Smruti Sambit’s Journey as a Reliability Leader at Nanoprecise
“When I joined Nanoprecise, I thought my work would be about condition monitoring in its most technical sense — vibration patterns, thresholds, and fault modes. What I did not realize then was that I would also become a bridge between people, machines, and their environments.”
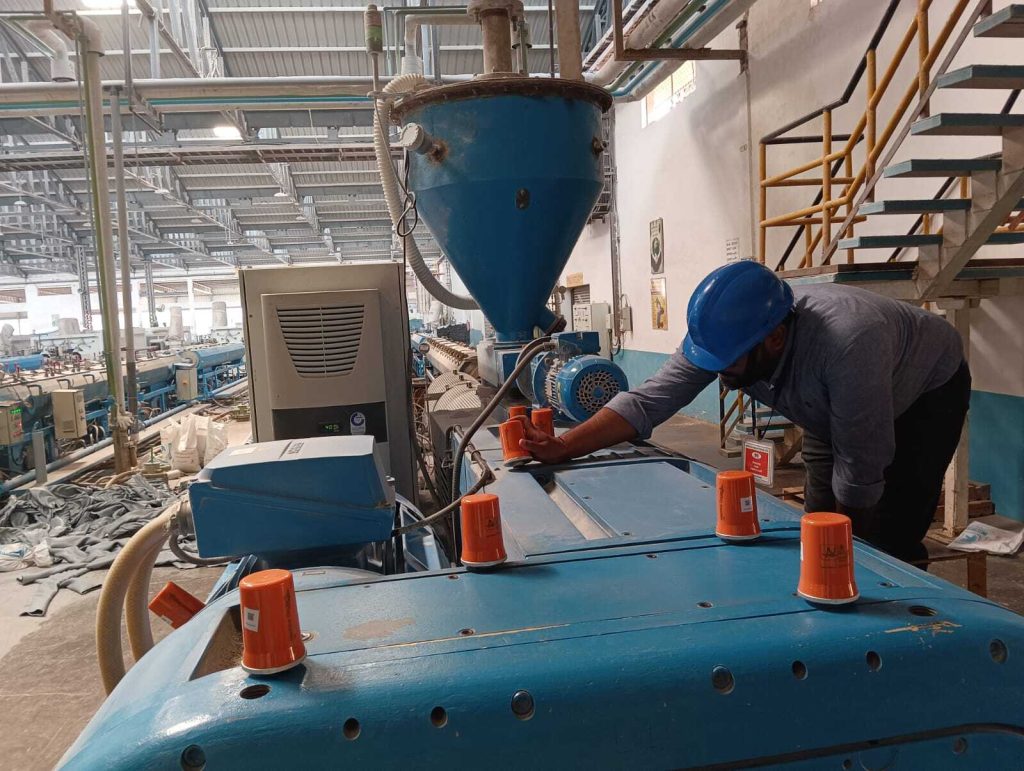
I am Smruti Sambit, Lead Solution Architect for APAC at Nanoprecise. My journey spans not just APAC, but also Middle East and over the years, my role has grown far beyond installing sensors or analyzing data trends or making reports to prepare a holistic solution for customers.
Today, I see myself as a translator — someone who helps industries understand what their machines are trying to say, and how to act on those insights in a way that truly improves reliability, energy use, and peace of mind.
My work begins where most problems do occur — on the plant floor. Not in dashboards, and not in the office. But in the spaces where machines run nonstop, where every sound, vibration, and energy spike tell a story, and where teams are trying to stay a step ahead of failure.
