, wasted labor, and missed delivery windows. It hits your margins hard.
Why It Happens? Traditional maintenance won’t always catch early warning signs. We allow machines to run at ‘good enough’, as long as they don’t fail…until they do.
Predictive Maintenance Solution:
By integrating IOT sensors that track things like energy consumption, vibration, and more in real time, manufacturers can get notifications about any abnormal changes for a number of variables, before problems escalate.
3. No Equipment Health Monitoring & Over-Maintaining Heathy Assets
Traditional Reliability Centered Maintenance often relies on quick spot fixes, annual or monthly schedules, and guesswork. This means maintenance teams often miss early warning signs, or end up servicing equipment that doesn’t need it. This creates a gray area for machines with real issues to operate undetected.
Why It Happens:
- No centralized system for equipment health monitoring.
- Time-based preventive maintenance doesn’t account for the actual condition of assets.
This lack of visibility not only increases the risk of equipment failure but also leads to over-maintenance, wasted labor, unnecessary part usage, and avoidable downtime.
Predictive Maintenance Solution:
Predictive maintenance combines data and condition monitoring to deliver actionable insights into the true state of your equipment.
With easy-to-use dashboards and smart analytics, modern predictive maintenance solutions give your team full visibility into:
- Which are at risk of failure.
- Which assets are healthy,
- Which need attention.
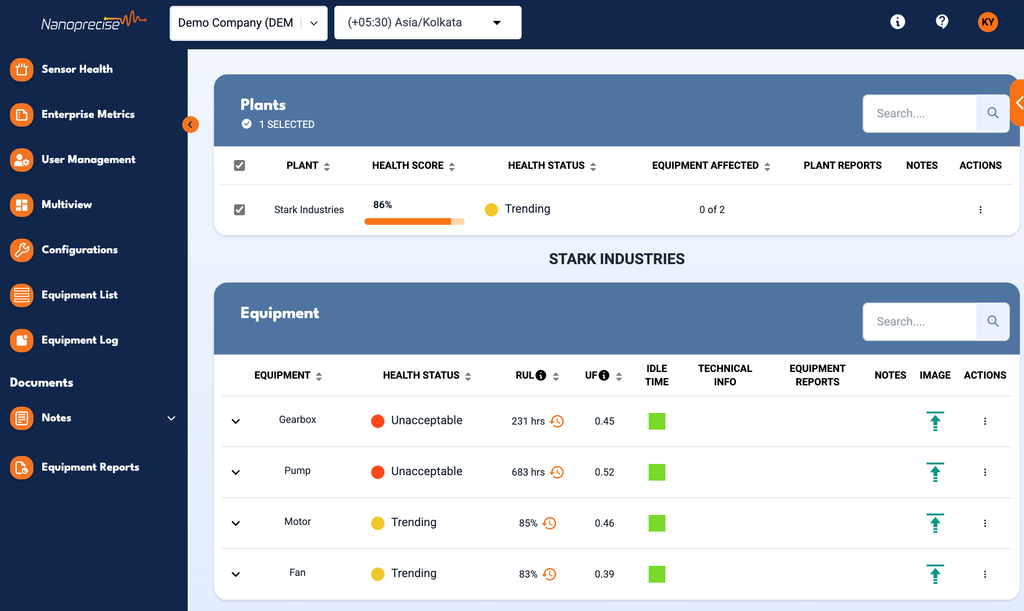
This helps your team move away from outdated calendar-based service routines and reduce waste by prioritizing maintenance where and when it’s needed.
Video: Predictive Maintenance Dashboard that delivers comprehensive insight into your assets.
4. Sustainable CPG: Preventing Energy Waste
It’s no longer acceptable to ignore to energy consumption as the costs for energy rise.
Machines that are running inefficiently or operating outside of normal ranges are leaking power and can silently cost operations tens of thousands per year – and most won’t even notice!
Predictive Maintenance Solution:
Utilizing a system that monitors energy consumption, like our NRG Monitor.
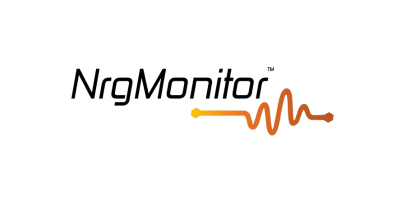
NRG Monitor tracks the energy consumption patterns of your machinery and sends notifications when specific machines are not operating properly.
