And how Predictive Maintenance Prevents Them.
Could predictive maintenance be the missing solution to many of the challenges the food and beverage industry faces?
Demand remains constant, with new products continuously being introduced and changing the manufacturing process. Yet margins keep tightening as food production costs rise, and maintaining a sterile facility remains non-negotiable.
In an industry driven by innovation and constrained by thin profit margins, the pressure to maintain smooth operations is relentless.
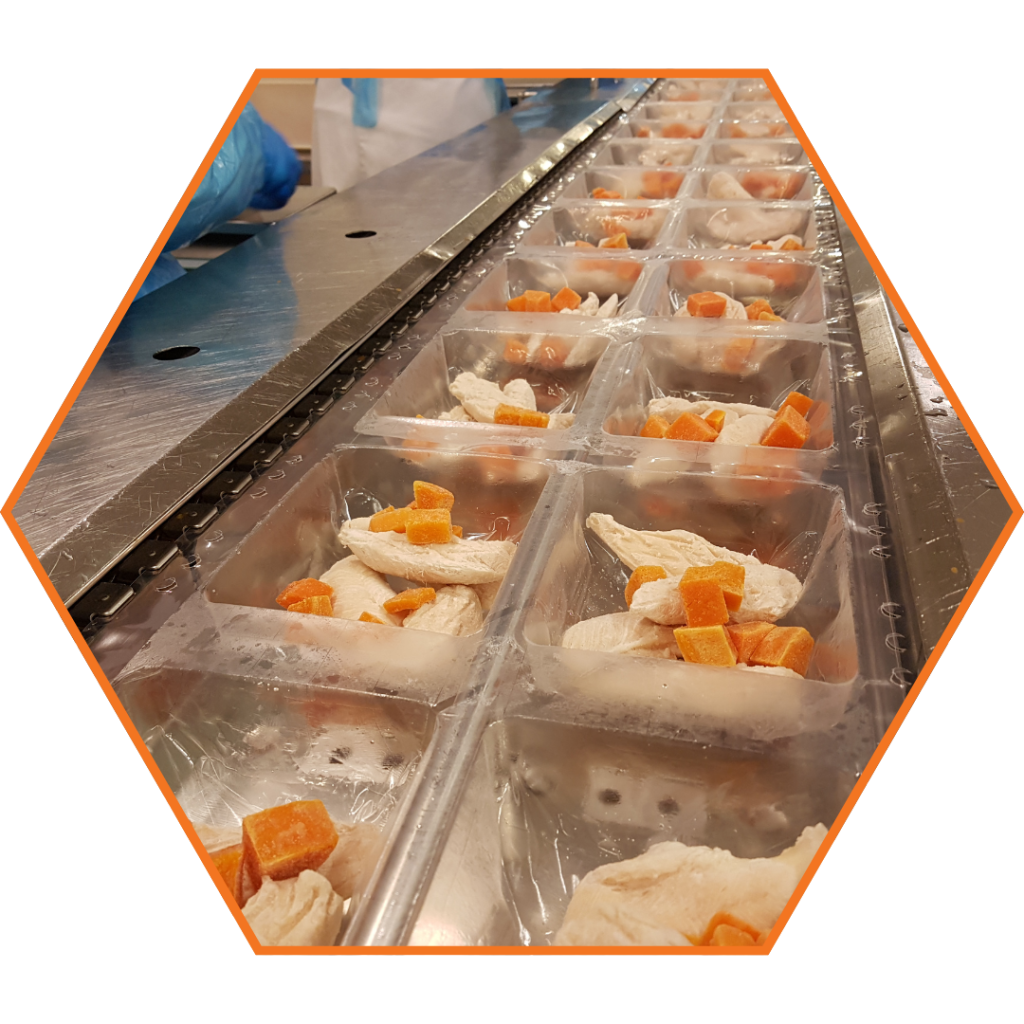
The desire to keep things running leaves little time to stop and check overall machine health. As a result, many operations adopt a mindset of “good enough” or “if it isn’t broken, don’t fix it.”
However, lack of consideration into overall machine health in food and beverage manufacturing is the consistent silent killer of ROI. This blog will share the top 7 ROI killers that we have seen, as well as solutions to fix them by integrating Predictive Maintenance!
1.Product Spoilage from Equipment Failure
When equipment breaks mid-production—like a cooler, mixer, or packaging machine—it can lead to the loss of an entire batch of product.
Spoiled products include everything from wasted ingredients, wasted labor, and missed delivery windows. It hits your margins hard, and your brand even harder.
Why It Happens? In the context of machine failure, traditional maintenance won’t always catch early warning signs. Machines often run at ‘good enough’, before failing completely.

Predictive Maintenance Solution:
By integrating IOT sensors that track temperature, vibration and overall performance in real time, food and beverage manufacturers can get real time notifications about any abnormal changes, before problems escalate into a full-on equipment malfunction.
2. Production Downtime Costing You More Than You Think.
Unplanned downtime drains money. Every minute your line is down, you’re paying for it, with idle staff, maintenance, product rework, late shipments and more. Not to mention, the potential impact on brand and loss of revenue.