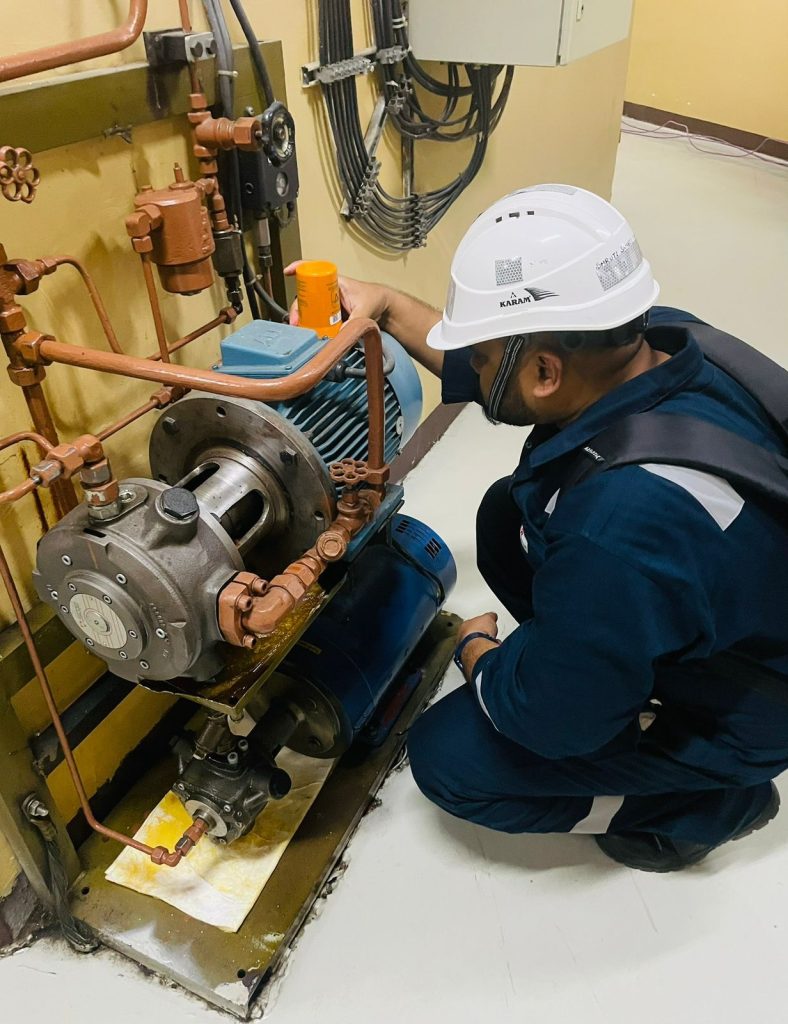
Whether it’s a cement plant in Vietnam, a hydro power plant in the remote islands of the Philippines, an oil refinery in Saudi Arabia, or a steel mill in India — every industrial site is its own ecosystem. Each comes with its own set of challenges, constraints, and operational rhythms.
That’s why our work always starts on the ground — not behind dashboards, and not with data streams. Before we talk about AI, alerts, or analytics, we walk the floor.
My team look closely at how the plant operates: the equipment layout, the operating conditions, the power sources, the network availability, and the environmental factors — dust, heat, vibration, or remoteness — that influence how a solution will actually perform in the real world.
We work as a hands-on team of condition monitoring engineers who understand that no two sites are the same. It’s not just about installing sensors or running diagnostics — it’s about understanding how machinery behaves in real-world conditions.
Whether it’s dealing with challenging mounting locations, adapting to different operational standards, or working closely with plant teams to fine-tune the monitoring approach, the goal remains simple: to improve reliability, reduce unplanned downtime, and help maintenance teams stay a step ahead.
