Energy-Centered Predictive Maintenance for Food & Beverage
Unplanned downtime and increasing sustainability pressures are critical challenges in today’s food and beverage industry. Nanoprecise delivers IoT-driven, AI-powered predictive maintenance solutions (PdM) designed for the hygiene-sensitive, high-throughput environments of food and beverage production.
Trusted by manufacturers across the sector, our platform helps reduce equipment failures, ensure consistent product quality, and minimize the environmental impact of sudden shutdowns.
Explore our case studies and brochure to see how we’re helping food and beverage manufacturers stay efficient, compliant, and sustainable.
Food and Beverage Industry Maintenance Challenges
Preventing Contamination through Human Intervention
Adhering to stringent quality and health norms, coupled with maintaining rigorous safety standards, is a paramount challenge in the food and beverage industry. Ensuring that human intervention, including data collection methods to monitor equipment condition aligns seamlessly with these standards becomes a critical aspect of preventing contamination risks.
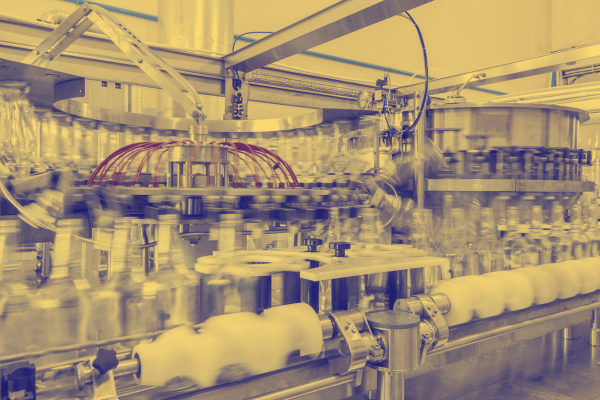
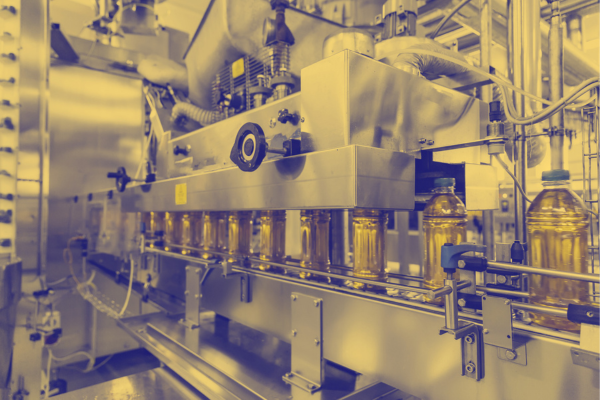
Unplanned Downtime and Batch Loss
Unplanned downtime poses a significant challenge in the food and beverage industry, potentially resulting in lost batches and disrupting carefully orchestrated production schedules. This critical issue demands a proactive approach that can mitigate the impact of unforeseen issues and enhance the overall operational resilience of manufacturing processes.
Manual Data Analysis
The reliance on manual data analysis, particularly in tasks like vibration analysis, presents a notable challenge for the food and beverage industry. This process demands a high level of expertise and experienced maintenance teams to accurately interpret the collected data. Moreover, the associated costs of vibration monitoring equipment, coupled with the necessity for regular maintenance and calibration, contribute to an increased overall cost of upkeep. Addressing this challenge is crucial for optimizing maintenance processes and achieving cost efficiency in the industry.