Why it Happens: Without insights into machine health monitoring, maintenance is reactive, instead of strategic and proactive. Teams often find themselves waiting for the right person to fix the issue, instead of scheduling proactive maintenance ahead of time.
Predictive Maintenance Solution:
PDM helps you catch abnormalities before they become problems, allowing you to schedule fixes before a failure occurs by learning which assets are trending toward breakdown so you can act before downtime hits.
3. Lack of Visibility into Equipment Health
Traditional maintenance is often filled with spot fixes and guesswork into the root cause of the issue. Most maintenance teams are either missing problems or wasting time fixing things that aren’t broken (allowing underlying issues to progress).
Why it happens: There is no centralized system to track machine health in real time and identify issues before they arise.
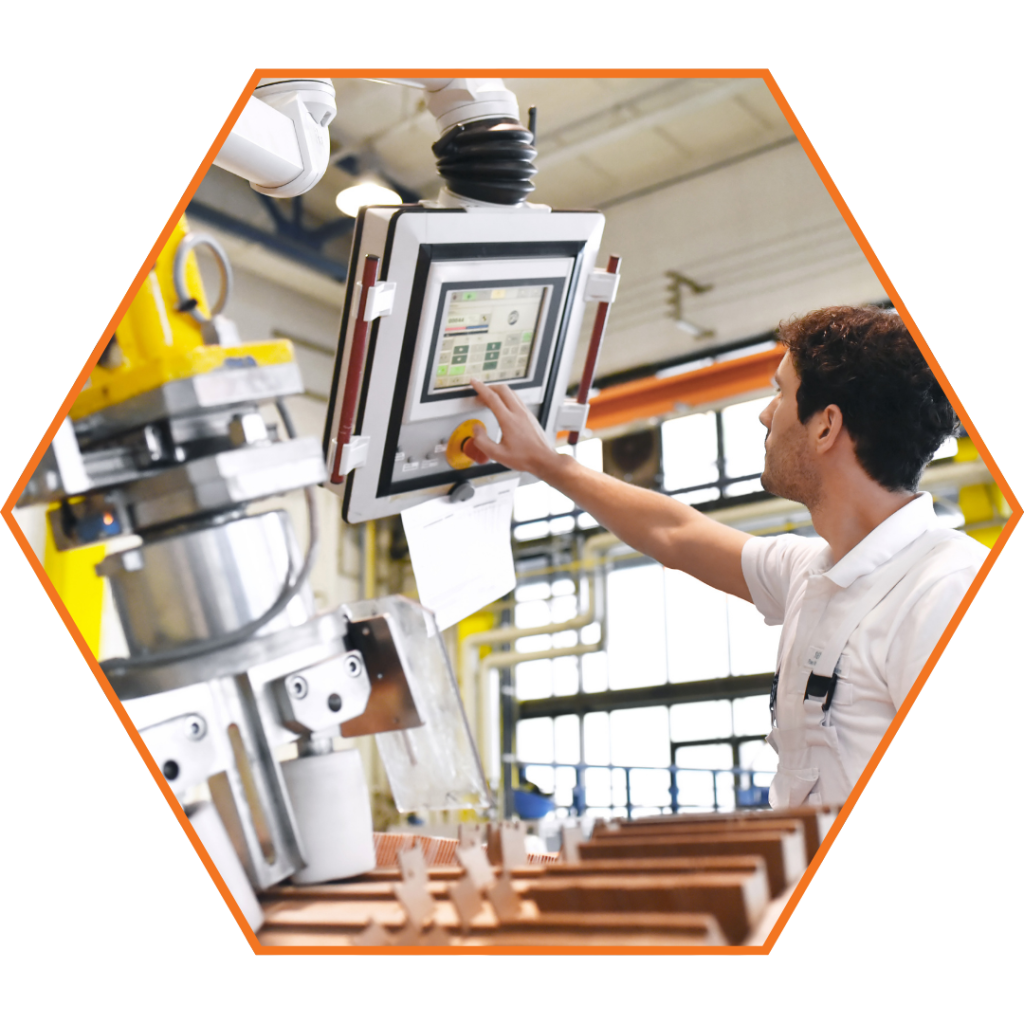
Predictive Maintenance Solution:
Predictive Maintenance Solutions can provide your team with the data and easy-to-view dashboards that give your team full visibility into all key equipment. So, you can learn which assets are healthy, which need attention, and which could fail.
4. Over-Maintaining Healthy Equipment
A further consequence into lack of visibility into machine health is wasted budget. Regular time-based maintenance on certain machines, doesn’t always translate to the most efficient way to ensure smooth operations.
Servicing a machine that doesn’t need it can pull resources away from real issues, burn through spare parts, and create unnecessary downtime.
Why it happens: Rigid PM schedules don’t consider real-time condition.
Predictive Maintenance Solution:
By integrating ongoing condition monitoring, PdM solutions allow your team works smarter—not harder, helping you identify what assets need maintenance and when they need it, not just when the calendar says so.
5. Energy Waste that Slips Under the Radar
Energy costs can be some of the largest line items, and as sustainability targets go up, it’s no longer acceptable to not pay attention to energy consumption.