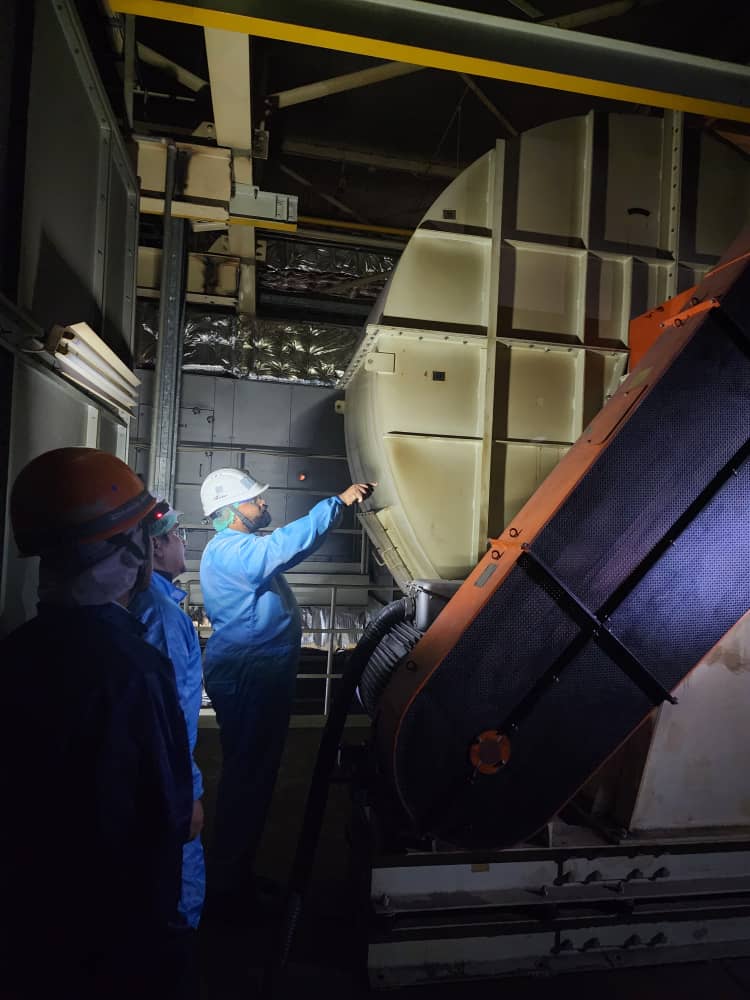
We ask:
- Where is the equipment located, and how accessible is it for maintenance?
- What are the expected loads, and what variabilities are common?
- What does failure look like here, and what’s the cost?
- Technical details to understand machine characteristics?
- And most importantly, what does the plant team need?
Because true reliability solution isn’t about dropping in a sensor and walking away, it’s about understanding the criticality of the asset, the local constraints, and the daily realities faced by the people working closest to the machines.
There are sites where we’ve had to work around tight spaces, challenging mounting conditions, very high temperature or limited internet coverage. Some teams are cautious, having seen technologies fail to live up to the promise. And there are plants where even a single missed signal can mean a huge loss in production or safety.
And in all these places, we don’t walk away. We lean in.
Because what we bring is not just a monitoring system, but a complete solution. One that’s custom-fit to the plant, built with context, and tuned by listening carefully to both machines and people.
I’ve spent hours with maintenance teams, listening to their challenges, hearing their observations, and tracking machines through their entire load cycle — just to spot what doesn’t look right.
That’s how we catch issues like a subtle vibration pattern indicating an early-stage bearing fault or a small spike in energy consumption that points to a misalignment quietly driving up power costs.
Today, it’s no longer just about preventing breakdowns. Industries are under increasing pressure to cut energy waste, improve uptime, and meet carbon reduction goals. The same data that helps predict failures is now key to optimizing equipment performance — minimizing excess energy use, extending asset life, and supporting ESG targets. This isn’t just maintenance anymore. It’s operational efficiency, energy management, and reliability — all working together at scale.