Case Study: $250,000+ in Downtime Avoided at a Leading Dairy Processing Plant with Energy-Centered Predictive Maintenance
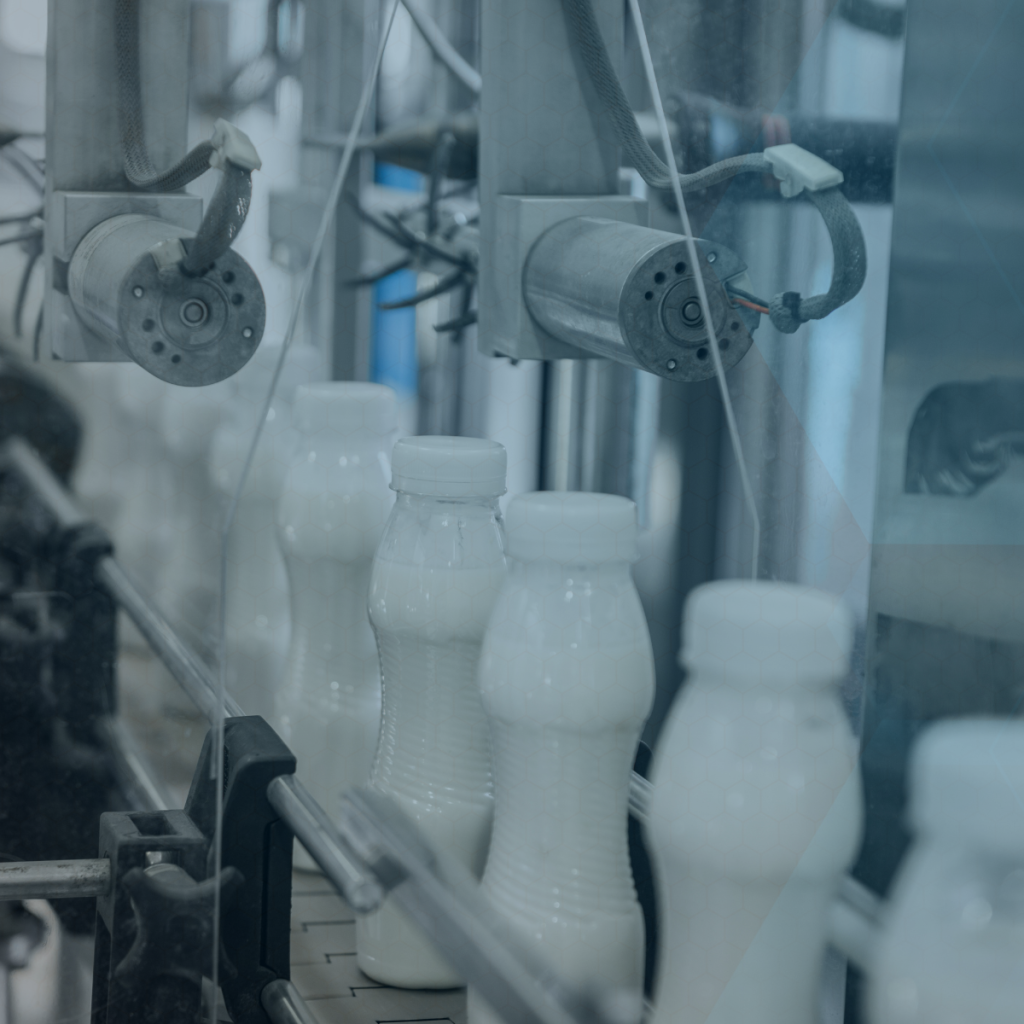
A leading dairy product manufacturer in North America faced high risks from hidden faults in critical machines (especially with many located in remote or hard to reach areas), leading to reactive maintenance and potential production losses.
To address this, our MachineDoctorâ„¢ 6-in-1 wireless sensors were deployed across key assets, including motors, pumps, and blowers. The system provided real-time fault detection and AI-powered Remaining Useful Life (RUL) insights.
When unbalance was detected on a 30 HP motor powering a Reverse Osmosis (RO) pump, a Stage 4 fault alert was triggered. This early warning enabled timely corrective action. This prevented over 16 hours of unplanned downtime!
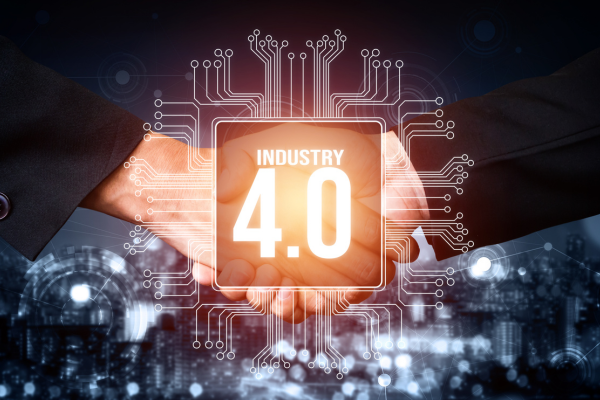
Let us show you how!
Our cutting-edge solutions are tailored to address the unique challenges faced by your industry, ensuring the highest standards of quality, safety, and operational efficiency. By seamlessly integrating with your processes, we empower manufacturers to eliminate unplanned downtime, reduce their carbon emissions and improve their overall operational efficiency.