Machines that are running inefficiently, leaking power or operating outside of normal ranges can cost companies tens of thousands per year without anyone noticing.
Predictive Maintenance Solution:
Utilizing a system that monitors energy consumption, like our NRG Monitor.
6. No Maintenance Data = No Maintenance Strategy
If you’re still relying on handwritten logs, spreadsheets, or tribal knowledge to manage maintenance, you’re playing a dangerous game. No data means you can’t track what’s working, what’s not, or what it’s really costing you.
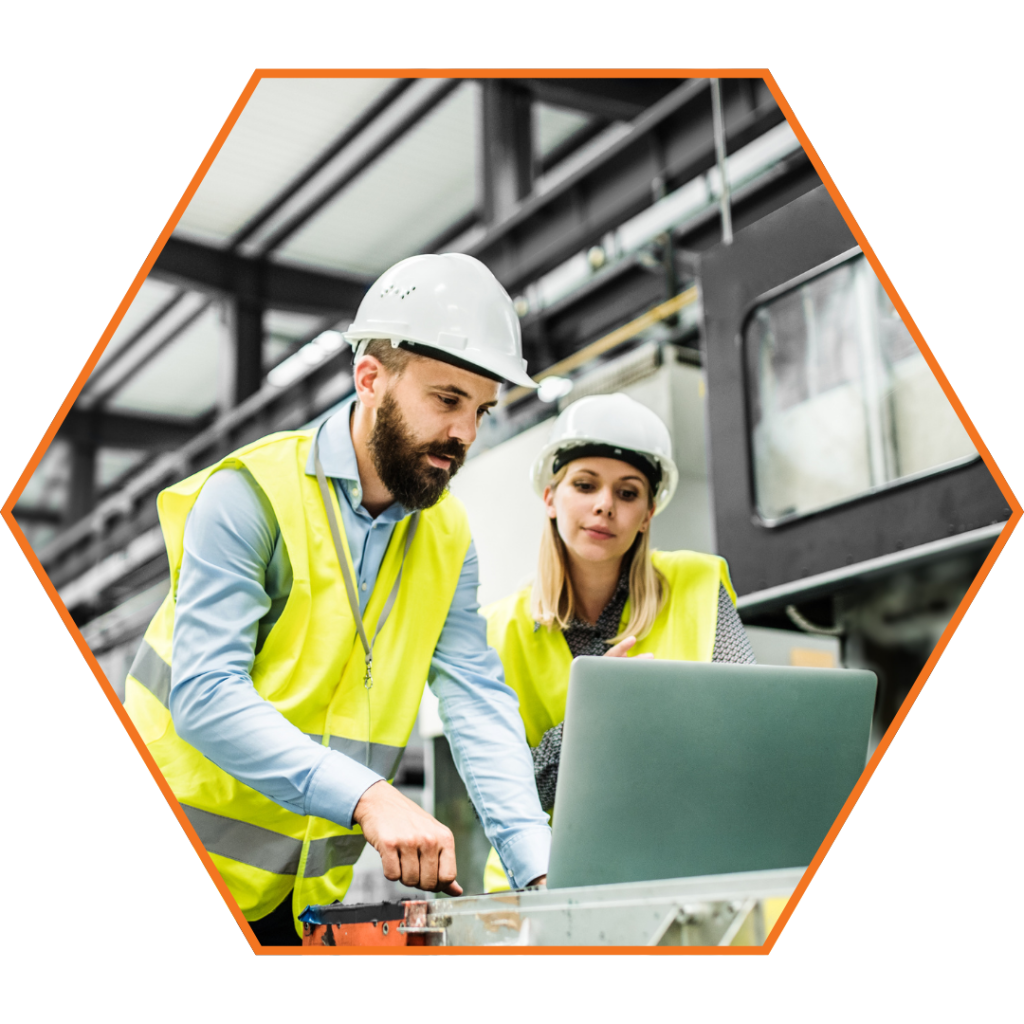
Why it happens: Many food and beverage manufacturing plants lack a centralized system to collect, store, and analyze maintenance history.
Predictive Maintenance Solution:
Store all maintenance records, alerts, and historical trends in one system. Allow a variety of AI learning models to learn from past failures, identify any repeat issues and build a maintenance strategy on data, not guesswork.
7: Inefficient Machines Operating on ‘Good Enough’
Smaller teams and tighter timelines leave little time for maintenance teams to keep everything running in top condition. However, the more things slide, the more it costs you in terms of energy consumption, decreased production, and reactive or emergency maintenance costs.
Predictive Maintenance Solution: Not only do predictive maintenance solutions identify when something isn’t running at full capacity, but it also identifies the costs of inaction and time you have until it fully breaks down.
Case Study: Learn how one company incurred a $625,000 cost of inaction by not doing anything.
Conclusion:
These 7 mistakes are common—but they’re also fixable.
With an advanced Energy-Centered Predictive Maintenances solution, you don’t just reduce breakdowns. You prevent spoilage, save energy, eliminate guesswork, and give your team the power to focus on what matters: producing high-quality product, profitably.
? Ready to protect your plant’s ROI and run smarter – grab our feature sheet below!