5. Lack of Consolidated Maintenance Data
Many still rely on handwritten logs, spreadsheets and knowledge from consultants or longstanding team members.
But this data is spread out everywhere. Unorganized data means you can’t track what’s happening and what’s not working, impacting your bottom line.
Why it happens:
Many CPG manufacturing plants lack a centralized system to collect, store, and analyze maintenance history.
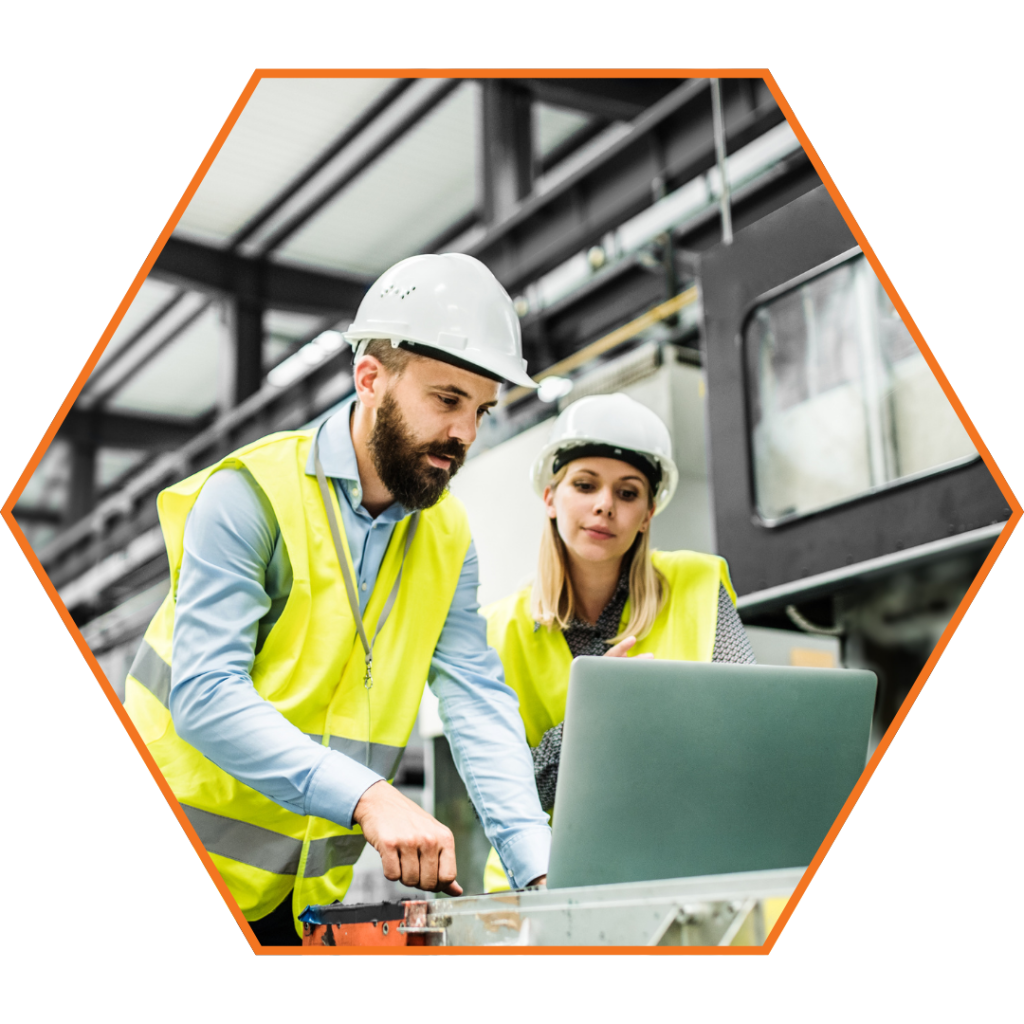
Predictive Maintenance Solution:
A good predictive maintenance solution should store all maintenance records, alerts, and historical trends in one system.
This helps you build a maintenance strategy on data, not guesswork.
Conclusion:
These 5 killers are common. But they can be mitigated by utilizing predictive maintenance in CPG Manufacturing.
With an advanced Energy Centric Predictive Maintenances solution like Nanoprecise, you can reduce financial losses by lowering energy costs, and improve asset reliability with better visibility into machine health.
?Ready to increase profitability in your plant? Get the Free Nanoprecise Feature Sheet!