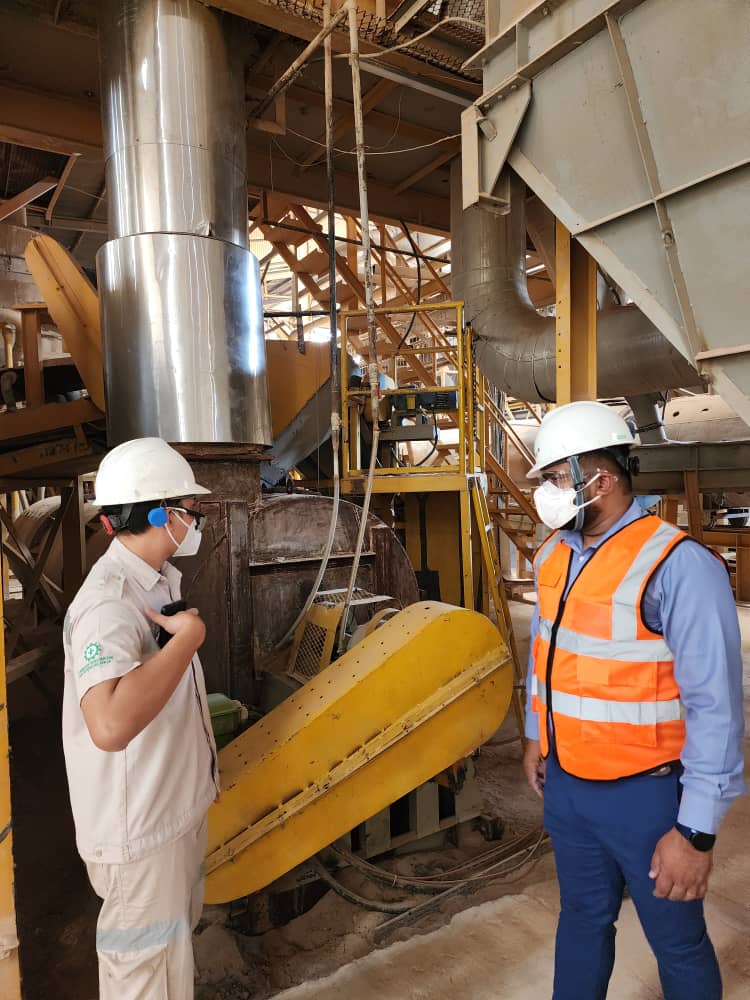
We’ve seen this evolve firsthand. A pump that runs with 8% misalignment isn’t just a reliability issue — it’s an energy drain and a carbon footprint problem. Every kilowatt wasted, every hour of inefficiency compounds into higher costs and missed sustainability targets. Our work is now as much about optimizing energy and reducing emissions as it is about avoiding failures.
And I’m not alone in this. Every solution we deliver at Nanoprecise is the result of collaboration across our teams — from Solution Architects and Condition Monitoring Engineers to Customer Success and Support. It’s not just me walking the plant floor; it’s a shared commitment across functions to truly understand the needs of each site and deliver reliable outcomes. We all listen, adapt, and solve — together. That’s what makes our approach stronger, and our impact deep
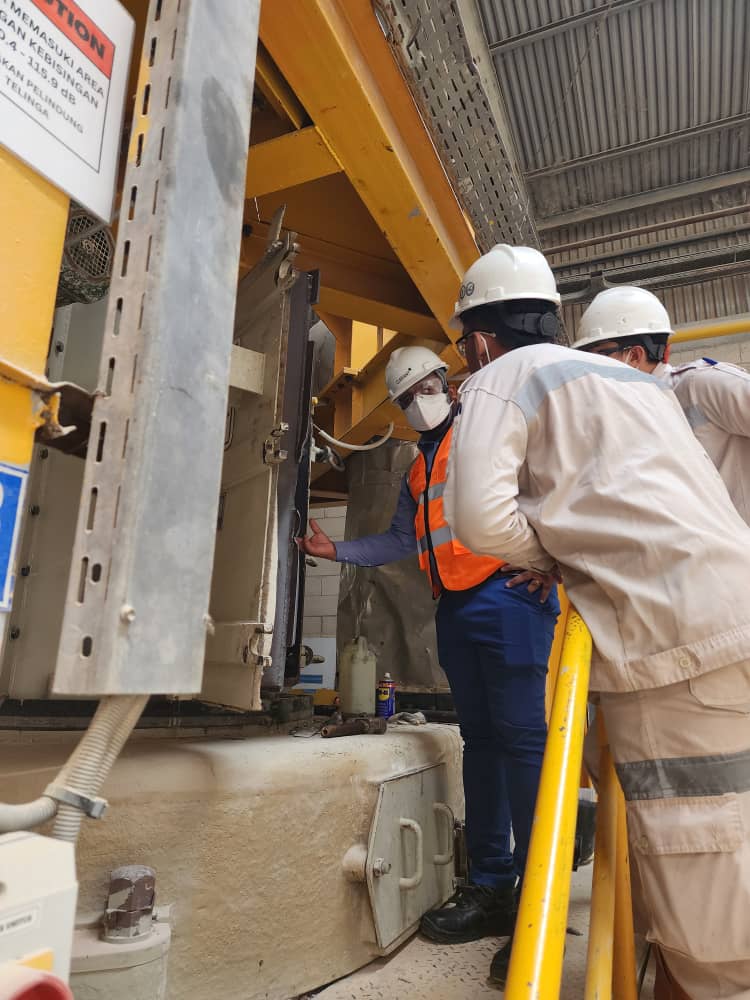
This journey has shown me that the future of industrial reliability isn’t just in advanced technology.
It’s in how well we connect:
- Machines in their context
- Data to insight
- And teams to solutions they can count on.
To me, reliability means more than just prediction — it’s about partnership.
It’s not just alerts — it’s action.
It’s not just what we install — it’s what we help improve.
Every site visit, whether in India, SEA, or the Middle East, is meaningful when machines run smoothly and teams feel confident, knowing they’re prepared.
When we listen to both the machines and the people, we don’t just monitor —
We solve.
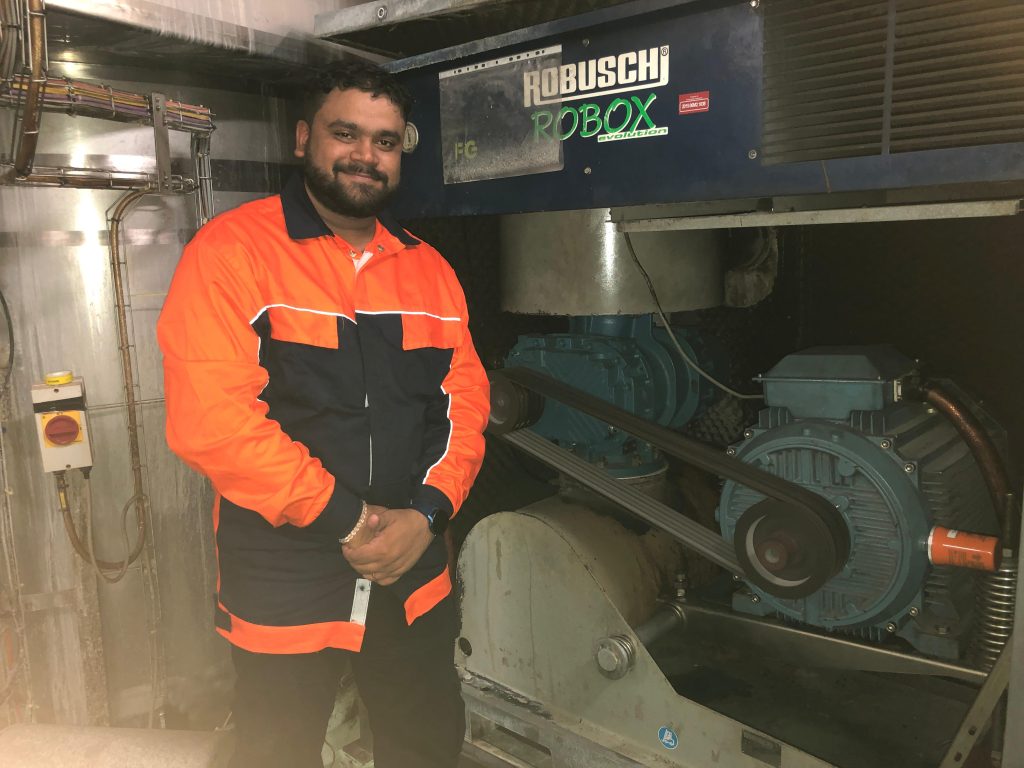